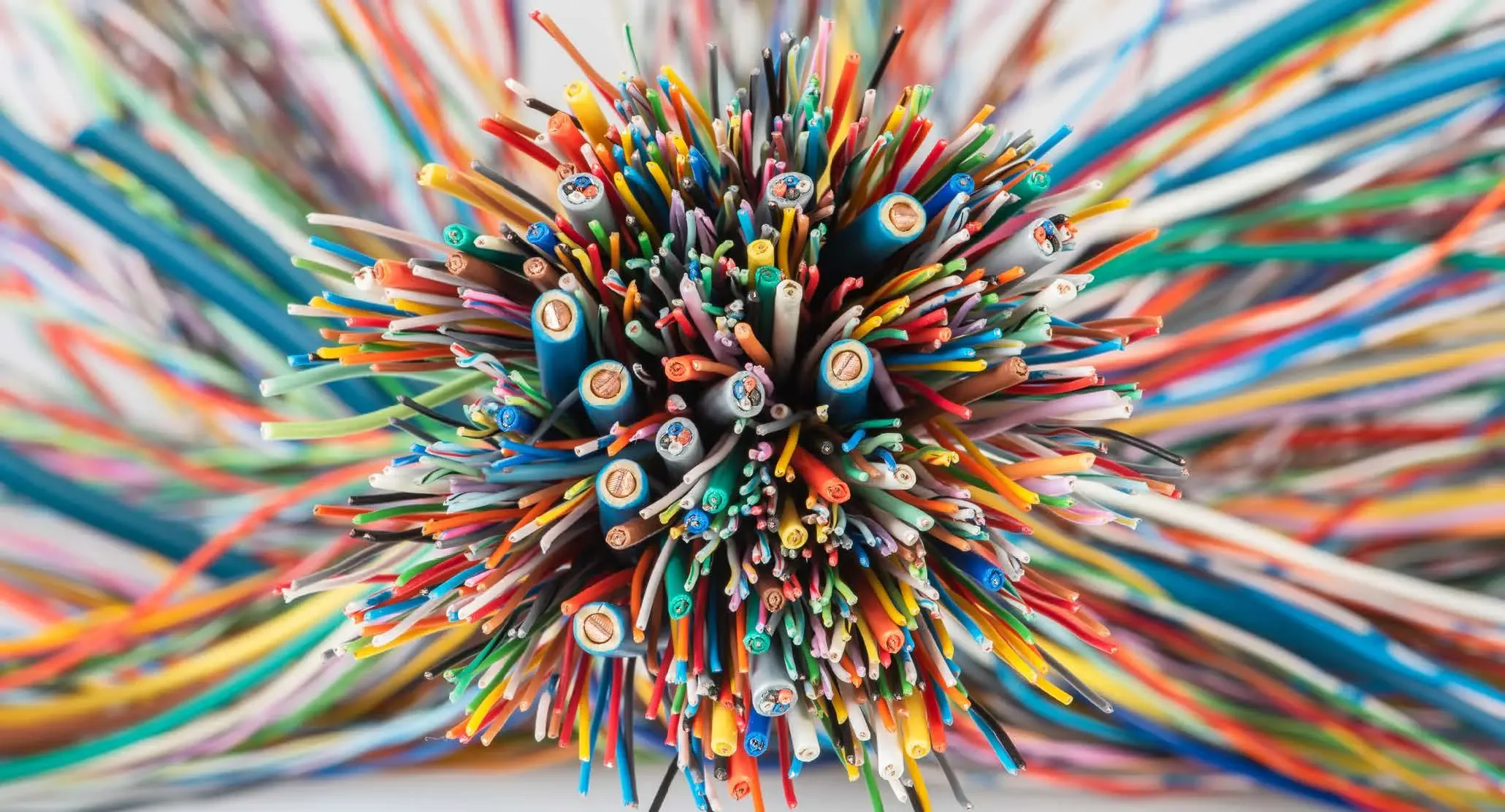
MacroFab Blog
Cable assemblies and wire harnesses are integral to electronics manufacturing, especially in PCBA box builds. Both are necessary for connecting and integrating components and systems. However, cable assemblies and wire harnesses serve distinct purposes that must be understood for good PCBA design.
A wire harness is essentially an organized grouping of wires or cables, either encased in a cost-effective, lightweight protective sheath or simply bound together with cable ties. Its primary role is organizational, consolidating multiple electrical wires into one unit for space efficiency and secure, neat routing.
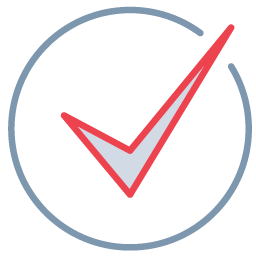
Checkpoint
Cable assemblies and wire harnesses serve distinct purposes that must be understood for good PCBA box build.
In contrast, cable assemblies are bundled wires or cables protected by a robust outer layer, and act as transmission lines for signals or power between different parts of a system or between systems.
A PCBA box build, also known as systems integration, refers to the assembly of a complete electronic product. Within this process, the careful integration of cable assemblies and wire harnesses is essential for ensuring dependable connections, protecting against environmental factors, and transmitting signals accurately. This article will focus on these components and compare their roles in modern electronic assembly.
What is a Wire Harness?
At a high level, a wire harness assembly is a collection of wires or cables designed to transmit signals or electrical current. It is a method of organizing and routing wires within complex electronic systems.
As part of this bundled group, certain wires or cables may branch from the main group at certain points. This branching allows the wire to connect to a particular component or terminal within the system. These branching points are referred to as “active breakouts” or ends.
Additionally, for protection, this entire group of bundled wires, including the branch-out points, is often encased in a lightweight protective sheath.
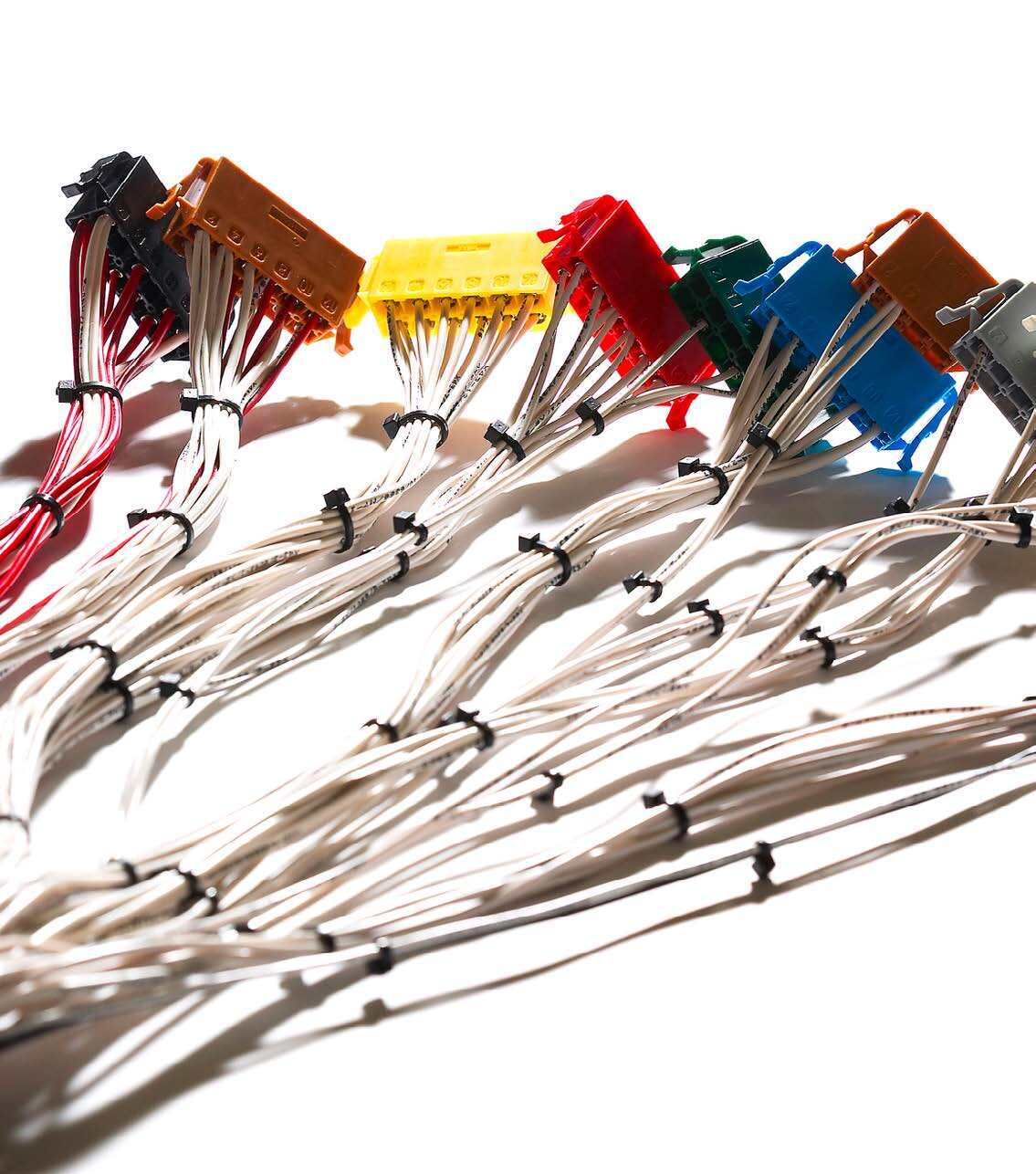
Basic Components of a Wire Harness
A wire harness is primarily made up of three essential parts: the wires, connectors, and housing or protection.
Wires and cables
A wire is a flexible conductor, which may or may not be insulated, used as a common pathway to transmit electrical signals or power from one point to another. Cables, on the other hand, begin with two or more wires bundled together Cables are more flexible than wires due to their multiple wires, and can transfer higher amounts of electricity.
When shopping for wires and cables for your wire harness design, familiarity with industry-specific jargon is crucial. Below are some key terms associated with wires and cables:
- Wire Diameter: Refers to the overall thickness of a wire. It’s the sum of the conductor’s actual diameter and the insulation’s thickness.
- American Wire Gauge (AWG): A standardized system used predominantly in the United States to denote wire or cable thickness.
- Standard Wire Gauge (SWG): This is the British counterpart to AWG.
- Braid: A structure created by weaving together thin metallic strands, often copper. This woven pattern serves as a conductor and is known for its strength and durability, making it apt for demanding applications.
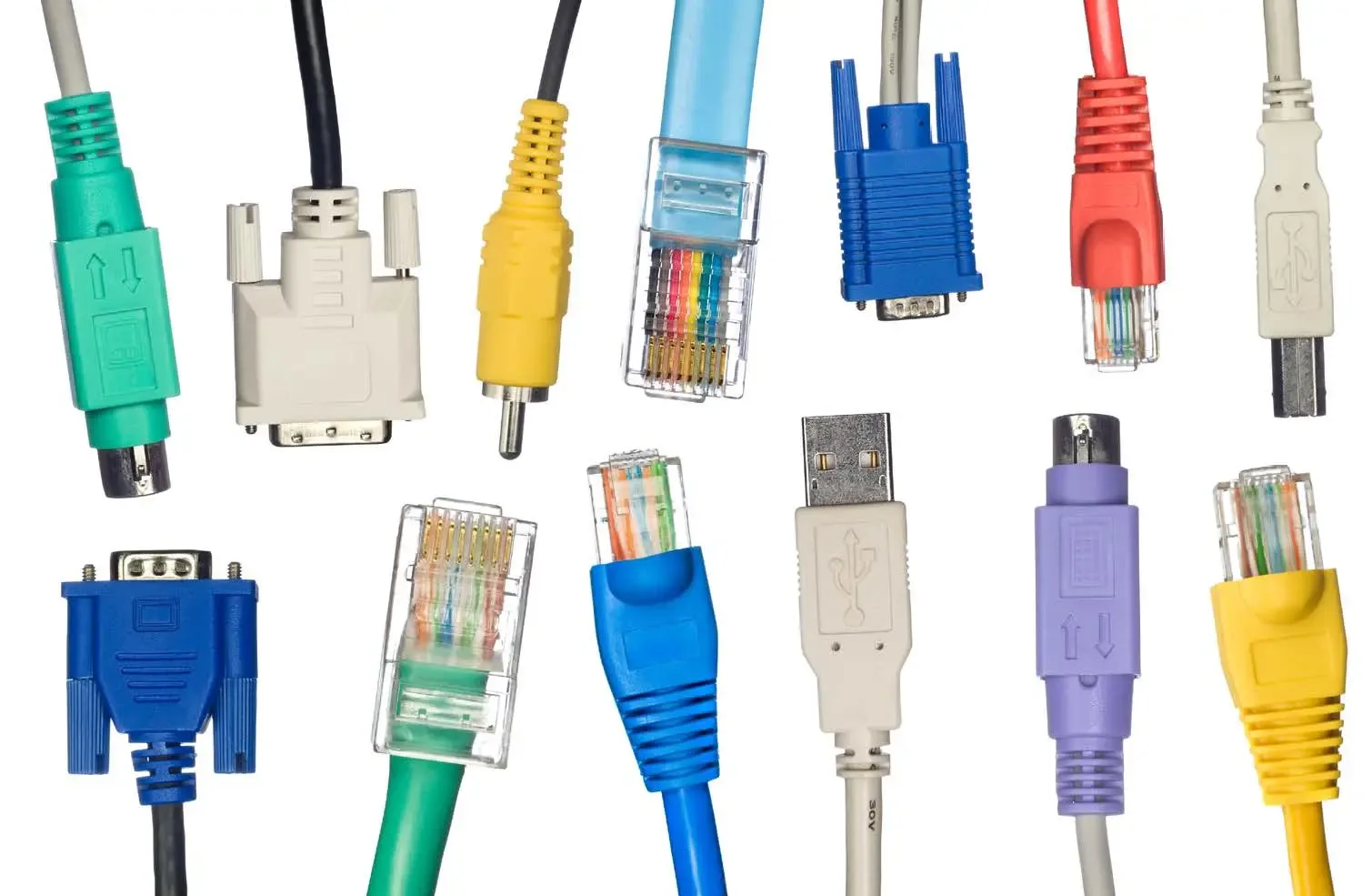
Connectors
Connectors, as the name suggests, facilitate the connection of these wires to other components or systems, ensuring a seamless flow of electricity. They come in two primary types: plugs and receptacles. Plugs are the male connectors, meant to be inserted into their female counterparts, the receptacles.
A connector typically has a front part, where the actual connection between plug and receptacle takes place, and a back part which attaches to the wire or cable, providing a secure and stable connection.
When dealing with connectors in wire harness assemblies, several terms are commonly used:
- Contacts: These are the actual conductive parts within the connector, facilitating the electrical connection.
- Cable Ties: Also known as zip ties or tie wraps, these are fastening devices used to bundle wires and cables together.
- Mating Cycle: The number of times a connector can be connected and disconnected while still maintaining its functionality.
- Polarization: Features designed into the connector to prevent wrong-way insertion.
- Strain Relief: A design feature or component that prevents wires from bending at extreme angles at the connector’s entry point, reducing the risk of wire damage or disconnection.
- Terminal: The end part of a wire where it makes a connection.
- Ring Terminal: A type of connector that is shaped like a ring, making it easy to attach to a screw or stud. It’s commonly used for grounding purposes or making connections to busbars and components with stud-style terminals.
- Loose Terminal: Individual terminal connectors that aren’t pre-inserted into a housing or connector body. They offer flexibility during assembly as they allow for custom connector configurations.
- Assembled Connector: a connector that has been pre-assembled, meaning it already has terminals inserted into a housing. It speeds up the PCB box build assembly process.
- Bellmouth: A flared or widened entry of a terminal, making wire insertion easier and reducing the risk of wire damage during insertion.
- Crimp: A method of joining a terminal to a wire by deforming or “pinching” them together, creating a secure mechanical and electrical connection.
- Double Crimp: The compression of two or more wire barrels at a single terminal.
- Crimp Height: Refers to the height or thickness of the terminal after it has been crimped onto the wire. It’s an essential metric to ensure a good quality crimp connection.
Protection
A wire harness assembly, while facilitating the transmission of signals or power, also exposes its components to various environmental and operational hazards. Among these, corrosion, stress, strain, and electromagnetic interference (EMI) are most prevalent.
Exposure to moisture and corrosive substances can result in the corrosion of wires and terminals. Such corrosion can introduce high resistance and impedance mismatch, hindering efficient power transfer and potentially causing system breakdowns.
Furthermore, during the lifecycle of a wire harness, mechanical stress from installation maneuvers or regular operation—like pulling, bending, or twisting—can wear out connectors and cables. This strain is particularly detrimental at the connection points, risking disconnections or wire breaks that interrupt the electrical pathway.
Additionally, every electrical device releases a certain degree of electromagnetic radiation. This radiation, when it interferes with another device’s operation, is labeled as Electromagnetic Interference (EMI). In essence, EMI prompts wires or cables to inadvertently receive unwanted electrical signals. This unintended reception can disturb the wire’s own signals and jeopardize the performance of sensitive electronic systems.
- Protection of Wires:
- Insulation: Most wires are coated with an insulating layer that not only prevents electrical leakage but also provides a first line of defense against environmental hazards like moisture or chemicals.
- Shielding: Especially for wires susceptible to EMI, a shielding layer, often made of braided copper or a metallic foil, surrounds the wire, preventing external electromagnetic fields from disturbing the signal within.
- Conduits and Sleeves: In extremely harsh environments, wires are encased in conduits or protective sleeves that provide an added layer of protection against mechanical or environmental damage.
- Protection of Joints and Connections
- Sealed Connectors: These are designed to keep out moisture, dust, and other contaminants. They play a vital role in preventing corrosion at the connection points.
- Strain Reliefs: Integrated into connectors, these prevent undue stress on the wire at its joint, reducing the risk of wear and tearor disconnection.
- EMI/RFI Filtering: For connections especially vulnerable to electromagnetic or radio frequency interference, connectors with built-in filters can be used to block unwanted interference.
Different Types of Wire Harnesses
Wire harnesses vary based on application, environment, and material composition. Here’s a summary table of different types of wire harnesses.
The Difference Between Cable Assemblies and Wire Harnesses
While cable assemblies and wire harnesses both organize wires, they have key differences.
The table below offers a concise comparison of the similarities and differences between a wire harness and a cable assembly:
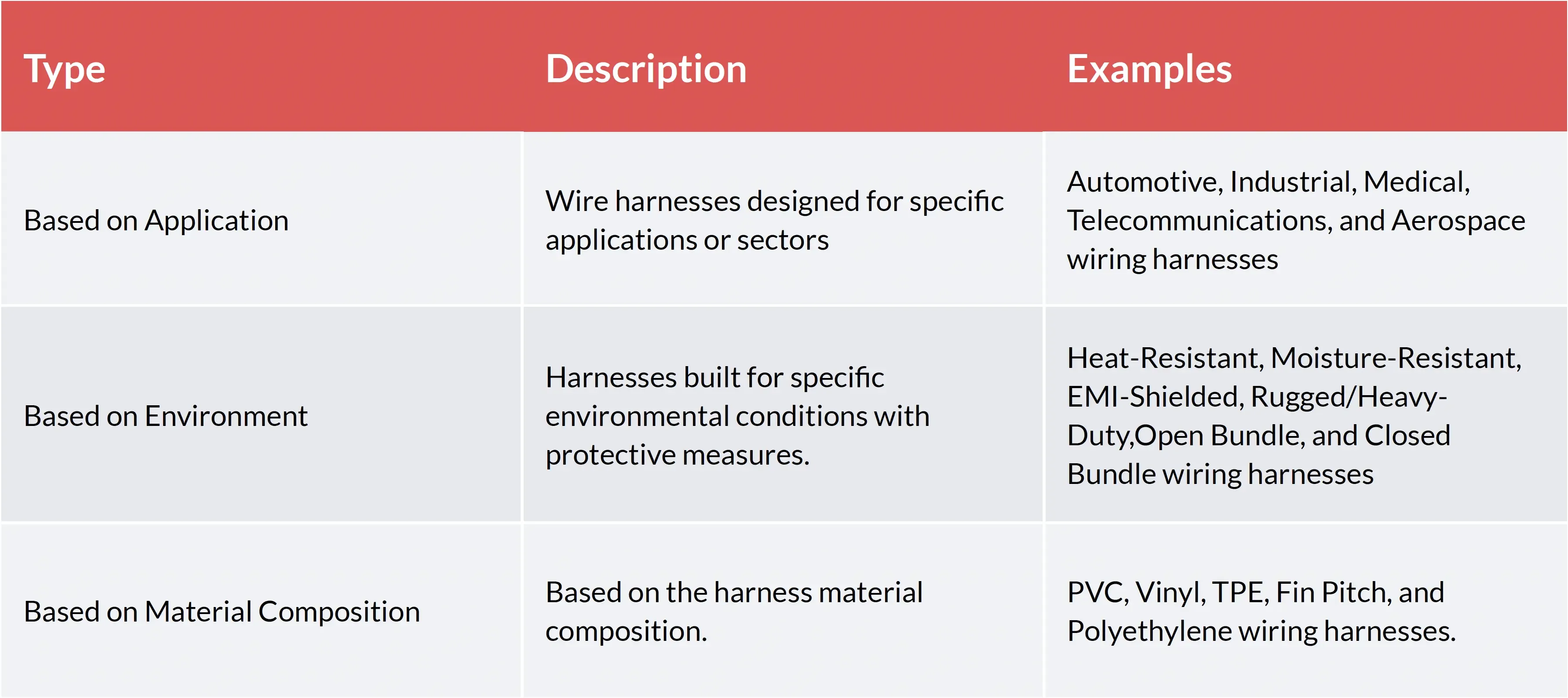
Table
What is a Cable Assembly
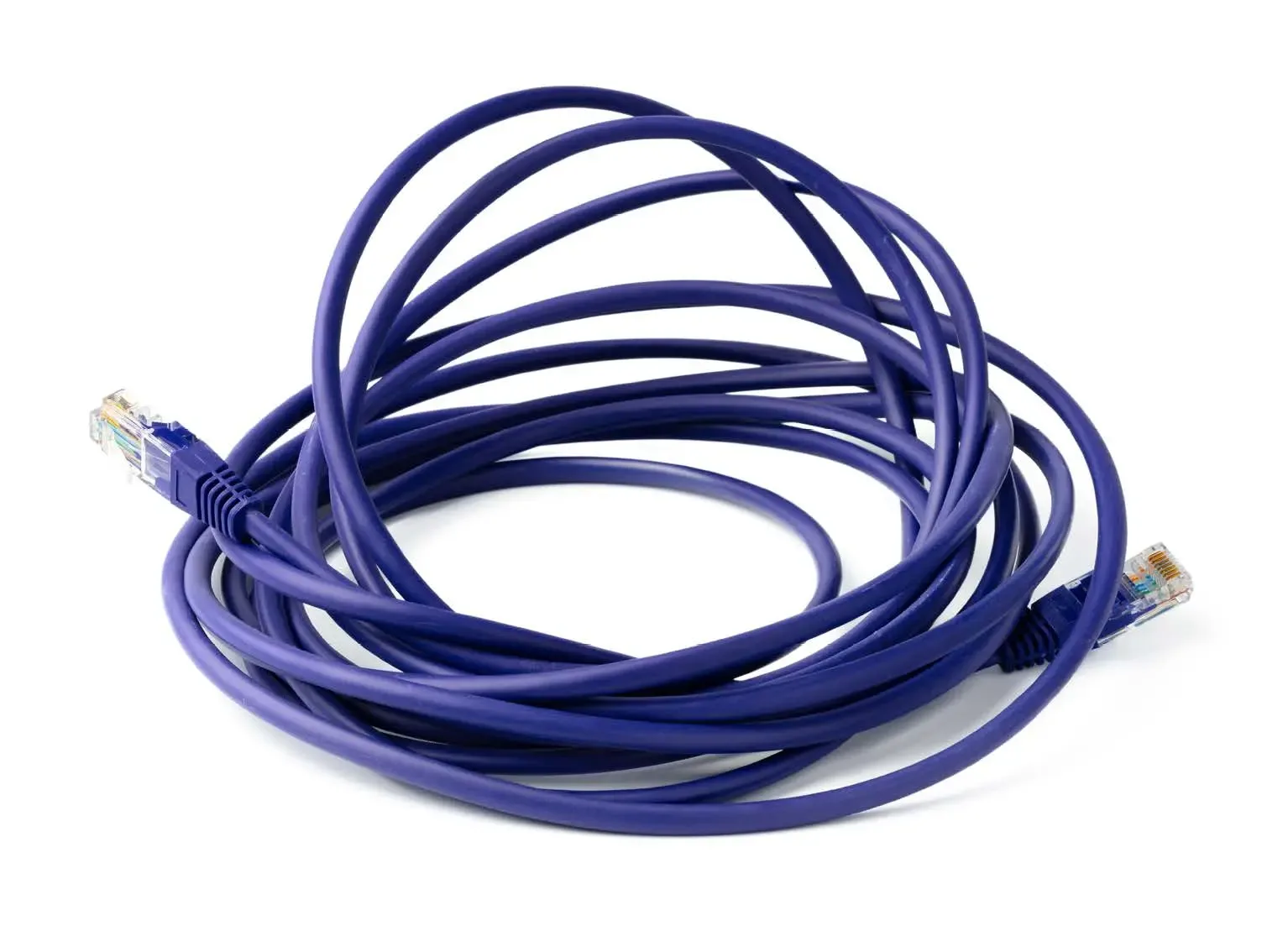
A cable assembly consists of multiple wires or cables enclosed within a singular protective sheath, typically made from rubber, vinyl, or pressure-extruded
thermoplastics such as polyurethane.
In contrast to wire harnesses, which bundle multiple individually sheathed wires or cables, a cable assembly integrates all its wires into one unified casing. Also, the protection layer used in a cable assembly offers a higher degree of protection compared to the sheathing
used in wire harnesses. This makes cable assemblies especially suited for extreme environments requiring enhanced protection.
Additionally, cable assemblies come equipped with multiple connectors at their active ends, facilitating connections to devices or other cables.
Different Types of Cable Assemblies
Similar to wire harnesses, cable assemblies are not one-size-fits-all. They are tailored to suit a variety of applications, industries, and environmental conditions. Below are some distinct types:
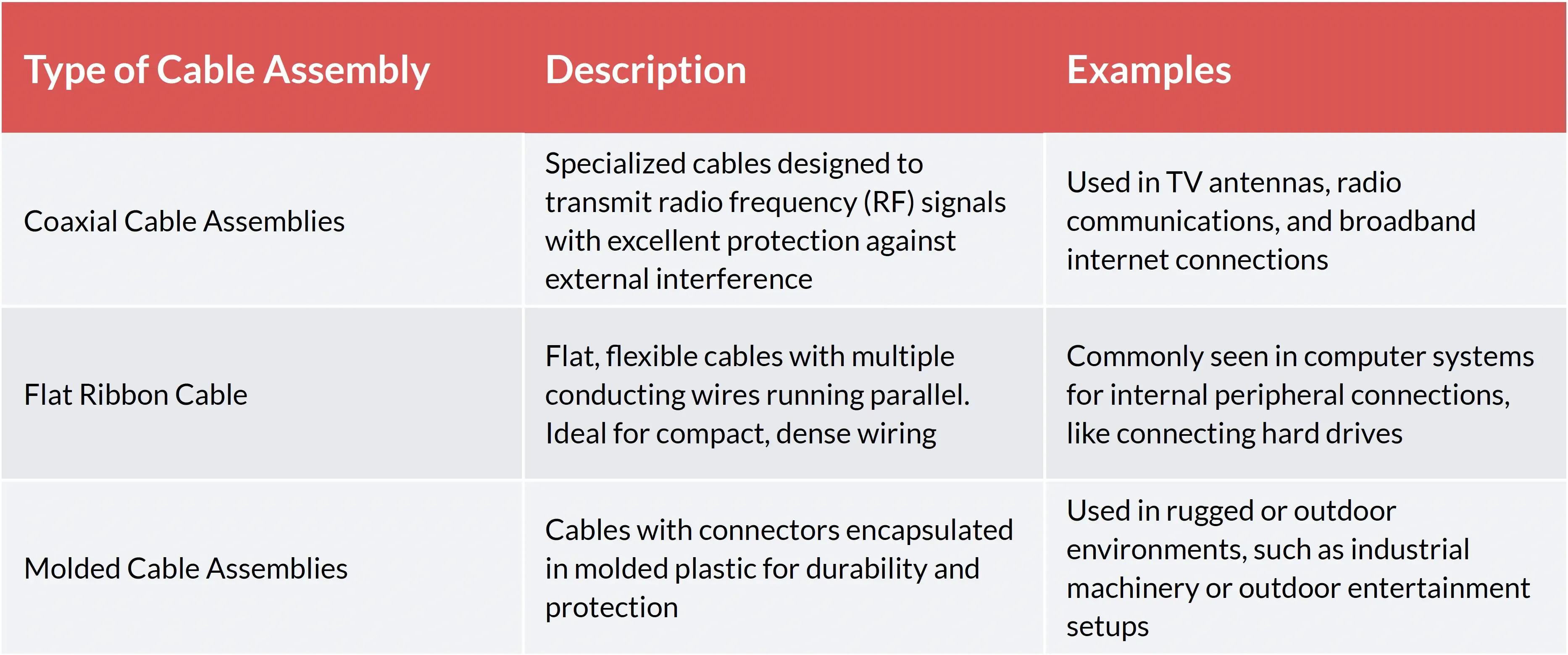
Cable Assembly
The Difference Between Cable Assemblies and Wire Harnesses
While cable assemblies and wire harnesses both organize wires, they have key differences.
The table below offers a concise comparison of the similarities and differences between a wire harness and a cable assembly:
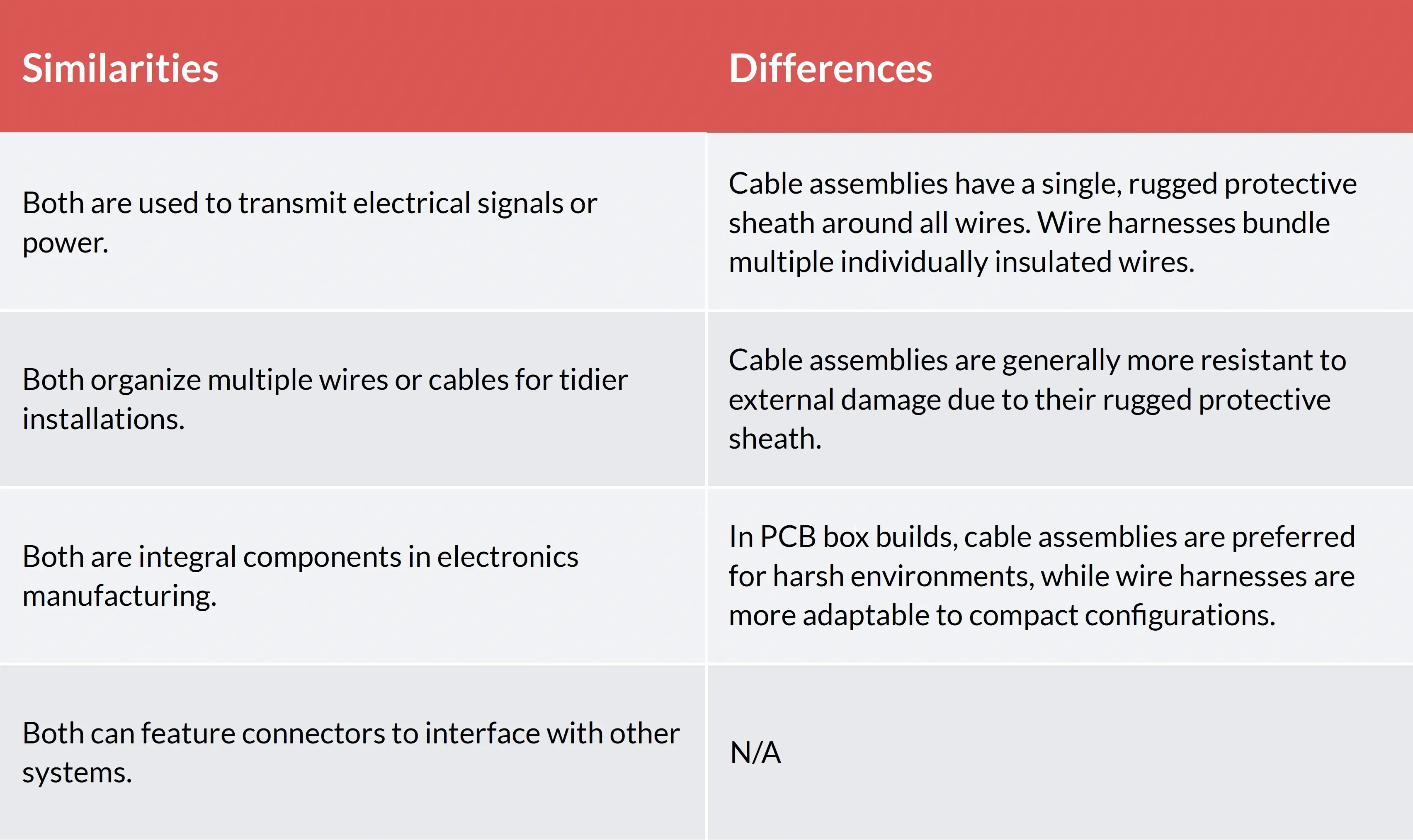
Applications for Cable Assemblies and Wire Harnesses
Cable assemblies and wire harnesses find their way into a multitude of applications, underlining their versatility and crucial role in a wide range of industries:
- Automotive Industry: Both cable assemblies and wire harnesses can be found in everything from the basic wiring systems that control lights and indicators to the more complex setups in modern vehicles, facilitating multimedia systems, navigation, and advanced driver assistance systems.
- Agricultural Industry: The modern agricultural sector heavily relies on machinery and equipment. Cable assemblies ensure these machines can withstand outdoor elements, while wire harnesses ensure that the internal electronics of these machines function seamlessly.
- Industrial and Manufacturing: In factories and production lines, wire harnesses and cable assemblies provide structured wiring setups that make maintenance easy.
- Military: Reliability is paramount. Both components ensure communication devices and navigation systems function consistently, even under extreme conditions.
In every mentioned sector, product success is deeply tied to the excellence and dependability of its PCBA box build. Central to this are wire harnesses and cable assemblies. They guarantee organized connections that withstand environmental challenges, and enhance overall functionality.
Therefore, correctly integrating these components in the box build process leads to long-lasting products, contented customers, and the ensuing sustainability and expansion of a business.
Conclusion
You might often hear cable assemblies and wire harnesses used interchangeably, but they fulfill distinct roles in electrical systems. Cable assemblies provide strong external protection and connectivity, while wire harnesses focus on optimizing internal organization and saving space.
Choosing the right cable assembly and wire harness can be challenging. If you work in the hardware tech industry, it’s imperative to understand these differences. When completing your box build, make sure to choose a company who can help you make the right decisions.
Related Topics
How Can a Box Build Benefit Your PCBA Design?
PCBA box build is a sophisticated process involving the design, production, and construction of an electromechanical system that goes beyond a PCBA.
Insider's Guide to Navigating Box Build PCBA Projects
This guide will help you become familiar with box build assembly, decide if it’s right for your PCBA project.
Looking for more than just a PCBA?
Learn about MacroFab’s Box Build Capabilities.About MacroFab
MacroFab offers comprehensive manufacturing solutions, from your smallest prototyping orders to your largest production needs. Our factory network locations are strategically located across North America, ensuring that we have the flexibility to provide capacity when and where you need it most.
Experience the future of EMS manufacturing with our state-of-the-art technology platform and cutting-edge digital supply chain solutions. At MacroFab, we ensure that your electronics are produced faster, more efficiently, and with fewer logistic problems than ever before.
Take advantage of AI-enabled sourcing opportunities and employ expert teams who are connected through a user-friendly technology platform. Discover how streamlined electronics manufacturing can benefit your business by contacting us today.