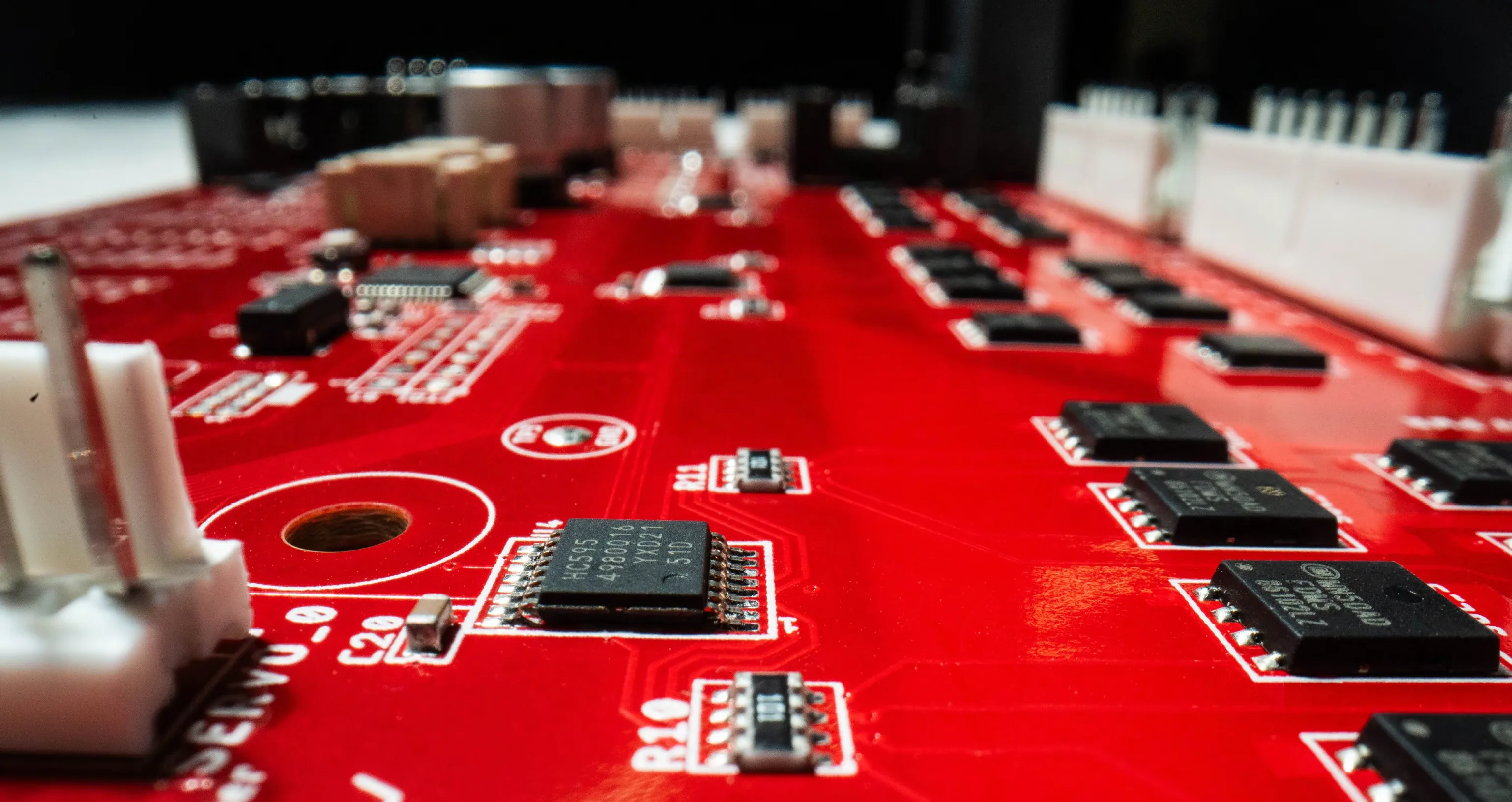
MacroFab Blog
Manufacturing services span a broad spectrum, but one stands out as a game-changer for hardware tech companies looking to streamline their logistics - box-build assembly.
At its core, box build assembly is the process of taking a PCBA and putting it into its final casing or enclosure, along with all the other components necessary to make a complete, functional product. This could include wire harnesses, interfaces, and any sub-assemblies that are required to make the finished product.
In some industrial products, box builds can be quite large, while in medical or commercial products, they may live in quite small enclosures. Depending on how complex they are, they can be either quite simple or very complex, requiring extensive planning and thoughtful design to integrate multiple PCBAs, cable assemblies, and other elements.
Choosing a PCB manufacturing service provider that also provides box-build assembly services can be a strategic move. As a client, you interact with a single supplier throughout the manufacturing process - from the initial component sourcing and PCBA production to the final product testing and packaging. This holistic approach can simplify the supply chain, potentially reducing costs and accelerating time-to-market.
However, box-build assembly isn’t right for every product. That’s why businesses must understand this service inside out.
This guide will help you become familiar with box build assembly, decide if it’s right for your PCBA project, and understand what information a service provider, like MacroFab, needs from you to deliver a high-quality end product.
Understanding Box Build Assembly
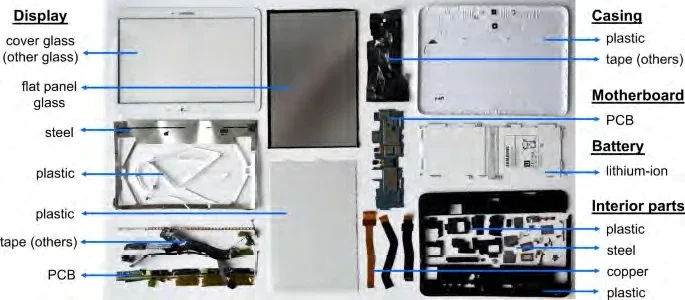
Example of product disassembly for a tablet (Samsung Galaxy Tab 4 SM-T530) to show all the necessary components for the final product. Image Courtesy of Disassembly-based bill of materials data for consumer electronic products.
The overall component set for box builds for commercial products, like the one above, and for other industries, like industrial, telecommunications, and energy sector devices, remains the same, although not all parts may be required for some builds.
Let’s break down these steps to understand this process better.
- Component Procurement: This involves purchasing and sourcing all the necessary parts to assemble the product.
- PCB Assembly: PCB components are soldered to the bare board surface by hand or by automated machinery.
- System Integration: The printed circuit board assembly and other parts get integrated into the product enclosure. This includes installing any sub-assemblies and other elements and wiring everything together. This assemblage makes up the ‘box build’ or integrated system.
- Testing: The assembled product is subjected to a series of tests. These tests ensure that the assembled product functions as expected and meets all the necessary performance and safety standards.
- Packaging: The finished product is packaged up and ready for shipping to the customer or end user.
Requirements: Why it’s Important to Discuss Them
When you engage a box build assembly service provider, they will typically ask for several key pieces of information and materials to ensure they can accurately build and test your product. Here are some common requirements:
- Bill of Materials (BOM): This is a comprehensive list of all the electronic components, parts, and assemblies needed to build your product. It should include information like part numbers, descriptions, quantities, and any necessary substitutes.
- Assembly Drawings: These provide visual instructions on how the product should get assembled. They can range from simple diagrams to complex 3D models, depending on the complexity of your product.
- Regulatory Compliance Requirements: If your product needs to meet specific safety or regulatory standards (such as FCC, CE, RoHS, etc.), you should provide these details upfront.
- Lead Times: Provide your preferred schedule, including any critical deadlines for prototype, pilot run, or mass production.
- Test Procedures: You’ll also need to provide the build assembly service provider with detailed testing procedures. This could include step-by-step instructions for functional testing, test points, expected outcomes, and any necessary test fixtures or equipment.
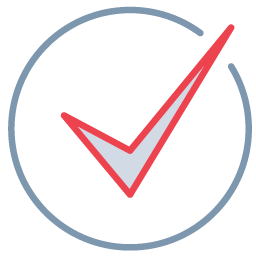
Checkpoint
Box build assembly involves putting a PCBA into its final casing or enclosure, along with all other elements needed to make a complete, functional product.
Understanding and communicating your project requirements to the PCBA contract manufacturer is more than just providing a list of components and an assembly guide. It’s about sharing your vision and expectations.
It aids in formulating an accurate quote, aligning expectations, and minimizing misunderstandings that can lead to costly delays. Your CM’s expertise can also offer invaluable insights for optimizing design and cost. In terms of regulatory compliance, discussing these requirements upfront ensures their integration into the assembly process.
Finally, such communication strengthens your relationship with the CM, fostering smoother projects, superior end products, and a long-lasting partnership.
The Role of Your Bill of Materials (BoM)
Your Bill of Materials plays an instrumental role in the box-build assembly process. Essentially, it serves as the DNA of your product, containing the details of every component that goes into the assembly.
The BoM informs, directs, and influences various stages of your project.
- Purchasing and Inventory Management: Your BoM is the primary source of information for purchasing decisions and inventory management. It dictates what components need to be purchased, and in what quantity, and may suggest preferred suppliers. By offering an overview of the required parts, the BoM helps in planning, managing inventory levels, and avoiding surplus or shortage of components.
- Production Planning and Scheduling: The BoM directly influences the planning and scheduling of the production process. By understanding the components’ lead times and availability, your CM can optimize the production timeline, aligning it with project deadlines and delivery dates.
- Cost Calculation: The BoM is central to estimating project costs. Detailing each component, their quantities, and potential suppliers allows for accurate cost calculations, facilitating budget planning and financial forecasting.
- Quality Assurance: An accurate and well-documented BoM ensures quality control by serving as a reference point during assembly, confirming that the correct components are used. It is also an essential tool for troubleshooting, offering a detailed view of the assembly at the component level.
- Communication: The BoM is a clear and concise communication tool. It allows everyone involved in the project from engineers to purchasing managers, to be on the same page regarding the components and their specifications.
A well-documented BoM is essential for future references as it maintains consistency between builds, ensuring that every produced
unit meets the same standard and quality.
Achieving the Right Dimension
Providing accurate product dimensions, including weight and size, to your box build assembly service provider is essential for several reasons:
- Production Feasibility: Your manufacturer can assess production feasibility based on accurate dimensions. Specific sizes or weights necessitate particular tools or processes, and having this information upfront allows for proper planning.
- Cost Estimation: Providing dimensions helps ensure accurate cost estimation, as size and weight influence the cost of manufacturing and packaging. Larger, heavier assemblies typically require more materials and are more expensive to produce and ship.
- Logistics and Shipping: Size and weight impact how a product is stored, handled, and transported. Precise details help optimize storage and shipping logistics, potentially saving time and money.
- Proper Integration: Providing accurate product dimensions ensures all enclosure parts fit together properly. You don’t want to discover mid-production your enclosure is too small to accommodate your PCBA, wires, and other hardware.
Testing and Inspection Techniques
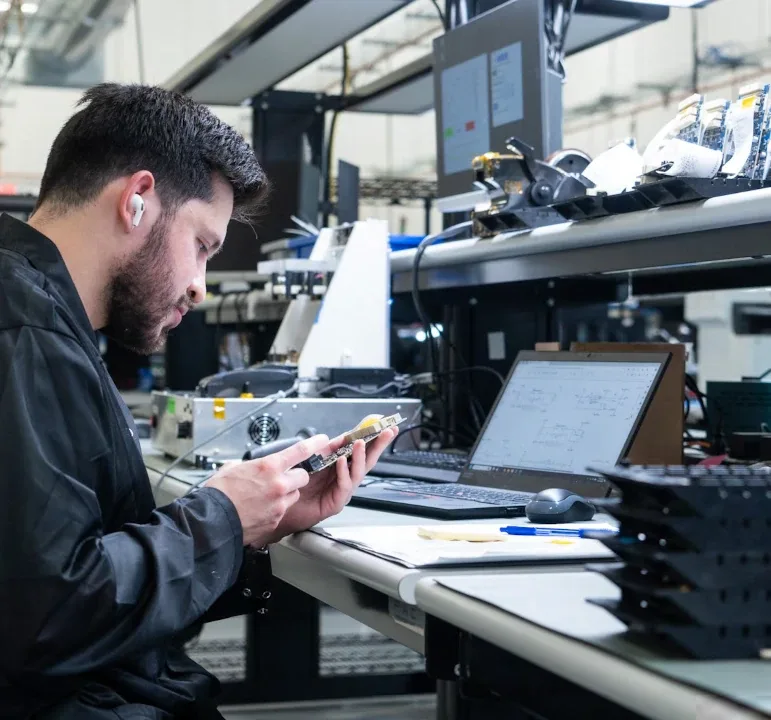
Recognizing the tests your box build assembly service provider should perform during your product assembly is crucial. First and foremost, this process assures quality. It allows for early detection and rectification of issues, saving time and resources.
Additionally, since products have unique functional needs, identifying specific tests ensures your product operates as expected. Furthermore, many industries demand regulatory compliance. You can confirm your product’s compliance through appropriate testing, avoiding potential legal ramifications.
Testing also evaluates the product’s durability, ensuring it withstands its expected lifespan, thus enhancing customer satisfaction and protecting your brand reputation.
Ultimately, specifying the right tests for your box build assembly underpins your product’s quality, functionality, compliance, reliability, and cost-effectiveness, boosting your market standing and customer satisfaction.
Having Samples and Prototypes is Essential
The purpose of samples and prototypes is to help you verify the design and functionality of the product by physically examining it, assessing its overall feel, and making any necessary adjustments before scaling up production. In particular, if your assembly drawings were in 2D, this could mitigate any fit issues (as mentioned above) since you will be able to see where parts may squeeze or crowd.
Moreover, prototypes go beyond being mere physical models; they are functional units ripe for testing and debugging. They provide the early opportunity to spot and correct faults or failures, an essential step in maintaining quality control.
Other benefits of having samples include:
- Regulatory Compliance: In some cases, regulatory bodies may require prototype testing to confirm compliance with safety and quality standards. Having prototypes ready can expedite this process.
- Cost Analysis: Prototypes can give you a good idea of the production costs you can expect for your product. They can help you identify areas where you may be able to reduce costs without compromising on quality or functionality.
- Market Testing: Prototypes can be used for early market testing. By getting your product into the hands of a small number of users, you can gather feedback that could be invaluable for refining your product and marketing approach.
Packaging, Labeling, and Shipping
Packaging, labeling, and shipping may seem like the final steps in the box-build assembly process, but their planning should commence well ahead of production.
As a result of this forward-thinking approach, you can also develop efficient packaging processes that reduce storage needs, as well as effective shipping arrangements to ensure timely delivery, which will positively impact your reputation and improve your customer satisfaction.
Moreover, labels provide crucial information, such as technical specifications, use instructions, and safety warnings. By selecting this information before production, you increase the accuracy and compliance of your labels.
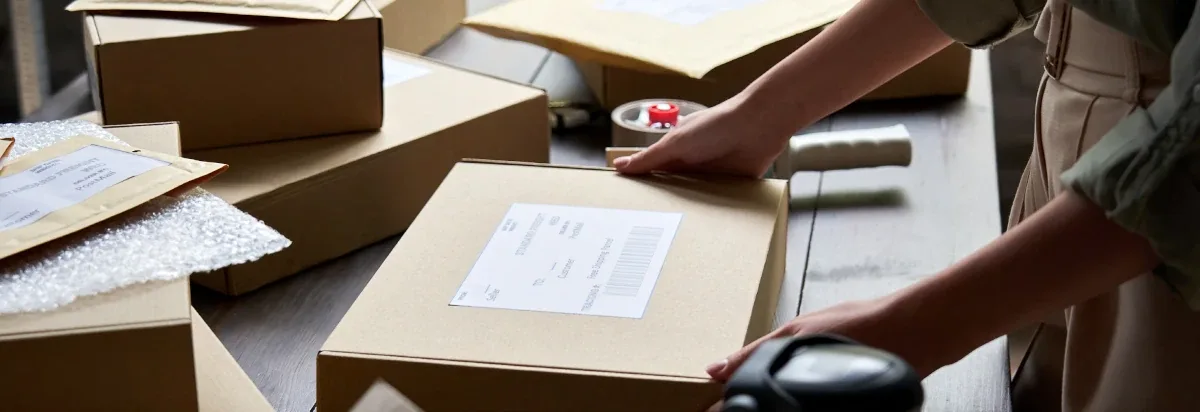
Conclusion
We’ve navigated the complex yet highly beneficial world of box-build PCBA projects. We explored the comprehensive nature of this service, the crucial role of your Bill of Materials, and the importance of meticulous planning for dimensions, testing, prototyping, and the final steps of packaging, labeling, and shipping.
Box build assembly offers an integrated, efficient, and effective manufacturing approach, which can save time, reduce costs, and simplify supply chain processes. Are you working in the hardware tech industry and looking to make your production process more efficient? Box build PCBA projects could be a worthwhile consideration.
Related Topics
Electronics in Motion: How Innovations are Redefining E-bike Experiences
This article explores how electronics and PCBAs contribute to the success of e-bikes today.
Smart Irrigation: Optimizing Water Use with PCBA-Driven Tech
With the rise of water scarcity and climate change, modern agriculture faces some concerning potential dangers. PCBAs can optimize the irrigation systems.
Drone PCBAs: Tackling Sensor Integration for Defense & Beyond
Understanding the challenges and best practices in creating sophisticated sensors for real-time data collection for different industries.
BUILD WHAT YOU WANT WITH MACROFAB
Use MacroFab for Box Build AssemblyAbout MacroFab
MacroFab offers comprehensive manufacturing solutions, from your smallest prototyping orders to your largest production needs. Our factory network locations are strategically located across North America, ensuring that we have the flexibility to provide capacity when and where you need it most.
Experience the future of EMS manufacturing with our state-of-the-art technology platform and cutting-edge digital supply chain solutions. At MacroFab, we ensure that your electronics are produced faster, more efficiently, and with fewer logistic problems than ever before.
Take advantage of AI-enabled sourcing opportunities and employ expert teams who are connected through a user-friendly technology platform. Discover how streamlined electronics manufacturing can benefit your business by contacting us today.