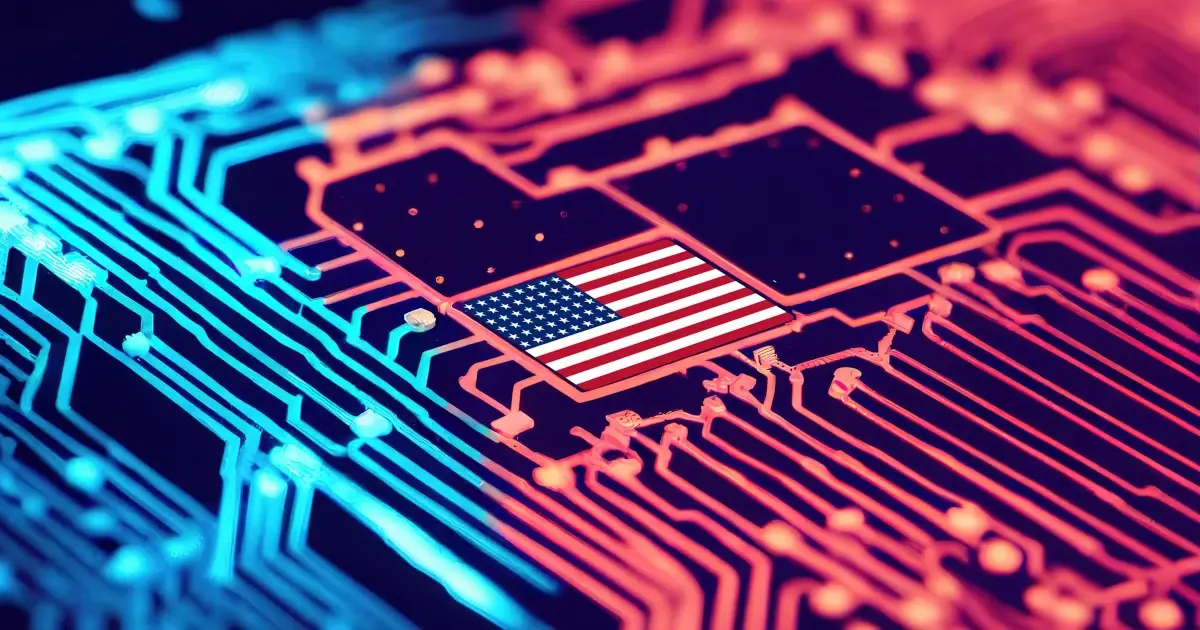
MacroFab Blog
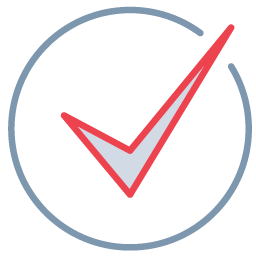
Checkpoint
Increasingly, domestic manufacturers are being tapped to help companies find the ‘sweet spot’ for profitability as the design cycle shortens.
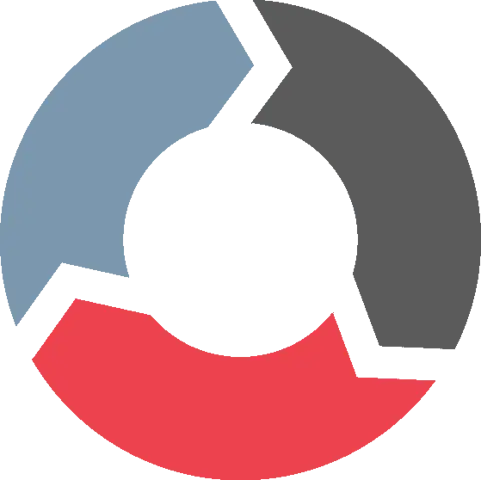
PCBA production is returning back to the United States after decades abroad. The business case for offshoring electronics manufacturing is no longer as compelling as it once was. However, it’s not just that business conditions overseas have worsened. “Made in America” PCB manufacturing now offers many advantages.
Companies that are looking to increase the agility, productivity, and resilience of their electronics supply chains can do so in partnership with local and regional vendors. The key is understanding what problems reshoring solves and knowing how to do it effectively.
In this post, we’ll define reshoring and give a brief overview of why it’s happening here and now. As the electronics PCBA manufacturing industry continues to evolve, reshoring will be crucial for many organizations.
What is Reshoring?
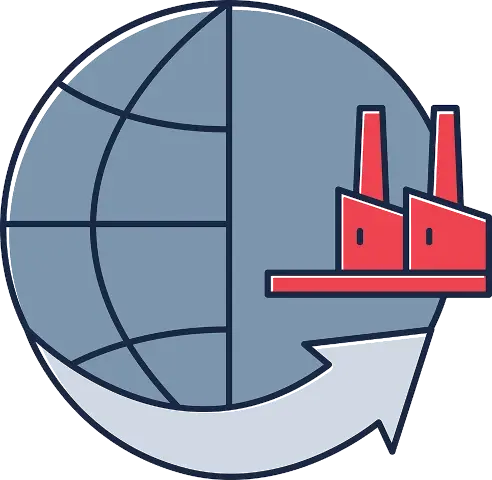
Reshoring refers to the act of bringing activities back to the U.S. that were previously offshored. These activities include manufacturing, service, and IT processes or capabilities. While reshoring has received more attention over the last few years, there is still ample opportunity for U.S. firms to bring back overseas production.
Reshoring is an attractive path for modern-day electronics developers. It reduces supply chain complexity and catalyzes local economic growth. It also makes developing complex electronic products easier.
Companies today need reliable manufacturing skills and capacity that can adapt to disruption in the marketplace. Reshoring offers these benefits and more.
Why Manufacturing Left America
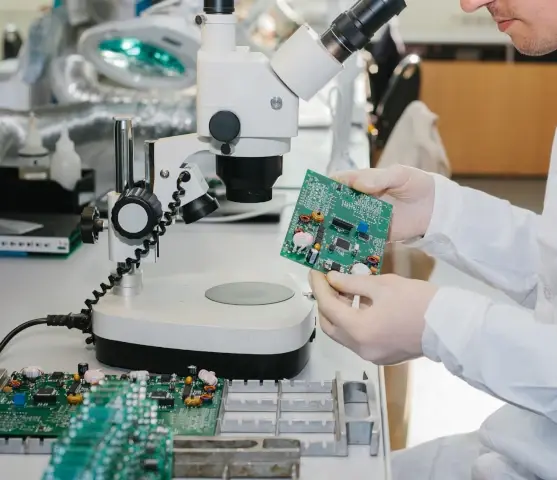
Beginning around the 1960s, U.S. companies in the semiconductor industry began offshoring labor-intensive manufacturing work. They moved basic assembly overseas, primarily to Asia, in hopes of increasing access to foreign markets and reducing labor costs.
Over the 1970s and 1980s, electronic manufacturing moved overseas, resulting in rapid improvements in production skills in foreign markets. Consequently, U.S. companies were able to outsource more complex elements of the PCB assembly production process to foreign contract manufacturers.
Following the North American Free Trade Agreement (NAFTA), some manufacturing jobs returned to Canada and Mexico. The U.S., Canada, and Mexico eliminated barriers to trade and tariffs, increasing the flow of economic activity across the continent. This included the establishment of many new manufacturing facilities, particularly along the U.S. – Mexico border.
U.S. companies started designing and sending components to Mexico’s factories for low-cost assembly. This created employment opportunities for Mexico’s budding manufacturing industry. Through NAFTA, North American companies got a taste of what it was like to have quality, cost- effective manufacturing that didn’t require moving products across vast oceans.
But in the early 2000s, offshoring picked up again after China entered the World Trade Organization (WTO). China’s participation dissolved key trade barriers, motivating U.S. companies to double down on offshoring to Asia. This trend continued when the U.S. opened up the floodgates for certain products manufactured in China by removing quota restrictions.
Why Manufacturing is Coming Back
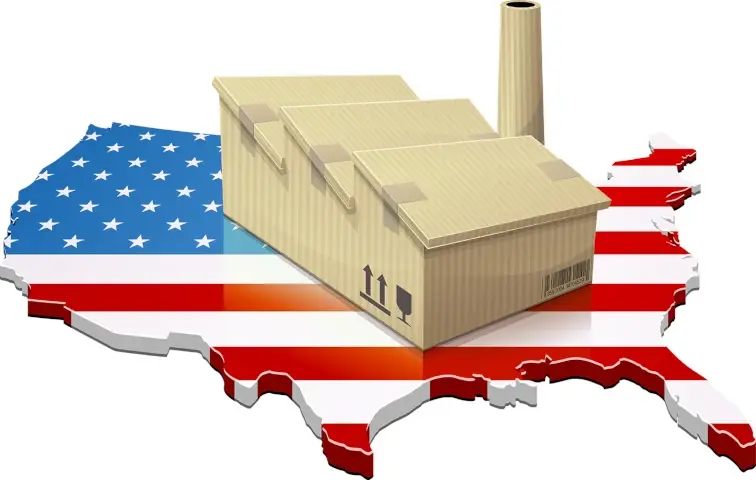
After decades of offshoring, manufacturing is returning to U.S. soil for several reasons. First, organizations have discovered that there are hidden costs to offshoring. Although skilled labor tends to be less expensive in countries like China and India, quality control issues and the lack of stringent IP protections can eat into margins and can negatively impact a company’s reputation. Energy, transportation, and labor costs have also increased, weakening the business case for offshoring.
Automation-heavy domestic manufacturing also promises lower overall costs, faster innovation speeds, and repeatable outcomes that improve quality. Increasingly, domestic manufacturers are being tapped to help companies find the ‘sweet spot’ for profitability as the design cycle shortens.
Moreover, COVID-19 revealed the fragility of our reliance on offshore manufacturing networks. The pandemic caused enormous, long-lasting disruption that has convinced even more electronics manufacturing leaders to reshore. Now, we’re seeing deeper investment in domestic electronics manufacturing infrastructure by corporations and government entities alike. Both are helping bring more aspects of the PCBA production process back home.
Reshoring is Essential for Future PCBA Production
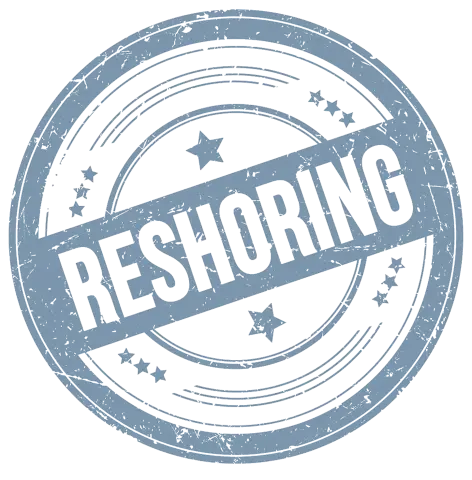
For good reason, reshoring is top of mind for U.S.-based electronics developers. It isn’t simply a buzzword or trendy new production framework. Reshoring PCBA production addresses major challenges that have cropped up over the past 50+ years.
As a technology platform that partners with factory lines all across North America, MacroFab has helped many businesses reshore overseas operations. We’ve already done the hard work of identifying high-quality facilities and assessing their capabilities. Electronics teams only have to plug into our network to get started.
Related Topics
Mapping Out a PCBA Supply Chain Strategy in Five Moves
Companies should create unique vendor relationships with numerous international suppliers due to the necessity of having to source components globally.
MacroFab’s Modern Approach to Strategic Sourcing
Many Contract Manufacturers (CMs) and Original Equipment Manufacturers (OEMs) have some sort of procurement team. So what makes MacroFab so different?
Electronics Production: Upgrading Inventory Systems with Modern Tech
Inventory and supply chain management software and processes play a pivotal role in safety, efficiency, & security of electronics manufacturing operations.
Find out more about reshoring with MacroFab
Reshoring with MacroFabAbout MacroFab
MacroFab offers comprehensive manufacturing solutions, from your smallest prototyping orders to your largest production needs. Our factory network locations are strategically located across North America, ensuring that we have the flexibility to provide capacity when and where you need it most.
Experience the future of EMS manufacturing with our state-of-the-art technology platform and cutting-edge digital supply chain solutions. At MacroFab, we ensure that your electronics are produced faster, more efficiently, and with fewer logistic problems than ever before.
Take advantage of AI-enabled sourcing opportunities and employ expert teams who are connected through a user-friendly technology platform. Discover how streamlined electronics manufacturing can benefit your business by contacting us today.