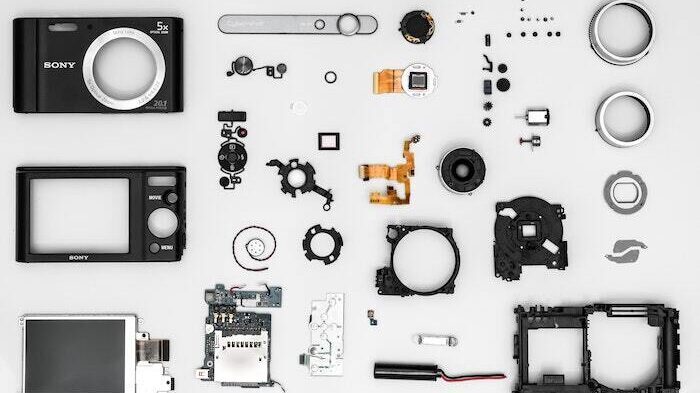
MacroFab Blog
Prototyping for product development demands creativity, knowledge sharing, and staying up to date with the latest technology. However, with all businesses, there are typically strict deadlines that require engineers to take short-cuts, which could cost the business time and resources later in development. Here are some guidelines to help you be as proactive as possible during this process.
Knowing when to switch from breadboarding to a custom PCB
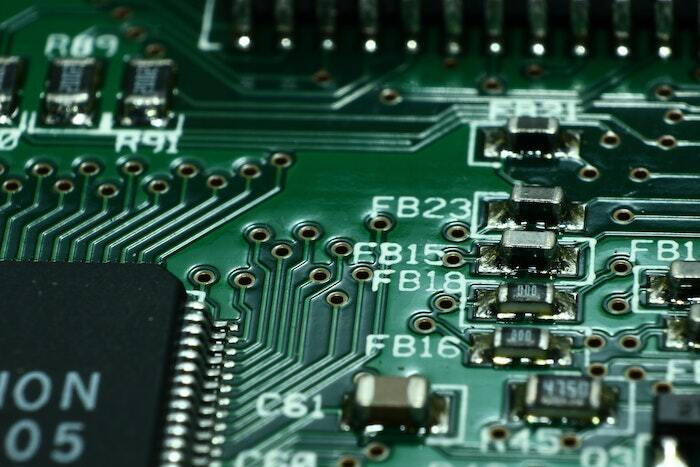
A valuable engineer is able to generate concepts and prototypes quickly to show proof of concept and feasibility of a new idea. As a result, many manufacturers offer development boards for almost any type of component, sensor, or peripheral that is available. A few development boards, a breadboard, a benchtop power supply, and some wiring is sometimes all that is required to prove out simple concepts. However, there are limitations to what can be accomplished with off-the-shelf parts and the transition to a custom PCB becomes necessary.
In some cases, using off-the-shelf boards is all that is needed to prove out a concept and a team can go confidently into development which will include designing a custom PCB. These typically include simple low voltage, digital circuits. However, in more complex situations, off-the-shelf boards are incapable of proving a concept, and further feasibility work is required prior to entering development with accurate timeline estimates. These situations include RF-based applications where PCB trace impedances and parallel capacitances need to be fully analyzed. Additionally, other factors that increase circuit complexity drive the need for custom PCBs, such as multiple sensors and peripherals, requiring more than a couple voltage rails, and high power applications that require analysis of heat distribution and power efficiency.
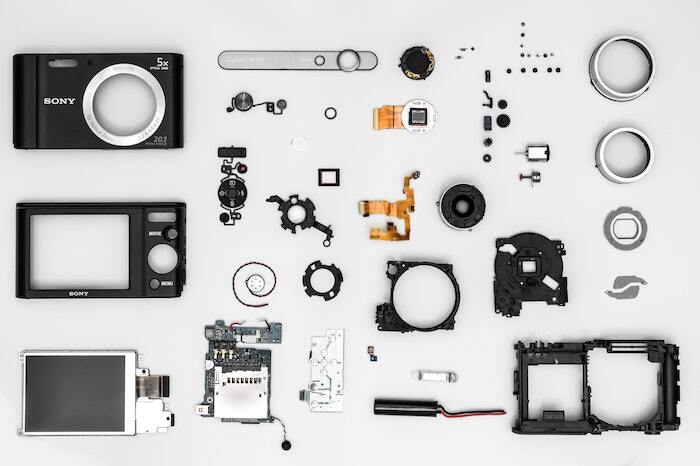
Lastly, the circuit itself may have little to do with the need to design a custom PCB. To really understand if a product concept provides value to the customer, a prototype representing the final design needs to be analyzed. Good human factors and ergonomic design will require engineers to design custom shaped PCBs to fit into prototypes that will be tested by users and potential customers. In this way, the prototype as a whole can be analyzed, iterated, and improved.
Beware of the Easy-Way-Out in PCB Design
When ready to move into schematic capture and layout, be cautious of the decisions made. These decisions have a high probability of making their way into production even if doing so was not the intention.
Deadlines, resource constraints, and budget limitations will commonly be the reason why specific aspects of a product will be deemed acceptable and not revised.
When changes need to be made after a product has transitioned to the manufacturing design phase, board level changes can become problematic. Changing the schematic or layout may require testing to be redone which can waterfall into having to rewrite test protocols and obtain re-approvals. This could easily add weeks to the development timeline. Having a component become obsolete early in the production phase can lead to a shortage of stock on the shelf, limiting profits for the company. In addition to development hurdles, changing the PCB design later than anticipated can cause designs to fall out of compliance.
Making proactive design choices can be paramount in launching products on time.
The table below outlines just a few shortcuts to avoid and why they may be detrimental to a project.
Copying and pasting schematics/layouts from legacy products
You run the risk of obsolete parts in older designs, and those files may not utilize the latest technology in PCB manufacturing that could enable the design to be more space efficient. Additionally, other issues may arise such as net name inconsistencies and outdated footprints.
Using components readily available in the lab (op-amps, transformer cores, MOSFETs, etc.)
Components laying around in the lab should be avoided unless they have been properly stored and they are accurately labeled. IC’s can be faulty without showing any signs of damage leading to a week’s worth of debugging.
Selecting niche components
Sometimes niche components cannot be avoided, but ensure your requirements are accurate and your design does not get cornered. For example, a 155ohm resistor may be exactly what is needed for a filter, but changing other components may allow for 150ohms and a multitude of backup options should the part go obsolete.
When Prototyping, Develop Good Habits for Product Development
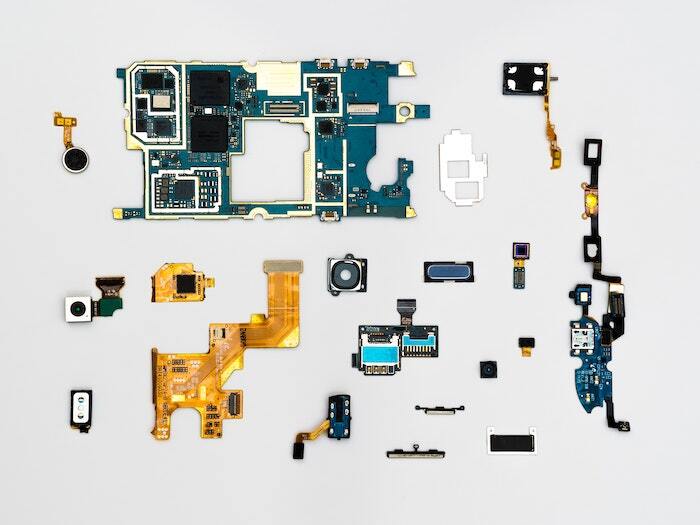
When designing a PCB, anticipating where the prototype will be two iterations from now will pay off in the end and can save unneeded frustration. It is understandable that not all product specifications and inputs may be readily available early in development. Therefore, design for a broad range of potential inputs. If it is a battery power application, be prepared for the chance that it could require more power than originally anticipated. If 20W of power is needed for the initial concept, the next iteration may require 30W. Designing for and incorporating a higher capacity battery may end up saving a design revision and a few weeks of turnaround time.
One of the best habits an engineer can develop is documentation. It is likely that a design will go through multiple iterations both formally and informally. Early on in the process, document the circuit, its purpose, how it works, and its expected behavior. When the first boards arrive, it will go through component changes, cut traces, and air wiring until it functions as intended and unless each step is documented along the way, replicating those changes in the next revision will be difficult and prone to mistakes.
Another good habit that will save time is to always order extra prototype boards. Permanently damaging a board can come unexpectedly and at inopportune times. The benchtop supply was set too high or a component was shorted while being probed causing a pad to be burned are just a couple of examples. Having extra boards on hand will prevent having to wait to continue testing.
Lastly, and maybe most importantly, is to work with supply chain and manufacturing early on in the process. They will help to identify high-risk components that may need to be substituted and areas of the board that are hard to assemble. Additionally, the supply chain will aid in identifying parts and components that can be sourced from approved vendors. Some contract manufacturers have their own supply chain departments, so they can harness their relationship with vendors and can help identify discounted rates for parts and aid in sourcing alternatives for out of stock and end of life components.
It is important to remember that, more often than not, the first PCB for a new concept will likely not be the final one. Be prepared to make iterations, keep track of changes, and work cross-functionally early on to avoid delays during development.
When you’re ready to prototype your PCB, using a CM with online capabilities will help you keep your files better organized, rather than emailing different versions of your designs and keeping track in you inbox.
Related Topics
How MacroFab Listens and Delivers
We’ve revolutionized the traditional PCB manufacturing process, offering a online platform supported by a network of high-quality North American factories.
Creating an Accelerated PCBA Lifecycle: From NPI to Production
Foster open communication to better embrace flexible BoM management and drive efficiency, quality, and innovation.
Struggling with Inflexible PCBA Manufacturing? MacroFab's Got Your Back.
Many electronics designers struggle with systems that demand complete data and specific formats upfront. Wouldn't it be great if there was a better way?
Turnkey PCBA Prototyping
Rev up your design game, iterate faster, and build better products within one comprehensive technology platform.
About MacroFab
MacroFab offers comprehensive manufacturing solutions, from your smallest prototyping orders to your largest production needs. Our factory network locations are strategically located across North America, ensuring that we have the flexibility to provide capacity when and where you need it most.
Experience the future of EMS manufacturing with our state-of-the-art technology platform and cutting-edge digital supply chain solutions. At MacroFab, we ensure that your electronics are produced faster, more efficiently, and with fewer logistic problems than ever before.
Take advantage of AI-enabled sourcing opportunities and employ expert teams who are connected through a user-friendly technology platform. Discover how streamlined electronics manufacturing can benefit your business by contacting us today.