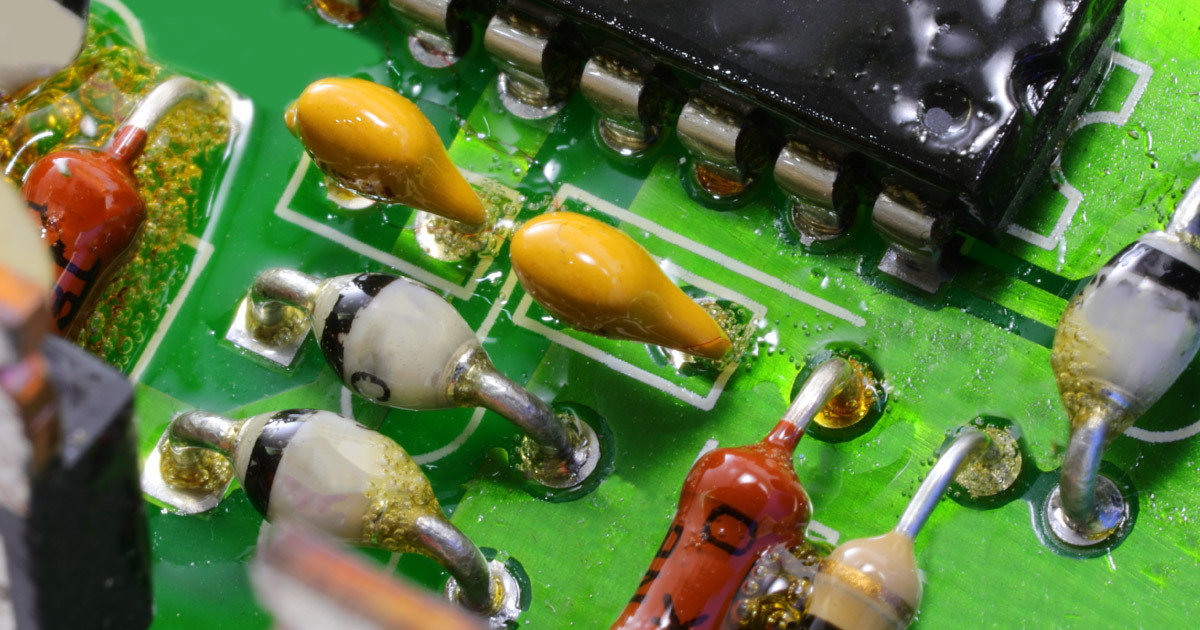
MacroFab Blog
Here is a quick overview of encapsulation vs. conformal coating, as well as their best uses.
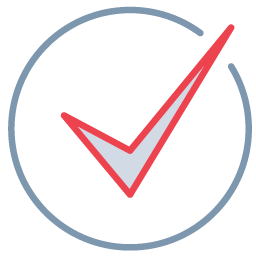
Checkpoint
Conformal coating protects from damage caused by fungus, moisture, salt spray, or corrosion.

PCBA manufacturing increasingly requires conformal coating and potting/encapsulation to provide advanced protection methods. The world’s technological advancements enable PCB assemblies to find their way into an expanding number of products in many industries. Occasionally, these products need extra protection to shield them from external contamination while preserving their original design and functionality.
Designers can achieve this result with conformal coatings or potting and encapsulation resins. Aside from providing chemical and thermal resistance to boards, both organic polymer substances also deliver electrical insulation. In spite of this, they differ significantly and shouldn’t be confused with each other. Here is a quick overview of conformal coating vs. potting vs. encapsulation, as well as their best uses.
What is Conformal Coating?
A conformal coating serves as a robust and protective shield for printed circuit board assemblies (PCBAs) and enhances their durability and longevity in challenging environments. As a polymerizing film, conformal coating adapts to the contours of the components it covers, thus having a 'conformal' nature.
Composed of various materials including acrylics, silicones, polyurethanes, and epoxy, this thin, lightweight layer delivers a non-conductive dielectric defense against moisture, dust, salt spray, and other corrosive elements. It may be applied by brushing or spraying.
By adding this additional protection, conformal coatings significantly improve the reliability and operational lifespan of electronic devices, reinforcing their functionality in the face of harsh or challenging conditions.
Conformal Coating vs. Potting vs. Encapsulation – What’s the Difference?
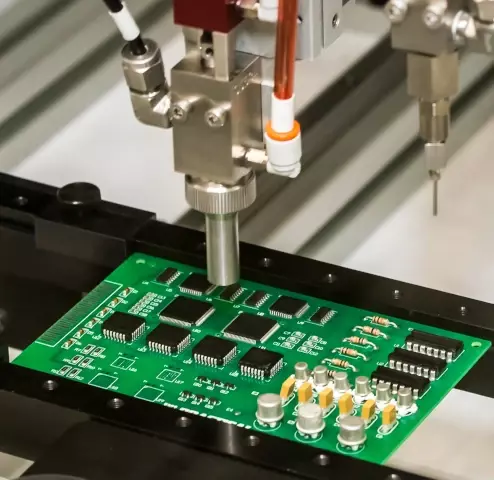
Conformal coating and potting or encapsulation of PCBAs provide different levels of protection.
Encapsulation uses a thick resin to contain electronic components. Resin provides protection from physical shock and chemical exposure. This step involves mixing the resin with a hardener before applying it to the board. When the crosslinked polymer dries, it obscures the component underneath.
PCB potting is sometimes confused with encapsulation, but the two processes are actually different. During potting, a case or shell is created, and resin is poured over it to completely encase the component. The resin-filled pot becomes part of the final product. Often, potting protects sensitive components against moisture and water damage. Furthermore, it can act as a visual and physical barrier that prevents IP theft and tampering.
To avoid moisture contamination, PCB potting should be adequately degassed before filling or pouring. Air bubbles trapped within the coating can cause a moisture problem if the encapsulant is improperly stored or applied.
Choosing the Right Protection Method for Optimal Performance
Conformal coating and potting/encapsulation are two primary techniques that offer environmental protection for PCBAs, but they differ significantly in their level of coverage and ideal applications. Understanding these differences is crucial for optimizing PCBA performance, longevity, and overall product functionality. Consider the environmental factors that will affect your assembly, such as:
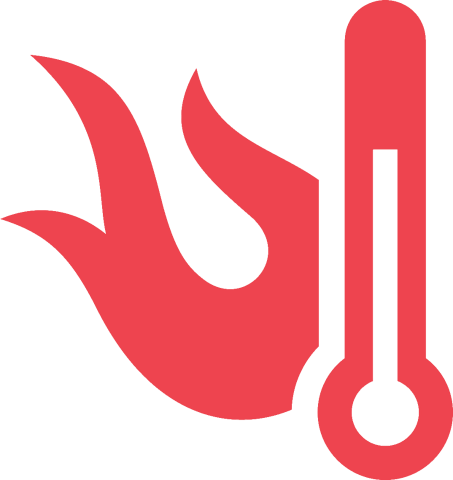
- Chemical exposure: Coatings and resin both provide excellent protection from chemical exposure.
- Mechanical stress: Resin provides a thick layer of protection against physical damage in environments where components may be abraded or scratched.
- Moisture from water, humidity, etc: Conformal coating is a cost-effective method of preventing water infiltration. Water resistance varies from coating to coating.
- Physical shock: Resin spreads the impact over the entire material, reducing or eliminating damage to underlying parts.
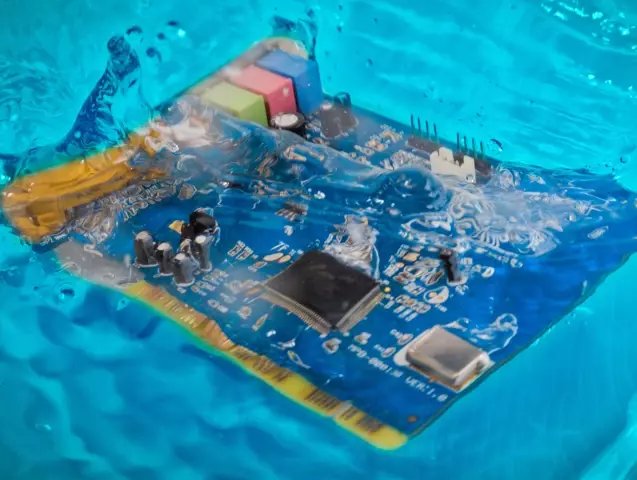
- Temperature extremes: Extreme temperatures require additional consideration, especially when selecting resins. A special type of epoxy compound designed for aggressive environments exists.
Selecting the optimal protection method hinges on the specific environmental conditions your PCBA will encounter during operation. Here's a breakdown of typical use cases for each technique:
Conformal Coating: Ideal for moderately harsh environments where PCBAs require protection from moisture, dust, or corrosion. Common applications include consumer electronics, medical devices, and automotive components. Conformal coatings offer several advantages, including:
- Reduced weight: The thin layer adds minimal weight to the PCBA, making it suitable for weight-sensitive applications.
- Easier rework: Repairs or component replacements are simpler due to the non-permanent nature of the coating.
- Wide range of material options: Acrylic, silicone, and polyurethane coatings offer various properties to suit specific needs (e.g., flexibility, chemical resistance).
Potting/Encapsulation: Best suited for critical PCBAs operating in harsh environments that demand high levels of protection. Applications include industrial controls, outdoor equipment, and aerospace components. Here's why potting might be the right choice:
- Superior physical protection: The thick resin layer safeguards components from physical impact, shock, and vibration.
- Complete waterproofing: Potting creates a sealed enclosure, offering the highest level of moisture resistance.
How to Apply a Conformal Coating
It is possible to apply conformal coatings in several different ways. This is determined by production yield and includes
- Dip Coating: In dip coating, the PCB or components get immersed in the coating solution. It allows for a full application, but issues may arise during drying.
- Brush Coating: Wet coating gets applied piece by piece with a brush. When misapplied, brush coating can lead to unsatisfactory performance results.
- Spray Coating: Spray coatings can be applied manually or by machines. In addition to its extreme accuracy, automatic spraying facilitates high-volume production due to its highly repetitive nature.
Final Considerations
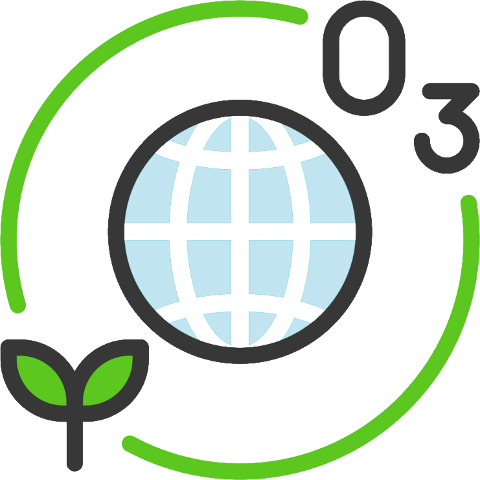
Consider your vendor’s capabilities, your product needs, and any regulatory requirements that may apply to your project before deciding whether to coat or encapsulate. The Montreal Protocol restricts some chemicals once used in conformal coating formulations as ozone-depleting chemicals, so make sure your CM understands these limitations (especially if they are located in a country with fewer environmental restrictions.)
Among the conformal coating types and methods offered by MacroFab are acrylic, silicone, and polyurethane. As per industry standards, we conduct quality control under UV light and add a UV tracer to our conformal coatings.
Related Topics
How Can a Box Build Benefit Your PCBA Design?
PCBA box build is a sophisticated process involving the design, production, and construction of an electromechanical system that goes beyond a PCBA.
Insider's Guide to Navigating Box Build PCBA Projects
This guide will help you become familiar with box build assembly, decide if it’s right for your PCBA project.
Overview of PCBA Manufacturing Processes and Technologies
We’ll provide you with an introduction to each step and explain its significance in the larger PCB manufacturing and assembly process.
About MacroFab
MacroFab offers comprehensive manufacturing solutions, from your smallest prototyping orders to your largest production needs. Our factory network locations are strategically located across North America, ensuring that we have the flexibility to provide capacity when and where you need it most.
Experience the future of EMS manufacturing with our state-of-the-art technology platform and cutting-edge digital supply chain solutions. At MacroFab, we ensure that your electronics are produced faster, more efficiently, and with fewer logistic problems than ever before.
Take advantage of AI-enabled sourcing opportunities and employ expert teams who are connected through a user-friendly technology platform. Discover how streamlined electronics manufacturing can benefit your business by contacting us today.