MacroFab Blog
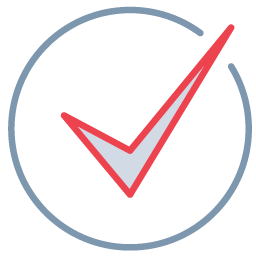
Checkpoint
The number of next-generation manufacturing facilities in the US using stateof-the-art processes has decreased from 25 in 2002 to only three in 2020. The CHIPS Act hopes to reverse this trend.
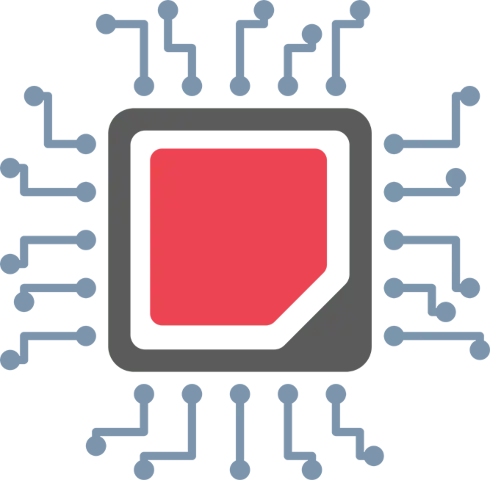
Throughout the electronics manufacturing and assembly industry, technology advances constantly. Constant change keeps the market from standing still.
Instead, devices get smaller all the time. Power requirements shift to different portions of a system. As designs become more complex, smaller form factors and higher component counts challenge our previous electronics manufacturing paradigm.
As a result, PCBA design innovations continue to expand to support the solutions demanded by the market. To maintain their company’s competitive edge, engineers must continually seek out new options and keep up with market changes. Take note of these six trends within the electronics industry.
How Long will Moore’s Law Last?
In 1965, Intel Corp. founder Gordon Moore wrote that with new integrated circuits, “the cost per component is nearly inversely proportional to the number of components.” His 1965 forecast went on to predict that the number of components fabricated on an integrated circuit would double every year until it reached 65,000 by 1975.
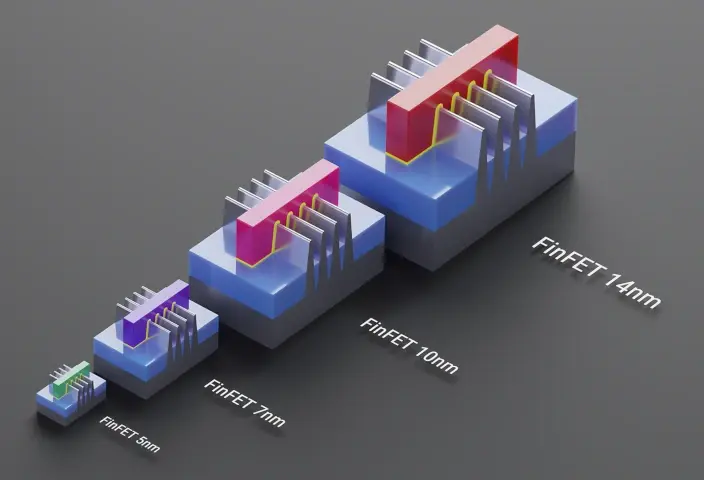
Moore’s prediction proved to be accurate. Moore revised that idea in 1975 in what became known as Moore’s Law, describing the doubling of transistors every two years. In the last two decades, however, the doubling pace has fallen behind the two-year cycle due to new challenges. However, the cycle has not halted completely. New designs and lithography methods continue to shrink component size, but these methods require increasingly more expensive fabrication techniques.
Meanwhile, fab plants have become less willing to invest in these costly processes. The number of next-generation manufacturing facilities in the US using state-of-the-art processes has decreased from 25 in 2002 to only three in 2020. The CHIPS Act hopes to reverse this trend.
Chiplets
Chiplets can work together as part of a multi-chip module, or MCM, creating a single integrated circuit. This ability to collaborate overcomes Moore’s Law’s limitations as well as the difficulties associated with monolithic designs. A chiplet is a tiny integrated circuit (IC) with well-defined functionality, perfect for building hardware tailored for specific applications like TinyML. TinyML focuses on machine learning for resource-constrained devices, and chiplets offer a modular approach that creates efficient hardware for smaller devices.
Chiplets allow a more flexible module solution to be designed with targeted functions that leverage the strength of each chip. Not only are chiplets useful for integration into a large module, but their technology can be reused in other modules that require similar functions, bringing more efficiency to the project development.
In addition, fabrication technology nodes that favor certain performance can be tailored to fit their specific function. This includes memory, data processing, analog, power, and RF. This lends credence to the notion that smart technology partitioning is more flexible but requires more advanced assembly for a complete module.

Connected, Before and After Manufacturing
The Internet of Things (IoT) and the cloud make connected manufacturing possible, through what is known as the Industrial IoT (IIoT). These connected technologies improve the efficiency, productivity, reliability, and traceability of materials and finished goods.
The four elements that manufacturers use to drive this revolution are:
- Devices – collect and sense data about the manufacturing environment and machine health.
- Communication– Leverage wireless and industrial networked machines that communicate between each other and to a cloud server.
- Data Storage – Data can be stored locally or on a server depending upon the required analysis and real-time requirements.
- Data Analytics – algorithms intelligently process data to predict machine wear, unplanned maintenance, and manufacturing order trends over time.
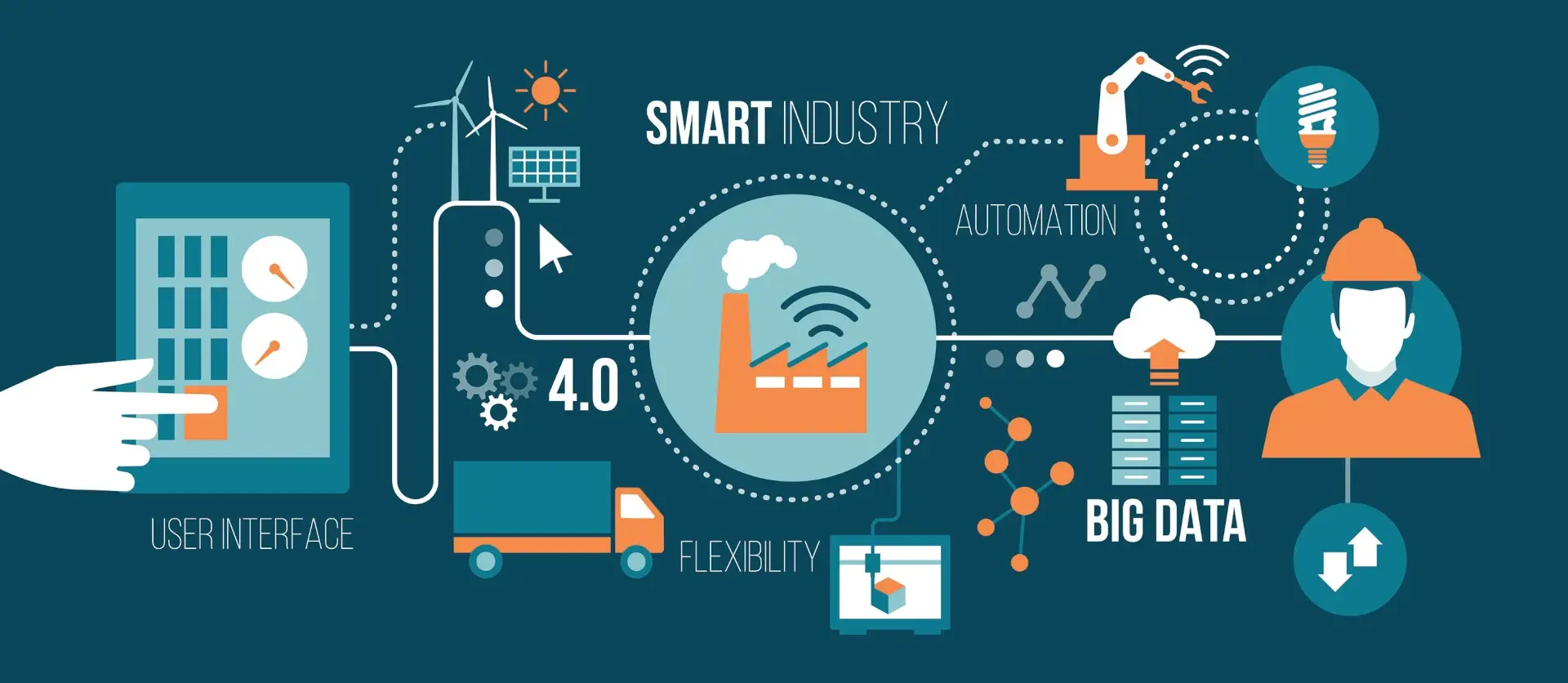
Communication systems, industrial controls, aerospace, automotive electronics, and automation across sectors benefit from embedded intelligent devices. The International Data Corporation (IDC) predicts there will be more than 41 billion connected IoT devices in the world by 2025.
The confluence of these technologies enhances factory manufacturing capabilities and allows more efficient production tracking. It reduces waste and allows intentional activity instead of repairs or waiting on gaps in machine setup changes.
High-Density Interconnect (HDI)
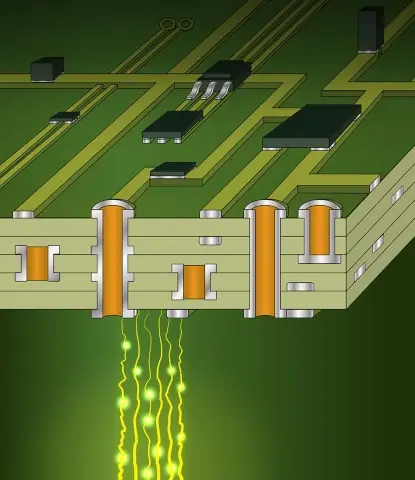
High-Density Interconnect (HDI) PCBs use some combination of the following assembly technologies: micro vias, blind and buried vias, built-up laminations, or highspeed signal bandwidth materials. PCB fabrication has been constantly improving and evolving with changing technology that requires accommodations for smaller and faster products. Specifically, HDI PCBs offer:
- Increased signal sharpness. Signals travel shorter distances thanks to HDI PCBs’ compact size. There is a performance increase, even if it is subtle.
- Physical reliability. HDI PCBs have less likelihood of losing physical connections.
- Lighter, cooler material. HDI PCBs tend to be lighter and cooler than traditional PCBs made from fiberglass, copper, and other materials. This can improve performance and heat dissipation to handle high temperatures better.
- Design improvements. Compact and versatile builds are enabled by blind and buried vias.
To accommodate the denser boards within a constrained area, HDI was developed as a means to force more electrical content into the same, or smaller area. Compared to traditional PCBs, HDI boards are more compact and have smaller vias, pads, copper traces, and spaces.
HDI PCBs have more dense wiring that results in a lighter weight with a more compact, lower layer count PCB. This provides an inherently smaller and lighter system than otherwise would be possible.
By working with your CM during the design stage for your project, a design for manufacturing plan (DFM) can determine if HDI PCBs are needed for your project and how to design for them.
Flexible PCBs
As wearables like smartwatches and IoT devices require durable, small designs, flexible PCBs have become one of the fastest-growing circuit board design trends.
To leverage multiple PCB planes in a single system, flexible or rigid-flex PCB material has become increasingly more pervasive. A rigid-flex PCB has design features that allow for the typical rigid board with the option to introduce flexible portions.
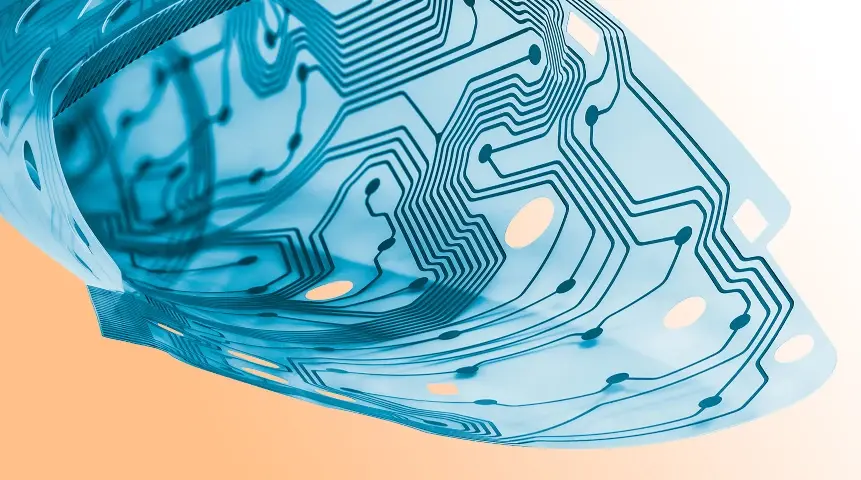
As part of the manufacturing process, layers on flexible PCBs are etched away, allowing flexible layers to be exposed for bendable angles. Boards can be bent up 180 degrees to interface with other PCB planes, reducing system area and enhancing design options.
Additionally, flexible PCBs remove the need for connectors and ribbon cables that otherwise can be unfriendly to high-speed signals by introducing electrical noise and reflections. Instead, flexible PCBs maintain signal integrity with the trace impedance required as if a signal was transmitting down a typical PCB transmission line.
PCBA design has been impacted by wearable technology. Read about it in our Impact of Wearables on PCBA Design: Their Past and Future now.
Listen to this classic Circuit Break Podcast to learn more about Flex and Rigid-Flex PCB assemblies.
Direct-from-Desktop Ordering
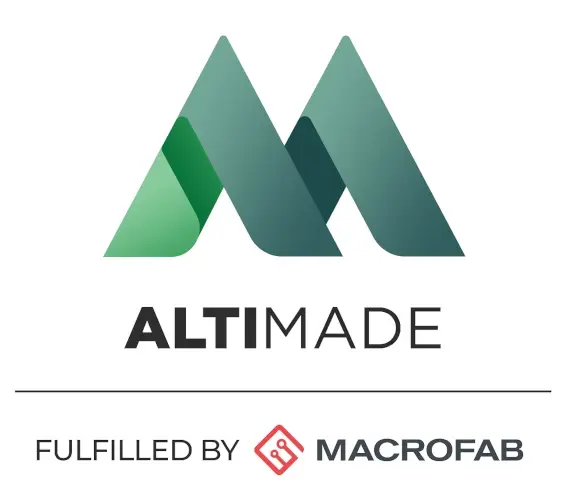
When you are ready to start your design project, you will want your CM partner to be involved in the process for maximum success. A design for manufacturing (DFM) plan will encompass your design, manufacturing needs, unique requirements, bill of materials, fabrication and assembly options, and quotes.
Rather than having to call several times to determine fabrication, assembly, and component kitting separately, it is possible to handle all these using the Direct-from-Desktop ordering process called Altimade.
By connecting Altium design tools to MacroFab’s factory lines, Altimade simplifies and streamlines the design-to-manufacturing process. With one click, customers can place orders directly from their workspace. By using this online tool, you will have all the information you need to make your project a success.
Read another PCBA design article now to learn how to avoid common design failures.
Conclusion
PCBA design innovations will continue to push the electronics manufacturing and assembly industry forward to keep pace with technology. Tracking the activity in the cloud through the IIoT pushes the industry forward for more efficiency. Flexible PCBs offer new design options for higher density, along with HDI connectivity. Reusable chiplet functions make smart partitioning of functional blocks a better solution for advanced modules. While Moore’s law is no longer a hard and fast rule, the technology trends will continue in assembly and manufacturing to allow more advanced designs. Use the Direct-from-Desktop Ordering tool Altimade to get started.
Related Topics
MacroFab vs. PCB Manufacturing Brokers: Why Direct Matters
This blog explores the key differences between MacroFab and manufacturing brokers, and why direct manufacturing is the optimal choice for PCBA needs.
How MacroFab Listens and Delivers
We’ve revolutionized the traditional PCB manufacturing process, offering a online platform supported by a network of high-quality North American factories.
Schematics to Reality: Innovate with Custom PCBs at MacroFab
A glance at how MacroFab's platform can turn concepts into a real functional product. This can be done with the many services that MacroFab offers.
Build Better With MacroFab
How Our Platform WorksAbout MacroFab
MacroFab offers comprehensive manufacturing solutions, from your smallest prototyping orders to your largest production needs. Our factory network locations are strategically located across North America, ensuring that we have the flexibility to provide capacity when and where you need it most.
Experience the future of EMS manufacturing with our state-of-the-art technology platform and cutting-edge digital supply chain solutions. At MacroFab, we ensure that your electronics are produced faster, more efficiently, and with fewer logistic problems than ever before.
Take advantage of AI-enabled sourcing opportunities and employ expert teams who are connected through a user-friendly technology platform. Discover how streamlined electronics manufacturing can benefit your business by contacting us today.