MacroFab Blog
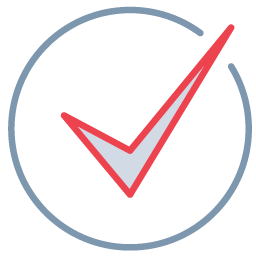
Checkpoint
In the coming years, reshoring may be the key to maintaining the US economy’s stability.
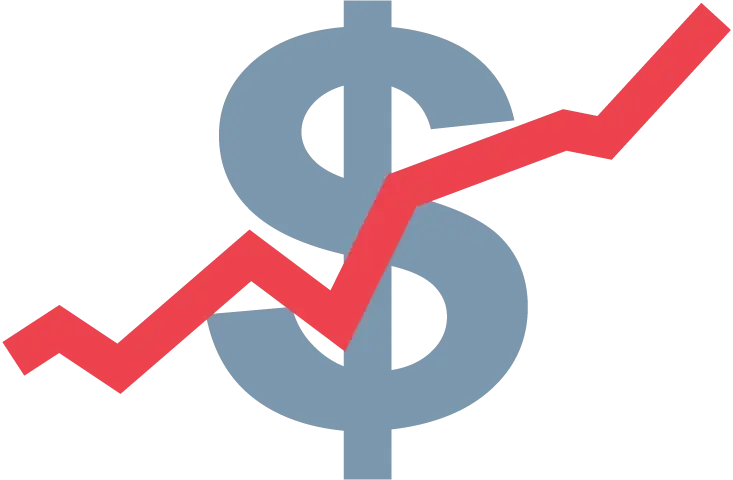
The tide is turning for electronics manufacturing in the United States. After years of decline, the industry is experiencing a resurgence driven by several key factors. This resurgence has significant implications not only for the overall US economy but also for the future of electronics manufacturing itself.
Prior to the pandemic, U.S. manufacturing had begun to rebound, adding 1.3 million jobs between 2010 and 2019. This represented a 25 percent return of jobs lost a decade earlier, but technological advancements stabilized global manufacturing output, exports, and GDP share. IPC estimates that today, the electronics manufacturing sector directly supports 1.3 million well-paying U.S. jobs.
But today’s global economy places U.S. manufacturing at a tipping point once again. Economic pressures suggest a global recession is close at hand or may have already begun, affecting productivity across the board.
At the same time, political and pandemic pressures in the APAC region have forced many American companies to rethink their global manufacturing strategies, encouraging many to consider nearshoring or reshoring their production, adding a boost to the domestic economy. This trend offers significant benefits for both manufacturers and consumers.
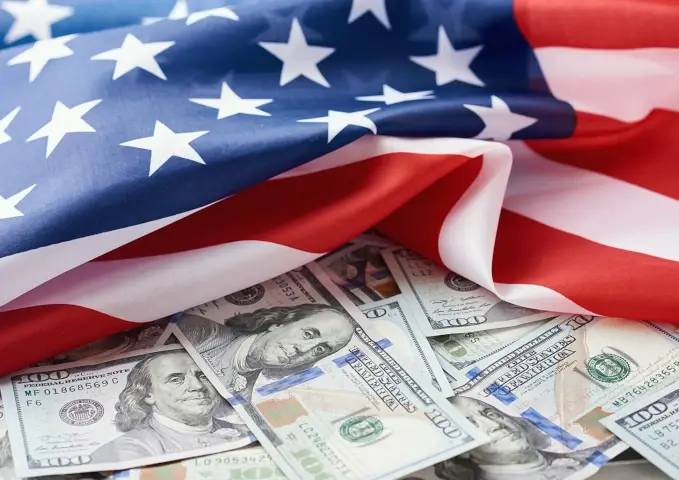
Further, a wave of investment in next-generation technologies–including digital technologies, artificial intelligence, and the growing connection between supply chains, design environments, and the manufacturing floor–is expected to further benefit US electronics manufacturing and US companies in the coming years.
- Enhanced Supply Chain Resilience: Reshoring shortens supply chains, reducing the risk of disruptions caused by international shipping delays, political instability, or trade wars. This improved resilience is critical for the electronics industry, which relies on a constant flow of components and materials.
- Improved Quality Control: By bringing production closer to home, manufacturers can exert greater control over quality standards and ensure their products meet stringent specifications.
- Faster Time to Market: Shorter supply chains also lead to faster time-to-market for new electronic products. This allows companies to capitalize on emerging trends and respond more quickly to customer demands.
Reshoring and improved technology could maintain a robust, thriving domestic manufacturing economy despite the impending possible global recession. What impact will it have on the US economy as a whole?
Here are some of the major changes occurring in the American electronics manufacturing industry today, and the possible implications of increased American reshoring.
Making American Electronics Manufacturing Digital
Digitization is becoming more prevalent in American manufacturing. A growing number of leading US electronics manufacturers are using digital technologies to improve key performance indicators. Among improvements, early adopters see
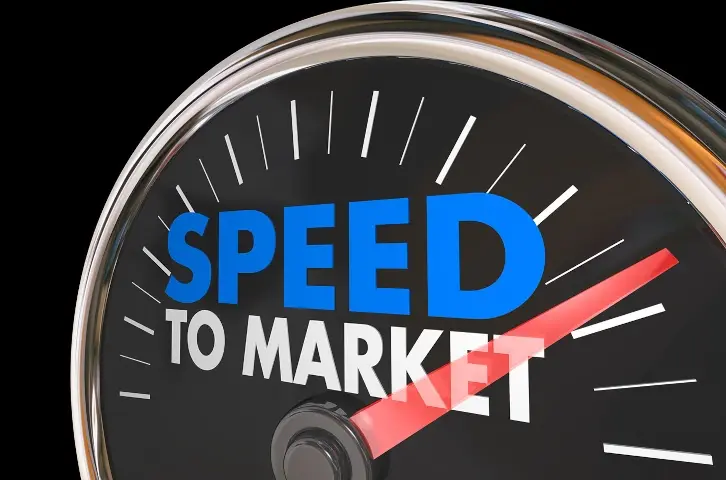
- Increased Productivity: Digital manufacturing can increase electronics factory outputs while reducing operating and product costs.
- Improved Agility: Digitization increases production changeover speed, reduces lead times, and improves on-time delivery metrics.
- Enhanced Speed to Market: Enhanced communication reduces design time and reduces the number of iterations required, accelerating the time to market.
- A Positive Impact on Sustainability: Digitization can improve energy efficiency, reduce waste production, and reduce greenhouse gas emissions.
Businesses can also meet their customers’ demands more easily with the help of digital technology. Traditionally, complex orders would take longer to process due to longer supply chain lead times. Due to digital technology, this is not always true. A digital supply chain provides businesses with greater flexibility and visibility through connected APIs, giving them more control over costs and availability.
The Value of Sustainability
Sustainability has also become important in the United States electronics manufacturing sector.
Today, end-users care more about where they spend their money than ever before. They want to know that companies are doing everything they can to protect the environment. According to the United States Environmental Protection Agency, sustainable manufacturing focuses on creating manufactured products using sound economic processes that minimize negative environmental impacts.
There are several ways companies in the manufacturing sector can make their operations and supply chains more sustainable to meet the demands of customers while also driving additional value through ESG (Environmental, Social, and Governance) initiatives. This includes limiting:
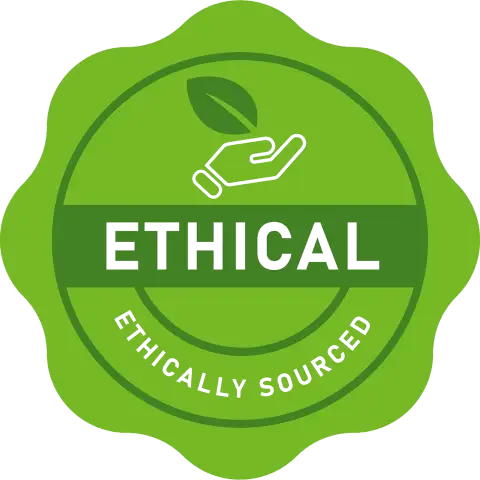
- Engineering waste: Companies can reduce engineering waste to meet customer expectations and become more sustainable. Reducing engineering waste can also help companies maximize the value of every dollar they invest in engineering. Often, this comes down to time waste, including delays and idle time, which can have far-reaching effects on production costs and timelines.
- Sourcing waste: Companies that focus on ethical sourcing practices can drive sales by meeting client demands. By partnering with ethical suppliers, manufacturers can also protect themselves against regulatory liability. Again, delays can create time waste, so consider creating an alternative part list, if possible.
- Production waste: Production waste can be reduced through the use of smart technology, more efficient production, and the use of green energy to power production facilities. Examples of green energy include hydropower, wind power, and solar power.
- Transportation waste: By optimizing supply routes, supply chain experts can reduce greenhouse gas emissions and boost sustainability efforts. By optimizing delivery and production schedules, navigating traffic jams, shortening routes, and saving time on the road, digital technology can help.
- Aftermarket waste: Companies can make changes to how they sell, use, and dispose of their products to minimize waste, maximize recycling, and match the expectations of clients.
Supply chain experts must understand what steps their company should take to become more sustainable. By doing so, they gain the trust of consumers, business partners, as well as government agencies that may look to sustainability when awarding contracts.
Many companies believe that sustainability initiatives increase customer loyalty, and several studies show that end-users are becoming more concerned about sustainability when making a purchase decision.
Resilience and Reshoring Drive Value
Businesses that want to position themselves for the future should consider reshoring and nearshoring.
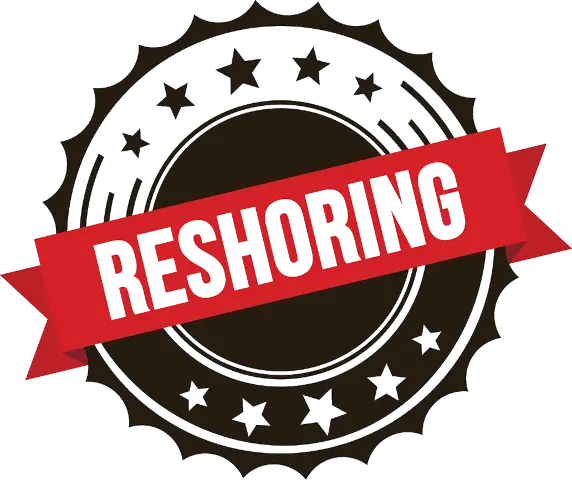
Many companies have traditionally sent production overseas to reduce labor costs, but the pandemic exposed the vulnerability of global supply chains. Delays have been commonplace. Manufacturing shutdowns happen too often. And while port delays are no longer as bad as they once were, unreliable weather patterns mean this could change in an instant. Meanwhile, increasing legislative changes, delays, and uncertainty in the political environment have made long supply chains far riskier.
Now, many businesses have seen the benefits of reshoring. When companies move their operations closer to home, they drive value by limiting risk (both known and unknown) by shortening supply chains. Meanwhile, shorter supply chains reduce total cost of ownership (TCO) and reduce risk while accelerating product development. They do this by
- Limiting the likelihood of problems arising during shipping and logistics.
Improving manufacturing strategies by avoiding many trade restrictions and tariffs
Companies can avoid government embargoes and tariffs by reshoring or nearshoring business operations.
Why Reshoring Matters Now More Than Ever
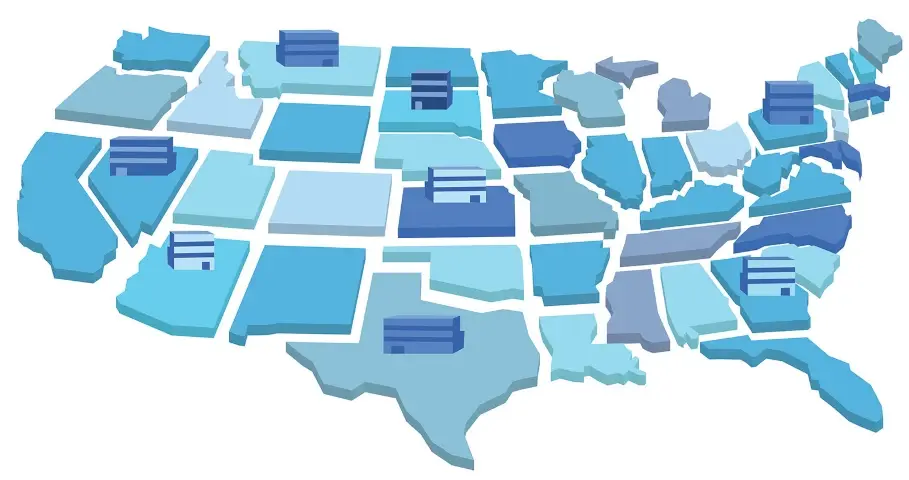
Before, lower overseas labor costs caused deep losses in the US manufacturing sector. But as productivity improved domestically and overseas wages increased, these costs have begun to equalize.
Now US-based manufacturers have opportunities to show their competitive advantage, as well as enhance customer experience through shorter supply chains, faster delivery times, and reduced tariff loads.
Experts see strong growth prospects within the electronics industry, particularly semiconductors, medical devices, and communications equipment, which are inherently important for national security and resilience.
Furthermore, when businesses manufacture domestically, it has a profound economic impact on the country’s economy. As American consumers increasingly seek out domestically manufactured products, reshoring can significantly boost demand for American-made electronics. This surge in demand can lead to increased sales, stronger brand loyalty, and a competitive edge in the market. In the coming years, reshoring may be the key to maintaining the US economy’s stability and ensuring the long-term success of businesses in this market.
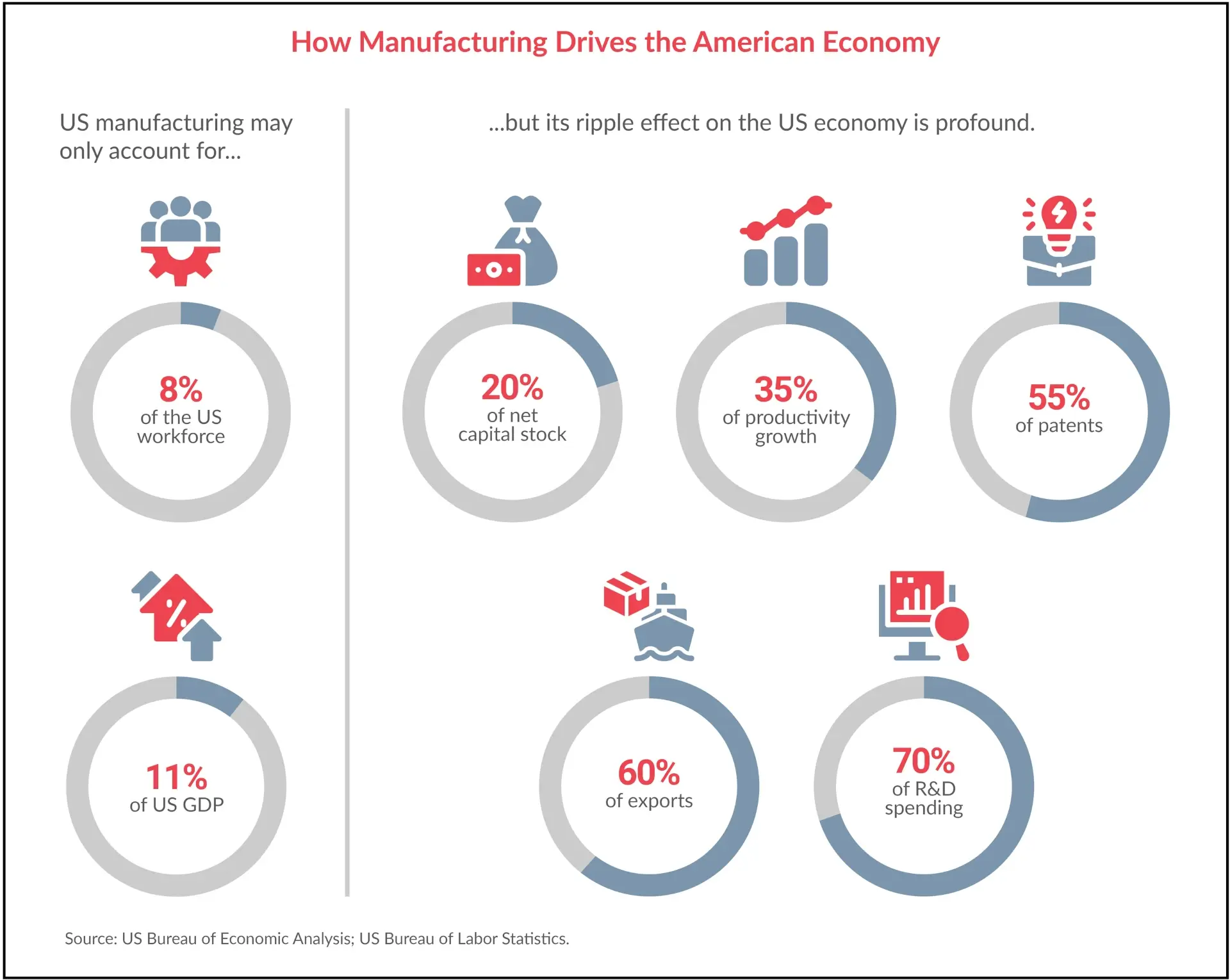
Want to know more about the benefits of domestic manufacturing? Read US PCBA Manufacturing: Eight Benefits now.
Nearshoring and Reshoring Are the Future of the Manufacturing Sector
The US electronics manufacturing sector is changing quickly, and this is perfectly exemplified by the number of businesses moving their operations back to North America. Supply chain experts must do everything they can to meet the expectations of consumers, and that means focusing on sustainability while shortening supply chains. US electronic manufacturing companies that bring their operations closer to home may be able to maintain a competitive edge when compared to other companies in the industry.
Related Topics
Companies Bring Electronics Production Home From Asia
Lately, numerous companies have begun reassessing their global value chains and moving electronics production closer to home.
Surviving the Warehousing Squeeze
The warehousing crunch has put a strain on electronics companies that rely on quick delivery of electronic components or PCBAs, especially from overseas.
Electronics Made in America? You Need Workers First
Reshoring offers a solution to persistent problems of instability, lending companies the resilience needed to succeed now and into the future.
Find out More About Reshoring with MacroFab
MacroFab Reshoring SolutionsAbout MacroFab
MacroFab offers comprehensive manufacturing solutions, from your smallest prototyping orders to your largest production needs. Our factory network locations are strategically located across North America, ensuring that we have the flexibility to provide capacity when and where you need it most.
Experience the future of EMS manufacturing with our state-of-the-art technology platform and cutting-edge digital supply chain solutions. At MacroFab, we ensure that your electronics are produced faster, more efficiently, and with fewer logistic problems than ever before.
Take advantage of AI-enabled sourcing opportunities and employ expert teams who are connected through a user-friendly technology platform. Discover how streamlined electronics manufacturing can benefit your business by contacting us today.