The first step in validating a new electronic design is creating a functional PCB prototype assembly. Prototyping serves as a proof of concept, demonstrating design feasibility and identifying potential issues before production. In complex projects, PCB prototyping establishes design feasibility and future manufacturability. This process takes ideas from paper through the design stage to a functional demonstration.
However, prototyping can become inefficient if basic rules are ignored, wasting time and leading to unnecessary costs. Prototyping often happens in small-volume runs, but too many one-off builds introduce inefficiencies that can delay your project. Luckily, adopting these tried and true strategies can help you lower costs and effort while saving time on your next PCBA prototype.
Choose a Contract Manufacturer (CM) for the Entire Project
When sourcing a CM to handle your prototypes, it may seem practical to select a supplier specializing in small-batch runs. However, this approach can cause future delays when you need to roll prototype development into final manufacturing; your new production-level manufacturing partner has no history with your job and begins the manufacturing process with zero knowledge. Building knowledge must begin all over again. This takes time and effort.
Partnering with a CM that offers both PCB prototype services and volume manufacturing capabilities can lower costs and speed your development. Platforms like MacroFab--with their connected technology platform and digital North American factory network(with options to prototype in the USA)--centralize project data, allowing insights gained during prototyping to carry over into production. This enables a seamless transition from prototyping to production by leveraging shared learnings from the prototype stage forward.
Communicate Proactively with Your CM
Effective communication with your CM will be key for a successful prototype. Engaging your CM early allows you to discuss design challenges, such as material choices, stack-ups, and clearance issues, and resolve them before they become obstacles.
Your CM can also help you determine when and where simpler or less expensive processes or materials, like PCB component alternatives, will suffice without compromising design integrity. This is an important step to cut costs, especially as prototypes move into larger production runs.
Additionally, good communication now can identify any possible design omissions or challenges. For example, a small, congested board creates assembly challenges (and associated costs) that can be reduced with some simplification. Addressing these factors early during lower quantity runs can facilitate a smoother manufacturing process later.
Prioritize Component Selection
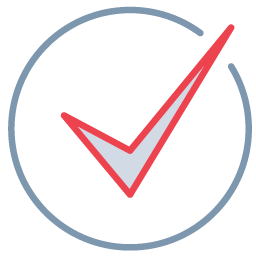
Checkpoint
The availability of your entire BOM is critical to prevent unwanted prototyping delays.
Component availability is a leading cause of prototyping delays. Including secondary or alternative components in your BOM gives your CM flexibility to procure parts without delaying your PCB assembly process when primary components are unavailable or back-ordered. MacroFab's technology platform can automatically suggest engineer-approved form-fit-function alternatives with a single click.
Additionally, consider the long-term implications of your component choices. Using rare or hard-to-source components might not only slow down prototyping but also increase production costs. Planning ahead for scalability and production simplifies the transition from prototyping to manufacturing.
Leverage a DFM Plan for Success
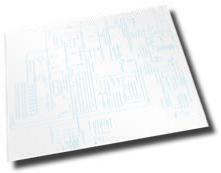
A design for manufacturing (DFM) plan is the guide for bringing a new product to production. This process starts during the design phase, but it is first tested during prototyping. It details the BOM, processes, capabilities and technologies needed for a new product production.
A good DFM will verify layout, board complexity, via placement, surface finish, and other board specifications to ensure every process, procedure and component works as it should. This manufacturing framework ensures smooth prototype execution and is designed to cut down on rework and unneeded iterations. Work with your CM during the design and prototype stage to implement your DFM to save time and costs.
Account for All Costs
Prototyping is often seen as a short-term stage, but overlooking its associated costs can lead to long-term inefficiencies. Beyond assembly and material costs, delays during prototyping can slow down your overall project, impacting its value and production timelines.
Always consider delay and idle time impacts. Additionally, future production costs should always factor in. Using unique or hard-to-find components as part of your design when more common items will suffice will have far-reaching impacts on production costs and timelines. It could even result in a redesign sooner rather than later.
Digital manufacturing platforms like MacroFab offer tools to compare pricing for different quantities and configurations, helping you select the most economical option for your project. "Extra" boards offer a chance to test and tweak a design before running your next iteration. This flexibility minimizes waste while ensuring your prototype aligns with both current needs and future production goals.
Prototyping with Precision
Building your PCBA prototype is an essential milestone to showcase the capability of a new project. But it’s only the first step in a larger process. Make sure to keep focus on the real goal: creating a quality product that can be manufactured successfully at scale.
Using the tips mentioned above will help you save time, money and effort and minimize waste as you work through the prototyping process and move to manufacturing at scale.
Related Topics
PCB Antenna Design: A Step-by-Step Guide
Step-by-step guide to the PCB antenna design process, providing practical tips to help you successfully integrate the antenna into your wireless product.
For Electronics Engineers: Top 10 Circuit Break Episodes
Enjoy these handpicked episodes designed to spark your imagination and fuel your passion for electronics.
Top 10 Electronics Podcasts You Should Listen To
This curated list of top electronics podcasts is tailored for those trying to keep up with the rapidly evolving tech world.
Choose the Optimal Contract Manufacturer for New Product Prototyping
If you’re struggling with building a prototyping plan for a successful product launch, find more information in this white paper.
About MacroFab
MacroFab offers comprehensive manufacturing solutions, from your smallest prototyping orders to your largest production needs. Our factory network locations are strategically located across North America, ensuring that we have the flexibility to provide capacity when and where you need it most.
Experience the future of EMS manufacturing with our state-of-the-art technology platform and cutting-edge digital supply chain solutions. At MacroFab, we ensure that your electronics are produced faster, more efficiently, and with fewer logistic problems than ever before.
Take advantage of AI-enabled sourcing opportunities and employ expert teams who are connected through a user-friendly technology platform. Discover how streamlined electronics manufacturing can benefit your business by contacting us today.