MacroFab Blog
Signal degradation can occur on any PCBA, but can be most challenging to design for when the system operates at a high speed and frequency. High-speed analog and digital signals must be taken into account when designing printed circuit boards that support higher frequencies.
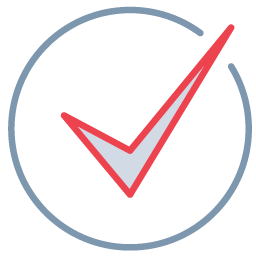
Checkpoint
It is difficult to protect each key signal from all noise intrusions, but this must be done to design an effective PCB assembly.
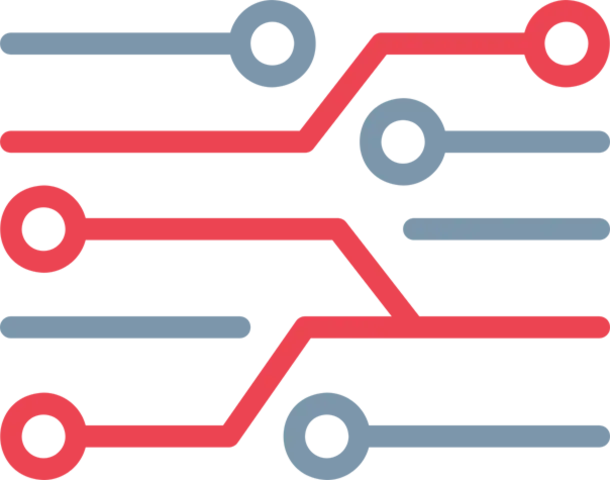

The system is susceptible to many factors that can degrade performance and distort the signal. We will discuss several potential signal integrity problems, their root causes, and how to resolve them.
Keeping a signal’s original characteristics intact and pure without corrupting it is signal integrity. This may sound easy in concept, but in practice, many challenges must be overcome. In real-life, other interference within the PCB might negatively impact signals.
It is difficult to protect each key signal from all noise intrusions, but this must be considered as early PCB design decisions get made to create effective PCB layouts. When working with your CM partner early in the development process, they can help you develop your design for manufacturing (DFM) plan, which will address many of the factors below.
Factors that may affect signal integrity include:
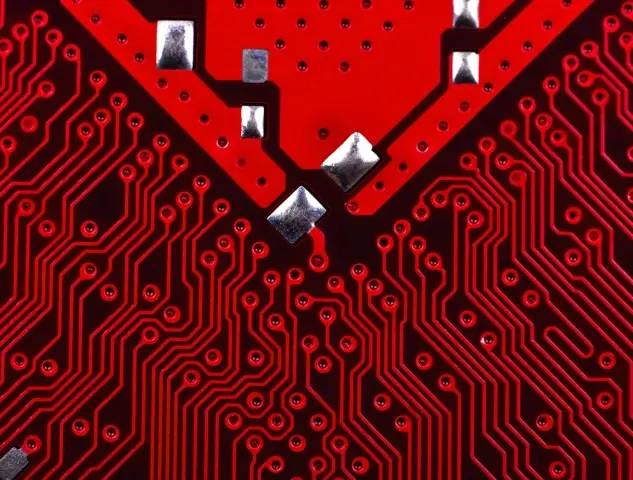
- Attenuation – The loss of signal power from the transmitter to the receiver. A match in impedance between the source and destination will ensure maximum power transfer.
- Crosstalk – Allowing some characteristics of one signal to be transferred to another unrelated signal is considered crosstalk. The key signals need to be kept separate from other noisy signals, buffered spatially, and held at high impedance.
- EMI – The term Electromagnetic Interference refers to intrusion by other unintentional RF signal radiators that can corrupt the signal of interest. Use ground shielding or metal RF isolation if needed to maintain the proper isolation between key signals within the routing. Learn more about EMI and EMC compliance.
- Interconnect effects – Traces using a connector or simply have inter-plane vias will have an interconnect that could impact the signal. Interconnects often have a different impedance than traces, causing abrupt signal distortion. To ensure there are no mismatch issues that cannot be navigated, layout tools should match the interconnect impedance as closely as possible.
- Ground bounce – When a fast-changing signal corrupts a pure ground, a phenomenon called ‘ground bounce’ occurs. This is the effect of a large signal change imposed upon a quiet ground. Keep ground planes and ground traces wide to maintain low impedance paths. The impedance from signals to ground should always be well controlled.
- Propagation delay – While it is difficult to eliminate all delays, for those signals where a long delay is detrimental, minimize the trace flight distance between components. This will shorten the duration of the propagation delay.
- Reflections – Signal reflections are unwanted and create artifacts within signals of interest. To negate reflections, transmission trace lines must maintain consistent impedances. Remove trace stubs where a divergent path allows a splinter trace to take an unmatched impedance path.
- Signal characteristics - Each signal will have electrical characteristics that make it valuable. In addition to high voltage characteristics, there are digital and analog characteristics, quiet supply voltages, and control signals. To avoid any signal corruption, it is important to know each signal’s characteristics and route them accordingly.
- Supply voltage fluctuations – Power supply stability is important to prevent unwanted operation or even failure due to improper supply conditions. Therefore, maintaining a low impedance wide trace for power supplies or even a power plane works best. Additionally, using all the recommended bypass capacitors to filter noise along the supply path will mitigate unwanted noise from coupling onto the supply node at the component input pin.
- Impedance – To prevent voltage drops from a source, the path impedance of traces or planes of a supply should be as low as possible. Similarly, ground planes should also have a lowimpedance path. The impedance between independent mutually exclusive signals should be as high as possible to prevent the cross-talk phenomenon mentioned above. Each transmission line needs to maintain a key impedance target to match the source and transmitter, often 50 ohms to ground. Differential transmission lines must be well-matched.
While there are many factors that could cause signal integrity problems in your PCBA development, we have discussed the most common 10 problems and mitigation techniques here. With a full design for manufacturing plan, these challenges can be curtailed and integrated into your development process.
Related Topics
PCB Antenna Design: A Step-by-Step Guide
Step-by-step guide to the PCB antenna design process, providing practical tips to help you successfully integrate the antenna into your wireless product.
Top 10 Electronics Podcasts You Should Listen To
This curated list of top electronics podcasts is tailored for those trying to keep up with the rapidly evolving tech world.
MacroFab's Certifications Benefit PCBA Production
Your PCBA production must be secure and reliable for your products to compete in the market. We have listed our certifications and how they benefit you.
Additional Resources
Read more about other impedance-matching techniques.
About MacroFab
MacroFab offers comprehensive manufacturing solutions, from your smallest prototyping orders to your largest production needs. Our factory network locations are strategically located across North America, ensuring that we have the flexibility to provide capacity when and where you need it most.
Experience the future of EMS manufacturing with our state-of-the-art technology platform and cutting-edge digital supply chain solutions. At MacroFab, we ensure that your electronics are produced faster, more efficiently, and with fewer logistic problems than ever before.
Take advantage of AI-enabled sourcing opportunities and employ expert teams who are connected through a user-friendly technology platform. Discover how streamlined electronics manufacturing can benefit your business by contacting us today.