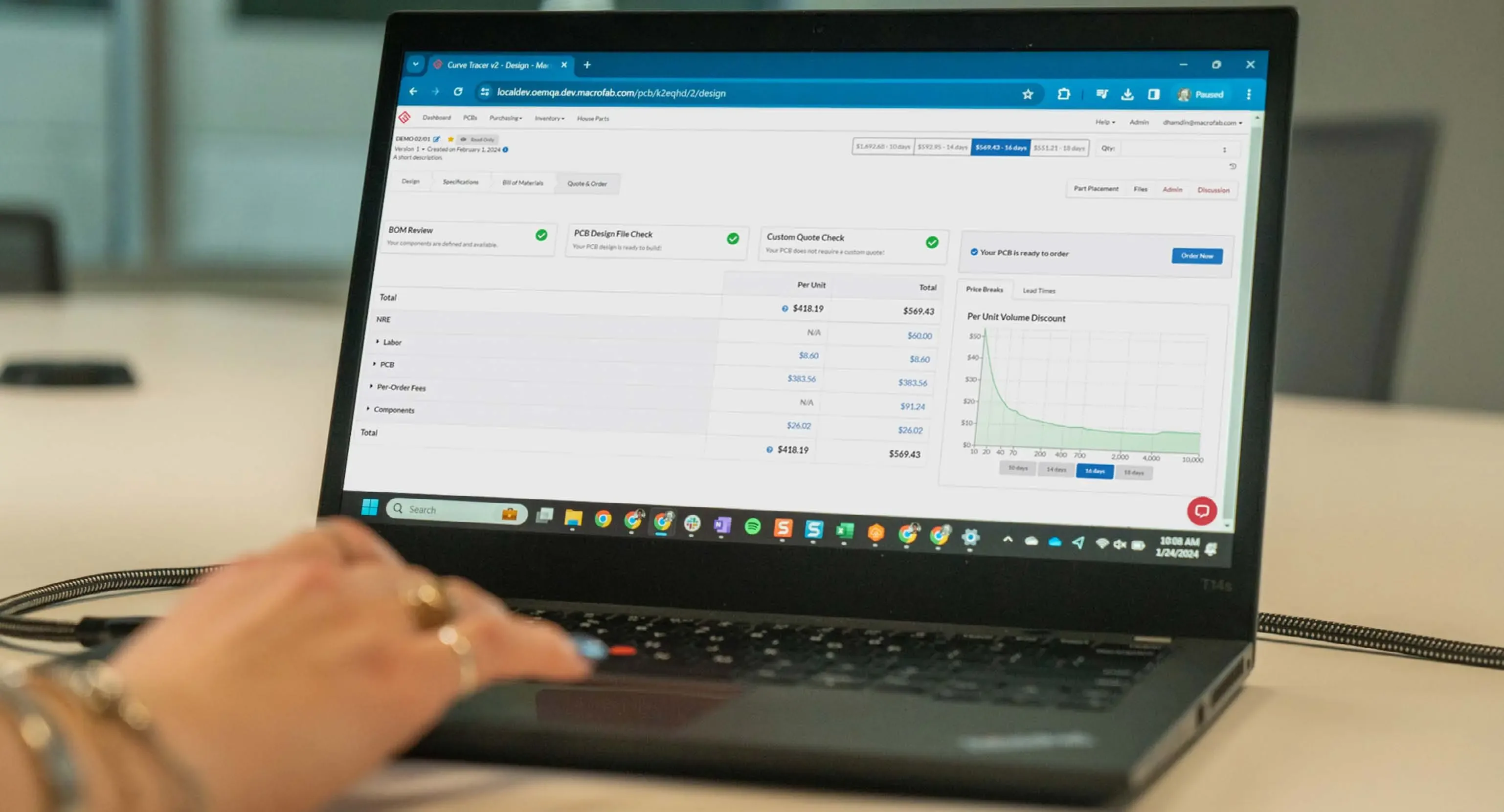
MacroFab Blog
The manufacturing of the first revision of your new prototype is a critical step in the product’s development process. To make sure your prototype has the greatest chance of success the first time, it’s essential to be prepared and follow a pre-order checklist to avoid any last-minute surprises.
In this article, we will outline the steps you should take to get your prototype ready for manufacturing.
Verify Parts and Component Selection
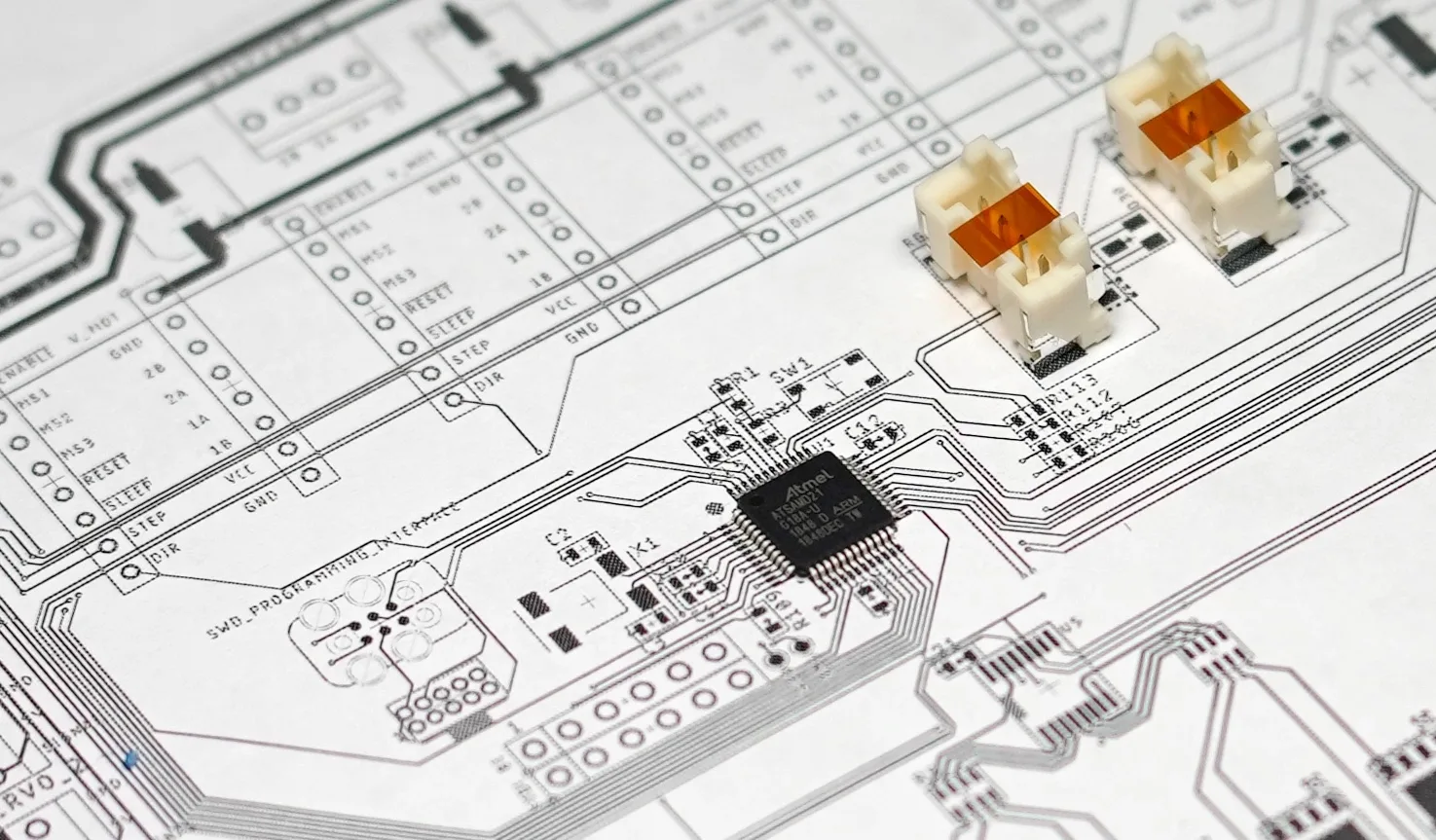
The first step is to verify your parts and component selection. This involves checking footprints, packages, and pinouts for various components like voltage regulators, transistors, and diodes. Additionally, verify the mechanical layout of the parts according to the datasheet drawings and double-check all unverified footprints to match the parts package.
An old-school but still valid way to check the mechanical layout is to print your footprints or PCB out on paper (while making sure you are 1:1 scale!) and then laying your component over the printout to check alignment. A more modern application of this strategy is using 3D models of the component to verify physical layouts.
PCB Layout Verification
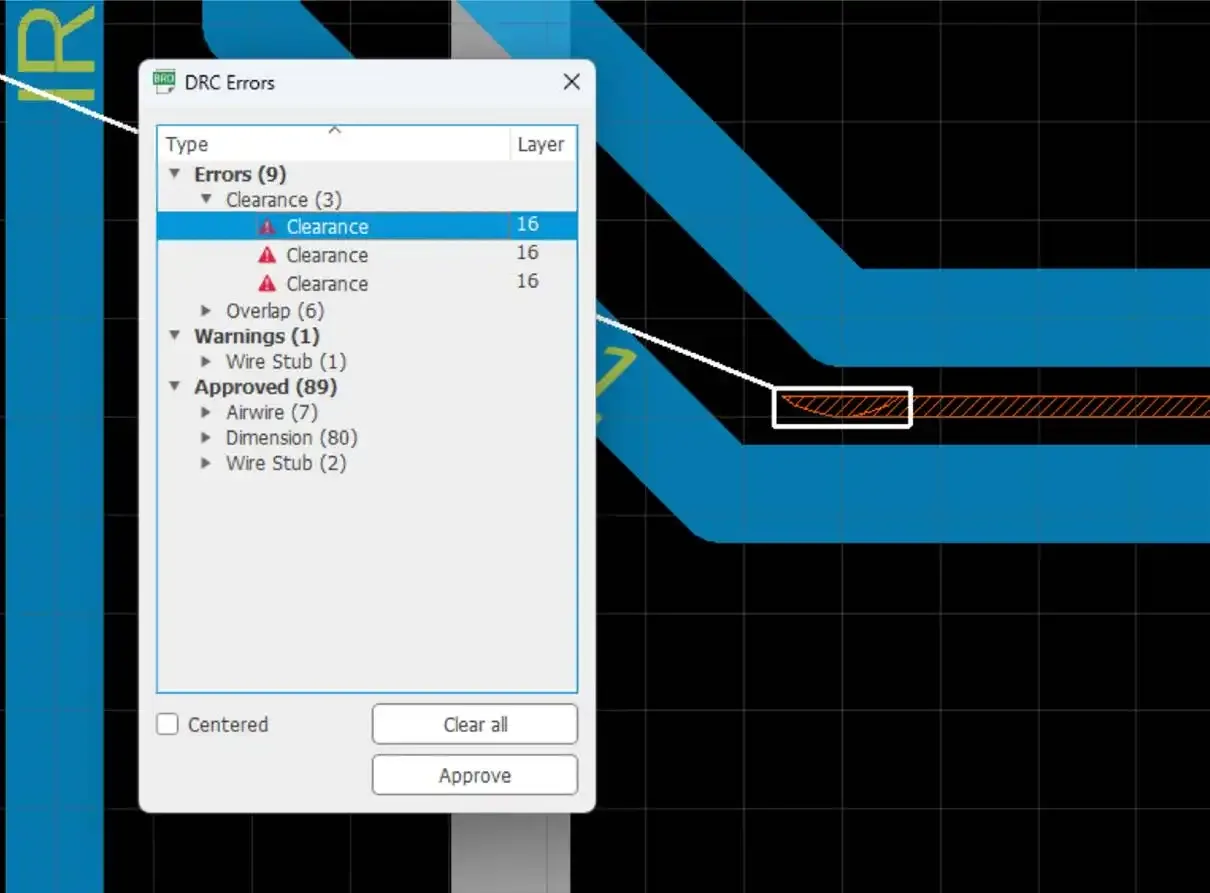
Utilize your design software’s Design Rule Check (DRC) tools to validate your PCB layout against the specific manufacturing guidelines, such as those provided in MacroFab’s manufacturing knowledge base. This step is crucial for confirming your design adheres to the necessary tolerances and that all electrical connections are correctly established and routed.
Additionally, take the opportunity to update the silkscreen layer with essential details like date codes, PCB version numbers, and any relevant metadata. This not only aids in traceability and version control but also ensures all necessary information is accurately represented on the PCB itself.
Assessing Component Selections and Strategizing Substitutions
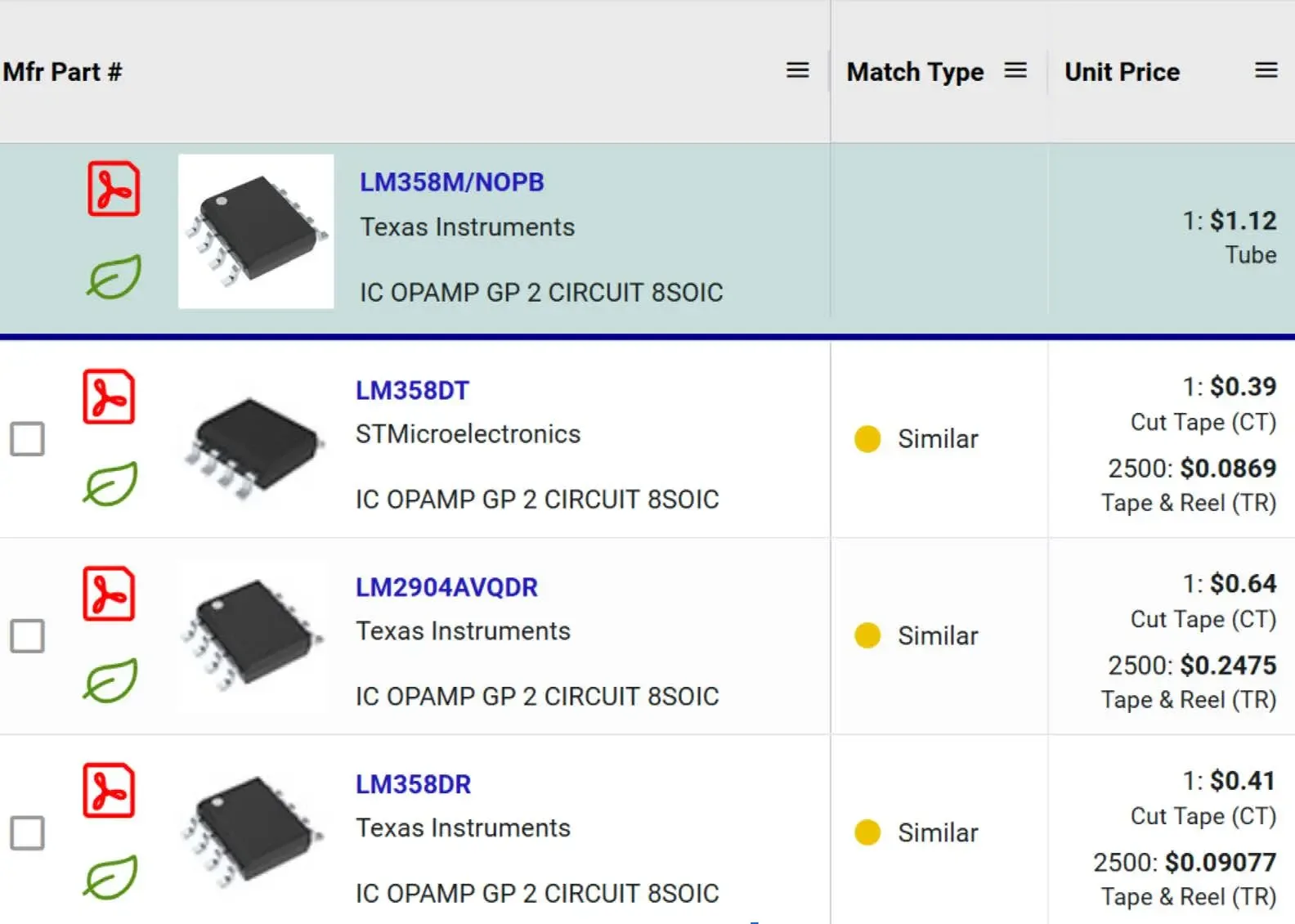
Carefully review your component selections to ensure they meet current and future project requirements. Distinguish between passive components (like resistors and capacitors), which often have readily available substitutes, and active components (such as MOSFETs, op-amps, and microcontrollers), where finding equivalents can be challenging due to specific performance characteristics or firmware porting problems. Develop a list of primary and alternative components, emphasizing the importance of compatibility and performance to avoid design compromises. Establishing what specifications are
important for each component during initial component choices will help accelerate alternative selections.
Additionally, assess the lifecycle and availability of each component to preempt stock issues and manufacturing delays. This involves verifying whether components are actively produced, estimating lead times, and identifying multiple sourcing options. By doing so, you can mitigate risks associated with component shortages and ensure a smoother manufacturing process with less downtime. A proactive approach to component selection and substitution can significantly enhance the feasibility and lifespan of your product.
Prepare Your Manufacturing Files
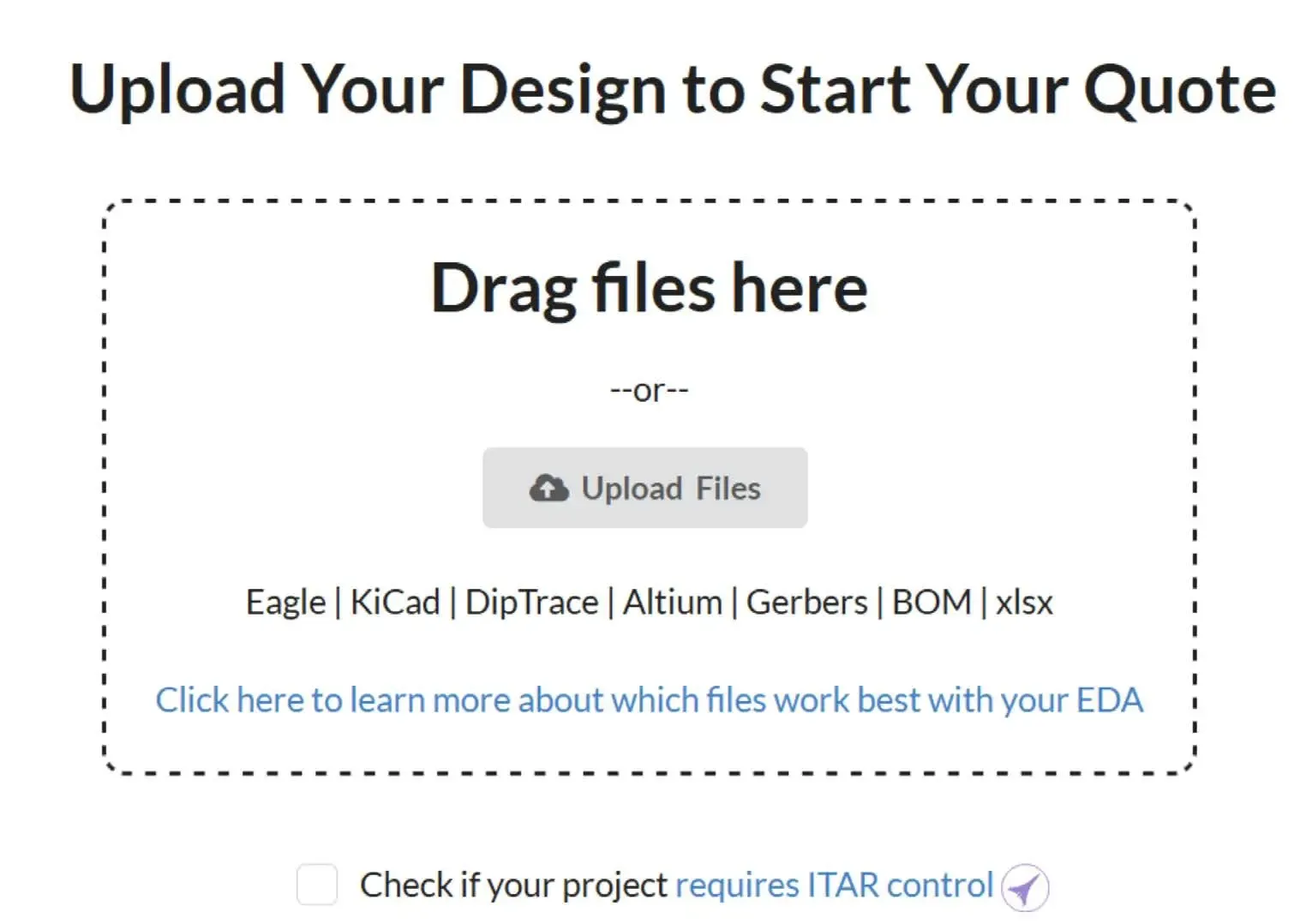
Transitioning from PCBA design to manufacturing hinges on creating accurate and complete manufacturing files. This set includes Gerber files, a Bill of Materials (BOM), a Placement file, and the physical PCB specifications. These documents are pivotal for ensuring your PCBA will be manufactured accurately and efficiently.
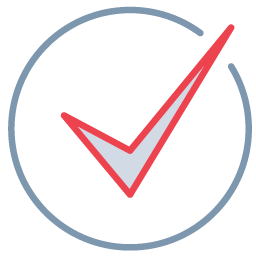
Checkpoint
MacroFab has design help based on the EDA program you use to create your PCB assembly.
Preparing each of these critical files varies depending on which Electronic Design Automation (EDA) tool was used to design the PCB assembly.
MacroFab has design help based on the EDA program you use to create your PCB assembly.
MacroFab supports the uploading of Gerber files, ODB++ packages, and native EDA tool files to reduce the problems of exporting and managing manufacturing data. Finally, MacroFab allows you to standardize your PCB specifications which reduces the problems of scaling your prototypes to production-level quantities. No more missed or incorrect specifications when switching fabrication shops!
Bill of Material and Placement Verification
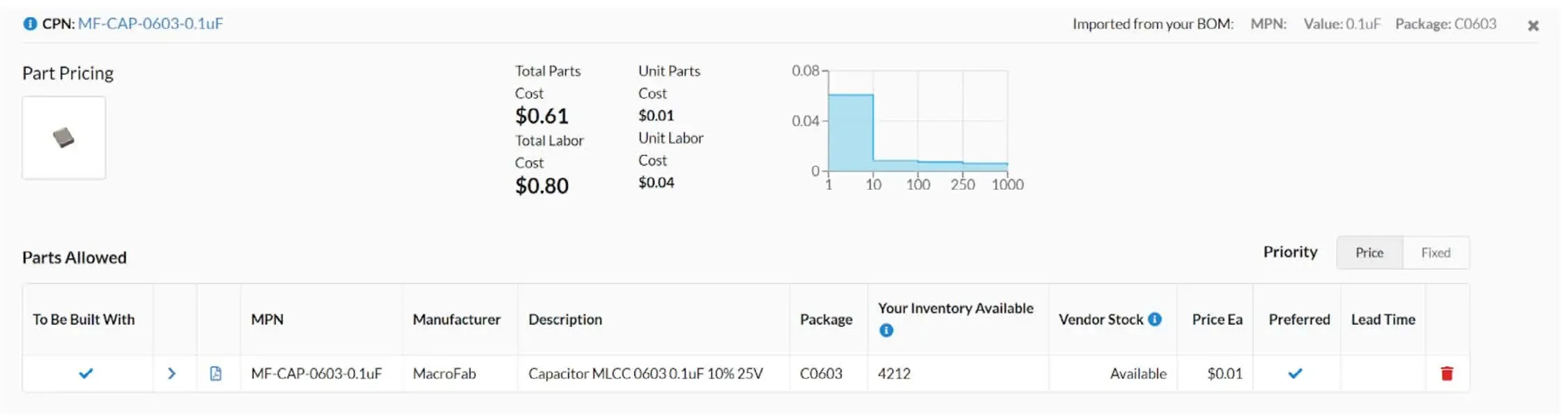
Make sure all parts required for your project are listed accurately in the Bill of Materials (BOM). Additionally, sourcing components from reliable and correct
sources is crucial for maintaining the integrity of your PCBA design. This step
helps in avoiding potential delays and increases the reliability of the procurement process.

Beyond the mere listing of parts, the BOM should also include specific annotations regarding component orientation and placement on the PCB. This is especially important for polarized components or those with a specific orientation, such as diodes, capacitors, and ICs. Including detailed notes on these aspects can greatly assist the assembly team, reducing the risk of errors during the manufacturing phase.
Furthermore, for parts requiring special handling or having unique assembly
instructions, adding clear and concise notes next to the respective components in the BOM can provide invaluable guidance. These proactive measures ensure the assembly process is smooth, efficient, and free from avoidable mistakes, ultimately contributing to the success of your PCBA project.
Order Your Prototype with Confidence
By adhering to the detailed steps outlined in this pre-order checklist, you’re setting the stage for a smooth and successful prototype manufacturing process that will enable you to scale in volume. This approach minimizes the likelihood of common pitfalls, ensuring your PCB assembly project advances from conception to completion with precision and efficiency.
As you prepare to place your order, take a moment to meticulously review your PCB specifications and the Bill of Materials (BOM) on the quote and order page. Platforms like MacroFab enhance this process by automatically flagging any discrepancies or issues within your files, and offering corrective suggestions to refine your order further.
Upon finalizing your order, remember to coordinate the timely shipment of any consignment or inventory parts, ensuring they match the specified packaging requirements and include the necessary overage to account for the assembly process. This proactive engagement not only streamlines the manufacturing workflow but also reinforces your confidence in the forthcoming prototyping
phase.
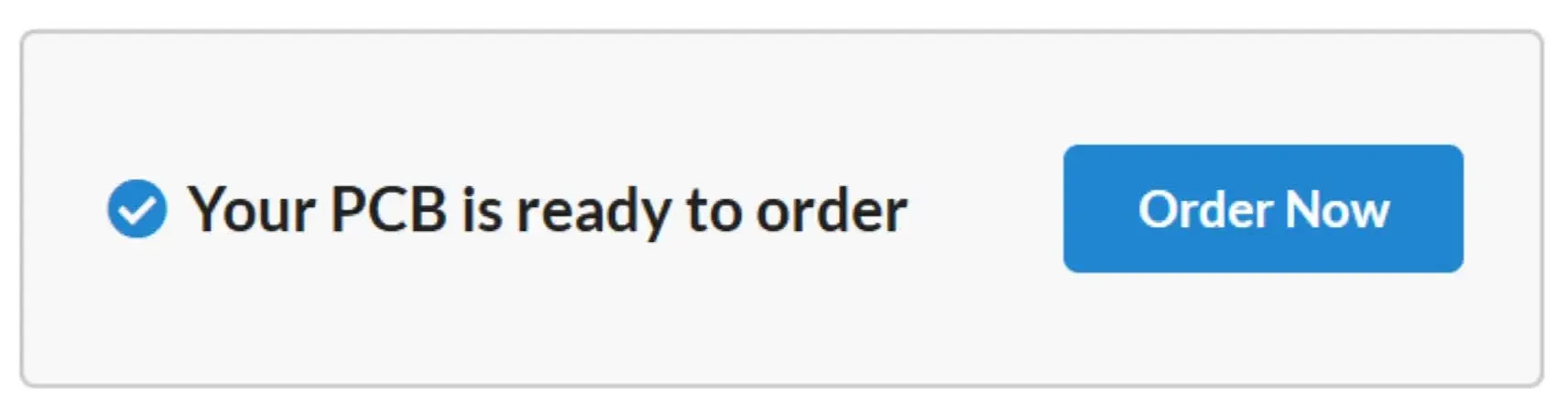
As you anticipate the arrival of your PCBAs, consider sharing your journey and insights gained through social media to inspire and inform others in the prototyping community. Embrace this phase of your project with optimism and readiness for the innovative discoveries that lie ahead. Happy prototyping!
Related Topics
How MacroFab Uses Clear Communication to Improve Your PCB Production Experience
This blog will discuss how MacroFab can help customers in their PCB production experience through clear communication in a high-octane environment.
Improve Your Next PCB Prototype: Better Debugging, Testing, and Reliability
Learn how to improve your next PCB prototypes as engineers push the boundaries of hardware technology to enhance debugging, testing, and general liability
Expert Tips for High-Speed Backplane PCB Design
Improve your high-speed backplane bus reliability with expert design tips.
Ready to get started?
Get An Instant Quote NowAbout MacroFab
MacroFab offers comprehensive manufacturing solutions, from your smallest prototyping orders to your largest production needs. Our factory network locations are strategically located across North America, ensuring that we have the flexibility to provide capacity when and where you need it most.
Experience the future of EMS manufacturing with our state-of-the-art technology platform and cutting-edge digital supply chain solutions. At MacroFab, we ensure that your electronics are produced faster, more efficiently, and with fewer logistic problems than ever before.
Take advantage of AI-enabled sourcing opportunities and employ expert teams who are connected through a user-friendly technology platform. Discover how streamlined electronics manufacturing can benefit your business by contacting us today.