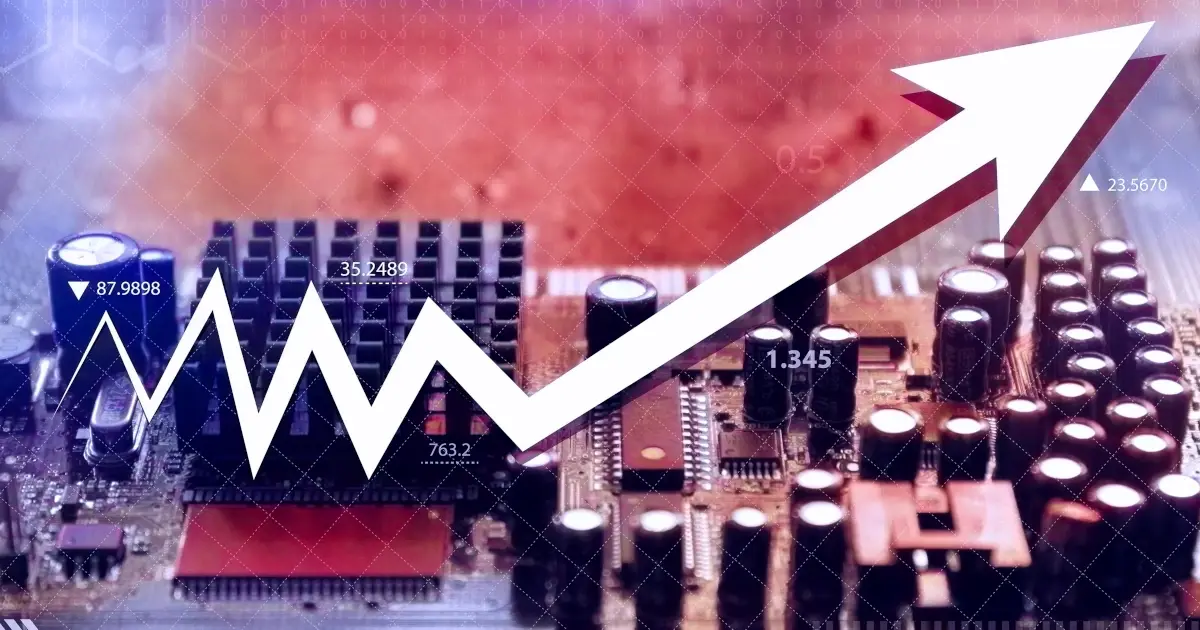
MacroFab Blog
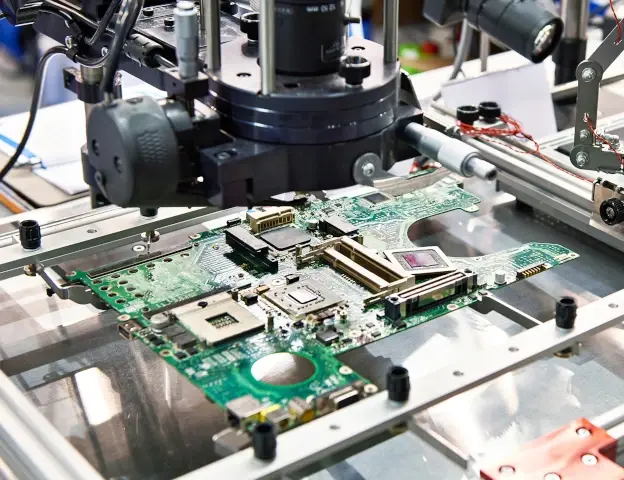
As an electronics project professional in the competitive electronics industry, it’s crucial for you to understand and manage the factors that influence project manufacturing costs. By doing so, you’ll be better equipped to maintain profitability and meet customer expectations. One essential question to consider is: What factors should you be concerned about when assessing manufacturing costs for your electronics projects?
In this comprehensive article, we’ll explore the factors contributing to the recent uptick in electronics costs, which has been observed across the industry. We’ll examine the underlying reasons behind this surge in prices and provide practical strategies to help you navigate these challenges effectively.
By understanding the driving forces behind the increasing expenses related to electronics, you’ll be better prepared to adapt to the evolving market conditions and remain competitive.
Key Takeaways
• Rising raw material prices, such as copper, gold, and silver, have a direct effect on electronics manufacturing costs.
• Recent global events, such as the Ukraine-Russia conflict, COVID-19, and inflation, have significantly impacted the electronics industry.
• Changes in regulations and environmental standards can also lead to increased manufacturing costs.
Rising Raw Material Prices
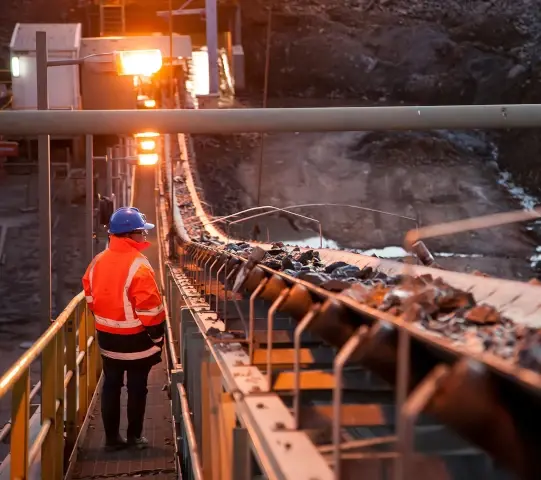
Fluctuating raw material prices, such as copper, gold, and silver, have a direct effect on electronics manufacturing costs. For example, in February, copper prices experienced a 15 percent surge due to supply constraints and increased demand.
To mitigate risks associated with such price fluctuations, it’s essential that you monitor global market trends and economic conditions. One way to counteract these risks is by securing long-term contracts with suppliers, which can help lock in prices.
Recent global events, such as the Ukraine-Russia conflict, the lingering effects of COVID-19, and inflation, have significantly impacted the electronics industry. A report by IPC highlights the following concerns:
- 86 percent of electronics businesses are concerned about inflation.
- In addition, 9 out of 10 companies are already experiencing rising material costs, including copper, gold, and silver.
A robust supply chain is vital in minimizing cost increases in electronics manufacturing. If you work with a CM with a wide sourcing network, you can reduce the chance of unexpected price increases.
CM partners should also be able to accept materials from whichever source is most appropriate, whether it is directly from you or through strategic sourcing. Economic and market trends monitoring remains crucial to maintaining a healthy supply chain while reducing risks associated with price fluctuations.
Labor Costs
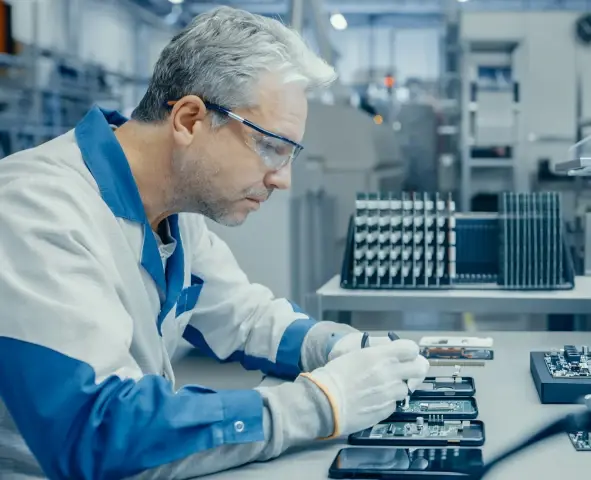
Labor costs significantly affect the overall expense of manufacturing electronic products. Factors such as skilled labor shortages, regional differences in labor costs, and design choices contribute to these costs.
For instance, in the United States, the average hourly wage for electronics assemblers rose by 3.2 percent in February compared to the previous year and rose further in March and April This increase in labor costs can directly affect the final product prices.
Nonetheless, wages may vary by region. Working with a manufacturing partner with geographically dispersed domestic manufacturing facilities can protect you from this problem.
One design choice that can influence cost is using through-hole components, which have higher associated labor costs than Surface Mount Technology (SMT). As product owner, you should collaborate with your engineering team to make cost-effective design decisions during product development based on expected labor costs.
Regulatory Compliance and Environmental Standards

Changes in regulations and environmental standards can also lead to increased manufacturing costs. Key legislation affecting the electronics industry includes RoHS, WEEE, and REACH. Non-compliance with these regulations can result in fines, penalties, and even product recalls, which can have severe financial consequences for your company.
According to a study by the European Commission, non-compliance with RoHS alone can cost businesses up to $10 billion annually.
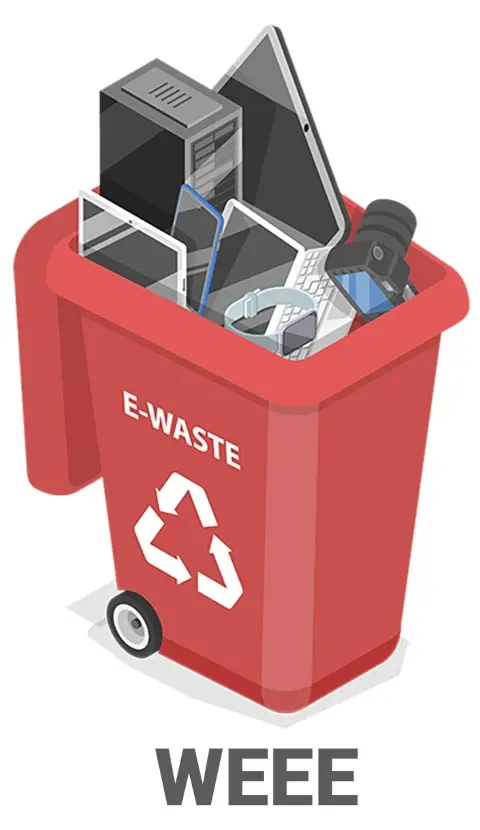
It is true that compliance with RoHS, WEEE, and REACH can increase per-unit manufacturing costs, but taking a proactive stance to ensure compliance can prevent fines and penalties, which is ultimately a sound financial decision.
Further, as sustainability becomes a priority, industry experts project that within a decade, up to 20 percent of PCBAs could be manufactured using more environmentally-friendly methods, such as dry etching, printing, and low-temperature solder component attachment. Despite being more expensive than traditional methods, such methods offer long-term savings through reduced waste disposal costs and lower energy consumption. Additionally, this choice is in line with corporate social responsibility and can open up new markets for business.
Consider implementing sustainable manufacturing practices and staying up-to-date on regulatory changes to minimize costs and reduce environmental impact. By doing so, you’ll not only maintain compliance but also enhance your company’s reputation and competitiveness.
Supply Chain Disruptions
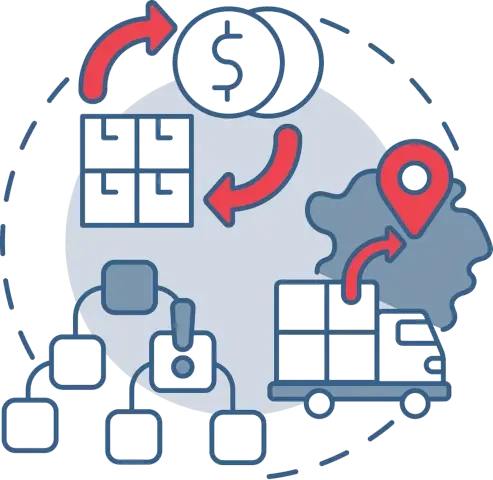
The electronics manufacturing industry faces significant cost impacts due to supply chain disruptions caused by factors like natural disasters, geopolitical tensions, and global health crises. The COVID-19 pandemic and “Zero COVID” policies serve as prime examples of such disruptions, prompting companies to reevaluate their supply chain strategies.
One strategic response to these challenges is reshoring, the process of relocating manufacturing operations away from the APAC region. Reshoring bolsters supply chain resilience and offers key advantages, including enhanced quality control, decreased shipping expenses, and increased agility in responding to market changes.
However, despite the benefits of reshoring, the industry grapples with component shortages, driven by heightened demand and constrained production capacity. Ensure that your manufacturing partner can provide you with multiple sourcing options for components, as well as ample factory capacity for future production.
Adopting proactive supply chain management practices, such as reshoring and contingency planning, is crucial for mitigating risk, achieving cost optimization, and preserving a competitive edge in the ever-changing electronics landscape.
Intellectual Property (IP) Protection
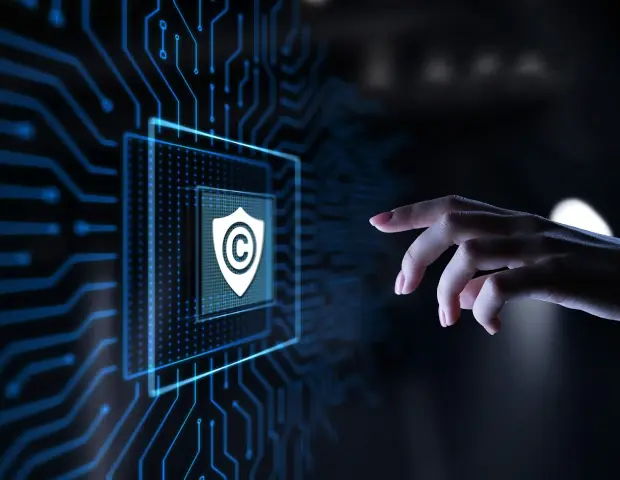
Inadequate IP protection can lead to increased manufacturing costs due to the risks of IP theft and counterfeiting. A study by the International Chamber of Commerce (ICC) estimates that the global economic value of counterfeiting and piracy could reach $4.2 trillion by 2022, potentially costing 5.4 million jobs worldwide.
IP protection is a cornerstone of success for any tech-related company. In an industry where innovative designs and proprietary technologies serve as crucial differentiators, safeguarding IP assets is vital for maintaining a competitive advantage and ensuring the long-term viability of your company.
To enhance IP protection, you and your manufacturing partners can adopt the following strategies:
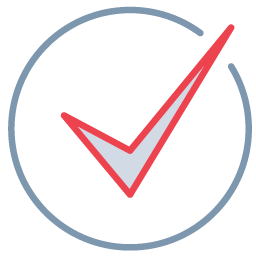
Checkpoint
By 2022, counterfeiting and piracy could cost the world $4.2 trillion and 5.4 million jobs.
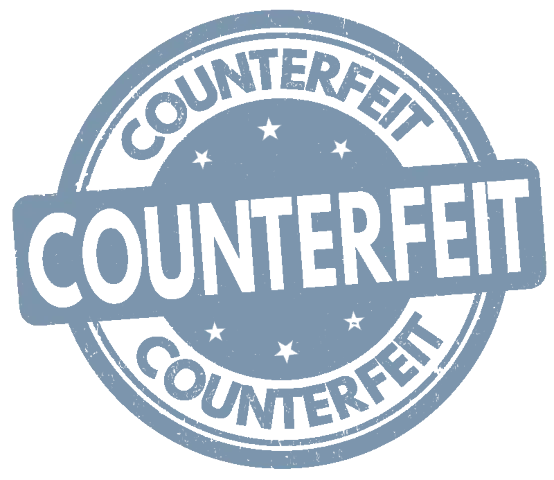
- Partner with Reputable Manufacturers: Work with trustworthy contract manufacturers that adhere to industry best practices.
- Utilize Non-Disclosure Agreements (NDAs): Implement NDAs with employees, contractors, and business partners to prevent unauthorized disclosure of sensitive information.
- Implement Secure Data Management: Use secure data management systems with robust cybersecurity measures to control access to IP assets.
- Register IP Rights: Register patents, trademarks, and copyrights to provide legal protection and assert ownership of IP assets.
- Conduct IP Audits: Perform regular IP audits to assess IP assets, evaluate risks, and ensure compliance with regulations.
Proactive IP brand protection is essential for maintaining competitiveness and driving innovation in the industry.
Conclusion
The recent spike in electronics costs stemmed from various factors, including rising raw material prices, labor costs, regulatory compliance, supply chain disruptions, and IP protection challenges. It’s crucial for you to actively address these factors to maintain cost efficiency and competitiveness in the market.
You can strike a balance between cost-efficiency and performance by implementing strategies such as securing long-term contracts with suppliers, investing in workforce training, maintaining regulatory compliance, diversifying suppliers, and protecting your intellectual property. Doing so will ultimately drive profitability and sustainable growth in the competitive electronics market.
Partnering with a reliable and experienced contract manufacturer is vital to successfully navigating these challenges. By leveraging their expertise and resources, product owners can better manage the complex factors that influence electronics manufacturing costs and ensure the delivery of high-quality products that meet customer expectations.
In conclusion, staying informed and proactive in your approach will help you overcome the challenges presented by cost fluctuations and maintain a strong position in the electronics manufacturing industry.
Related Topics
Mapping Out a PCBA Supply Chain Strategy in Five Moves
Companies should create unique vendor relationships with numerous international suppliers due to the necessity of having to source components globally.
MacroFab’s Modern Approach to Strategic Sourcing
Many Contract Manufacturers (CMs) and Original Equipment Manufacturers (OEMs) have some sort of procurement team. So what makes MacroFab so different?
Electronics Production: Upgrading Inventory Systems with Modern Tech
Inventory and supply chain management software and processes play a pivotal role in safety, efficiency, & security of electronics manufacturing operations.
See How MacroFab Can Help
Schedule Time With a SpecialistAbout MacroFab
MacroFab offers comprehensive manufacturing solutions, from your smallest prototyping orders to your largest production needs. Our factory network locations are strategically located across North America, ensuring that we have the flexibility to provide capacity when and where you need it most.
Experience the future of EMS manufacturing with our state-of-the-art technology platform and cutting-edge digital supply chain solutions. At MacroFab, we ensure that your electronics are produced faster, more efficiently, and with fewer logistic problems than ever before.
Take advantage of AI-enabled sourcing opportunities and employ expert teams who are connected through a user-friendly technology platform. Discover how streamlined electronics manufacturing can benefit your business by contacting us today.