MacroFab Blog
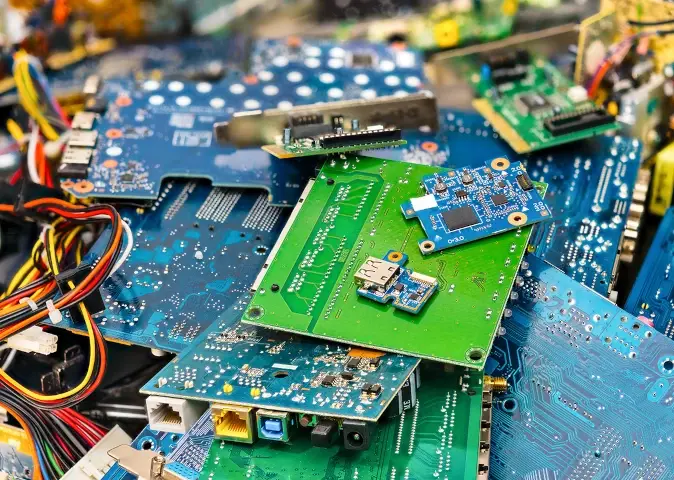
Globally, the use of high-tech electronics continues to grow. Worldwide, the number of households with electronic devices increases every year, and each person owns more devices. In addition, connected devices have appeared in every industry from healthcare to retail, from the factory floor to the agricultural field.
Though this trend has an undeniable positive impact on the electronics manufacturing industry by increasing orders, it also adds urgency to a growing problem: manufacturing waste.
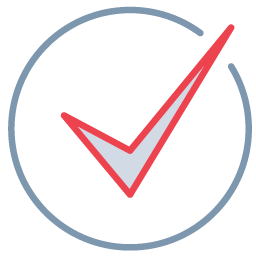
Checkpoint
American manufacturing can further limit waste thanks to its superior level of automation.
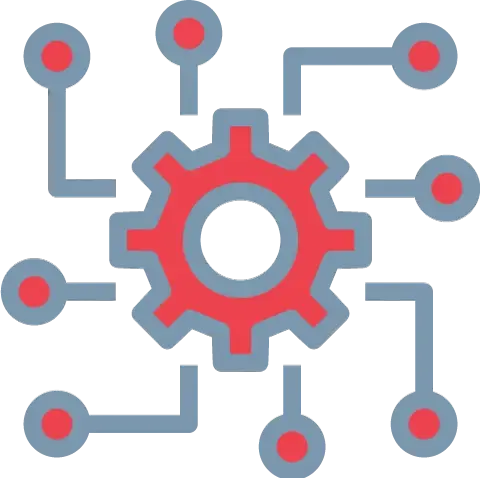
This term may bring to mind piles of end-of-life PCBA boards, but manufacturing waste encompasses much more than that. Today, businesses are generating more electronic waste in the form of expired raw materials and inventory, but also in time, transport, and motion waste related to poor supply chain practices.
Each type of waste can significantly inflate business expenses and make a negative impact on your company’s environmental, social, and governance (ESG) reputation. It falls on supply chain managers and experts to do everything in their power to minimize this electronic waste. What do supply chain experts need to know now?
Why ESG Initiatives Matter
When the pandemic first spread across the world, it broke traditional supply chains. Businesses that rely on PCBAs are now aware it’s time to rethink this method of moving goods. In addition to meeting their end goals, these companies realize they must now make good decisions for workers, the environment, and people as a whole to move into the future.
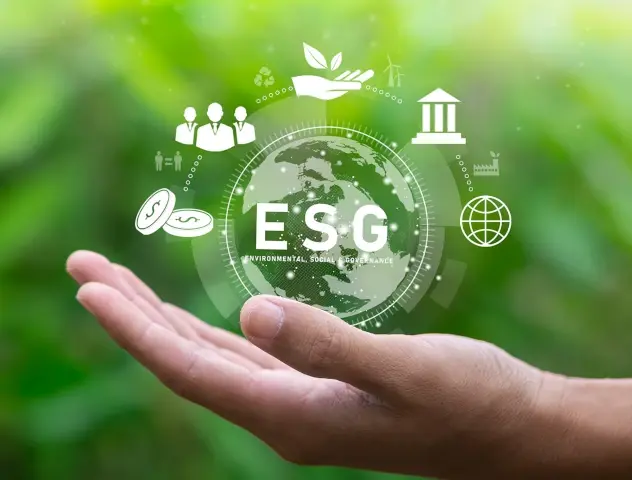
As a result, ESG initiatives are becoming more common across industries. Monitoring actions toward environmental protection and social responsibility can have a multifaceted effect on future business success. This includes
- Solidifying relationships with customers. The creation of ESG policies and their documentation can ensure that customer interest in ethical dealings can be supported.
- Enhanced reputation. Organizations can ensure alignment between their leadership team and business decision-makers by proactively addressing ESG priorities and compliance. As a result, costly mistakes are less likely to occur.
- Impact on funding and strategic alliances. Potential or active borrowers may be required to meet certain ESG policies or related metrics as lenders’ policies continue to evolve. Additionally, potential business partners may reconsider mergers or acquisitions if a business’s reputation is damaged by its (lack of) ESG actions.
E-Waste Factors You Can Control
It is important for supply chain managers to maintain control over electronic waste production. Controllable factors include
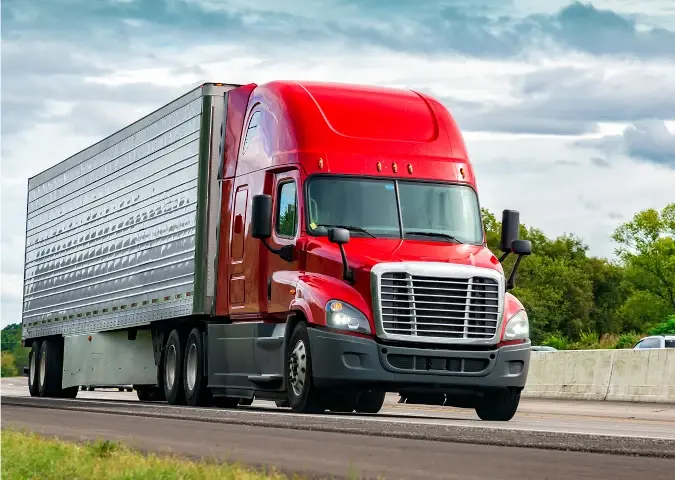
- Transport waste: costs associated with moving components, materials, and products more than necessary.
- Inventory waste: This refers to all expenses that are tied to the poor management of inventory. An example would be inadequate raw material management or product component management.
- Motion waste: Motion waste refers to the expenses, including time, associated with excessive movement of tools and people required for a plant’s production process.
- Waiting waste: The idle time, downtime, and inefficiency caused by failures of equipment, waiting for materials, or production bottlenecks.
- Defects waste: Expenses incurred due to product revisions and destruction of defective products. Additionally, it includes costs associated with product recalls, lost eputation, and replacing defective units.
Waste can affect your company’s operations and ESG initiatives in a significant way. It is therefore imperative that supply chain managers work closely with business leaders to examine policies and procedures to limit impact through proactive strategies. Making sure key parameters are met, designing for manufacturability and testing, and decreasing material use through smarter, more efficient designs can all make a significant difference in your overall waste profile.
Thinking about reshoring but not sure what to factor in? Read Should You Reshore? 5 Helpful Graphs now.
Managing E-waste Through Reshoring
The issue of electronic waste is a significant one, but businesses can improve their efficiency to eliminate wasted time and lessen their environmental impact. One of the most effective ways to achieve these goals is through reshoring.
Supply chain experts can reduce the amount of e-waste generated by their companies by reshoring by
- Reducing Transport Waste: Reshoring ensures that finished products are closer to end users when they leave the factory. Localization provides efficient and advantageous transportation methods, which eliminates the need to rush orders in case of poor planning or unexpected bottlenecks. Supply chain managers can also reduce transport waste by sourcing semiconductors needed for electronic goods closer to home as more domestic factories come online under the CHIPS Act.
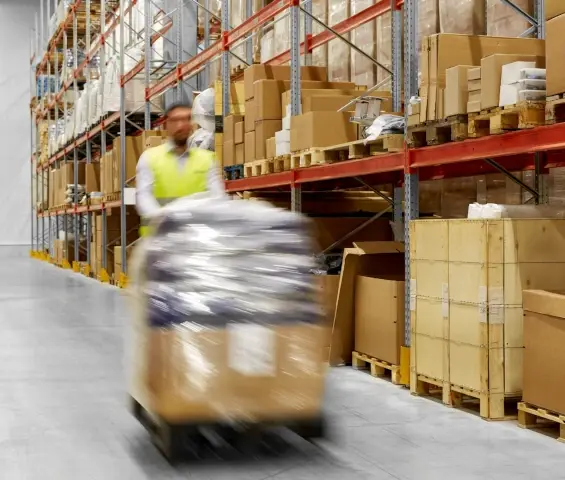
- Minimizing Motion Waste: Motion waste occurs within a workspace. Motion waste can-and does-get minimized in manufacturing facilities in the APAC region. Nevertheless, American manufacturing can further limit waste thanks to its superior level of automation. Automation can significantly reduce motion waste by optimizing repetitive tasks as much as possible. It is therefore possible to substantially decrease motion waste by reshoring PCBA production closer to home.
- Streamlining Waiting Waste: Waiting waste almost always results from bottlenecks. The benefit of reshoring production is shorter supply chains, fewer bottlenecks, and more efficient operations. As a result, you eliminate the risk of unforeseen events caused by weather, political disruptions, or changes in international transportation. Visibility also increases with closer operations, so downtime and idle time are reduced.
- Minimizing Defect Waste: A perfect manufacturing world would get it right the first time, every time. However, defects in the real world are inevitable. By reshoring to work with vetted manufacturing partners that take process control seriously, operational efficiency can be improved. This is largely due to proximity and communication: if your manufacturing partner speaks the same language and works in the same time zone, maintaining quality control is easier, while tracking and documenting changes occurs more smoothly.
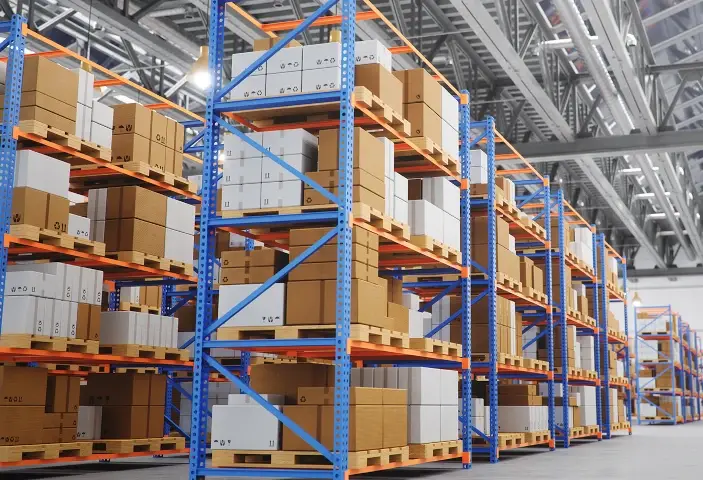
- Managing Inventory Waste: Companies that reshore their operations have an easier time managing their inventory since their products don’t require as much lead time. As a result, businesses can maintain less inventory in reserve and are able to respond more quickly to increases in demand. This reduces the risk of creating an overbuying scenario that results in unused inventory that becomes waste.
In the end, these are some of the ways reshoring operations domestically can reduce e-waste and improve ESG performance. As more companies are looking at the benefits of reshoring PCBA fabrication closer to home from Mexico and China, their operations should become more efficient, allowing them to address supply chain issues, reduce waste, and deliver better products for their consumers.
Today, more attention is being paid to the environment than ever before. It is imperative for supply chain experts to focus on e-waste production, the source of company waste, and ways to reduce it. By reshoring, businesses can reduce logistics problems, transportation costs, and unknown risks while better satisfying end-user expectations.
Related Topics
How ESG Initiatives Create Value for the PCBA Industry
ESG (Environmental, Social, and Governance) initiatives, once little more than a buzzword, have become crucial to a business’s success and longevity.
Companies Bring Electronics Production Home From Asia
Lately, numerous companies have begun reassessing their global value chains and moving electronics production closer to home.
What’s Changing in US Electronics Manufacturing
In the coming years, reshoring electronics manufacturing may be the key to maintaining the US economy's stability.
No Headaches, All the Benefits
Embark on a straightforward transition to electronics manufacturing with MacroFab.
About MacroFab
MacroFab offers comprehensive manufacturing solutions, from your smallest prototyping orders to your largest production needs. Our factory network locations are strategically located across North America, ensuring that we have the flexibility to provide capacity when and where you need it most.
Experience the future of EMS manufacturing with our state-of-the-art technology platform and cutting-edge digital supply chain solutions. At MacroFab, we ensure that your electronics are produced faster, more efficiently, and with fewer logistic problems than ever before.
Take advantage of AI-enabled sourcing opportunities and employ expert teams who are connected through a user-friendly technology platform. Discover how streamlined electronics manufacturing can benefit your business by contacting us today.