MacroFab Blog
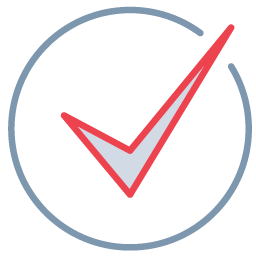
Checkpoint
Digitization eliminates the need for tribal knowledge, reducing fear of its loss.
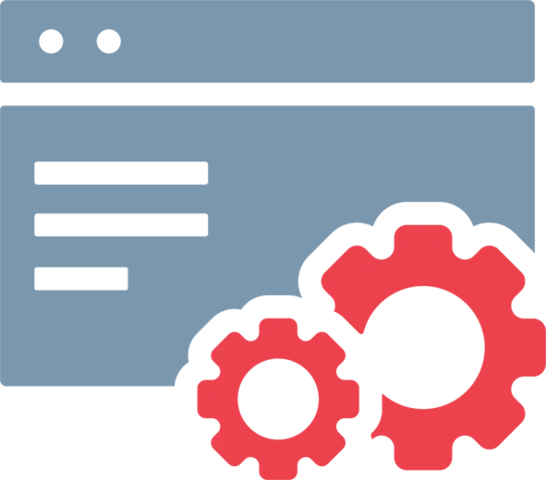
The electronic production process is prone to risk, especially today. After nearly three years, the COVID-19 pandemic is still affecting our supply chains. It’s difficult for companies to get their products to market on time. The interconnected nature of our supply chains also means organizations can’t insulate themselves from disruption.
But there are steps leaders can take to mitigate risk and protect production plans. Even though global disruptors are impossible to completely avoid, electronic supply chain teams can minimize their effects by evolving legacy processes and upgrading legacy systems.
No matter what type of business you run, the following eight tactics will help reduce electronic supply chain risk today and into the future.
Understand Supply Chain Disruption
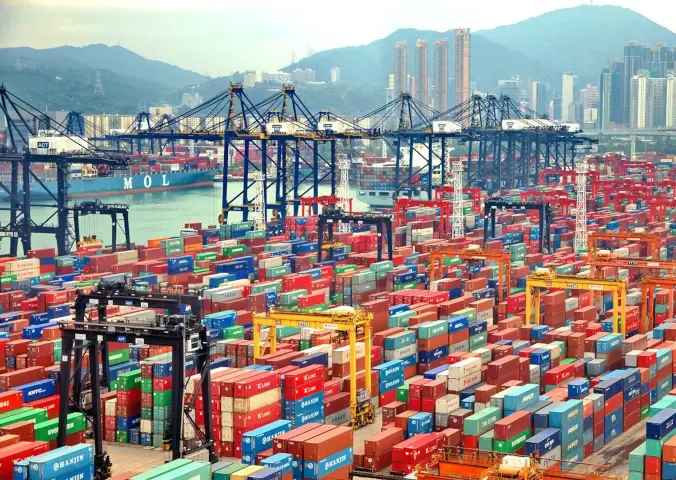
The first step to mitigating risk is understanding how disruption manifests and affects the supply chain. Disruption can surface from anywhere and spread quickly. As a result, when a crisis occurs, supply chain leaders need to first recover and then learn as much as they can.
As a first step, teams have to assess the type and scale of the current disruption. A known risk–like an important supplier with ongoing financial difficulties going bankrupt–is easy to identify in advance. But unknown risks–like a tsunami that destroys ports and shuts down global shipping for several weeks–can leave you vulnerable without notice.
Recovery begins with identifying the event’s source and the affected part of the supply chain. Once you’ve recovered, it will be easier to test how the disruption was handled by asking
- Where were you underprepared?
- What did your team do well?
- What part of the supply chain suffered the most?
- How long did it take to recover?
By answering these questions and more, leaders can discover where they have the opportunities to reduce risk going forward.
Invest In Technology
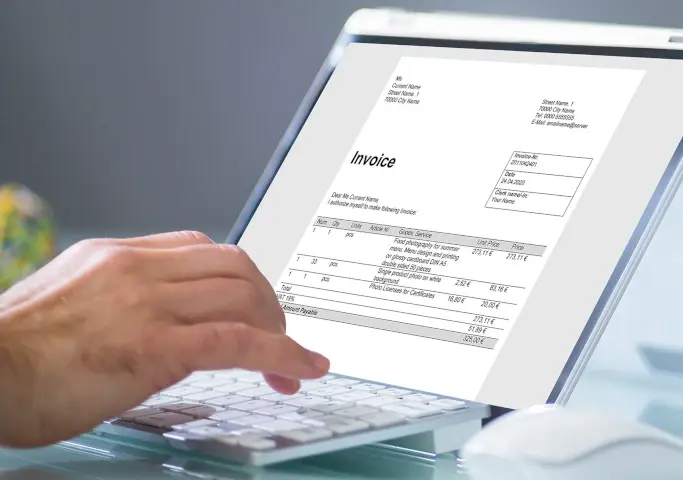
Supply chain technology has improved significantly in recent years. Companies no longer need to rely solely on human activity or analog record keeping. It is now possible to digitize so many supply chain aspects – product designs, BoMs, orders, invoices, and more.
Digitizing these assets makes them easier to store, share, and maintain. In a supply chain that allows people to access what they need when they need it, collaboration flourishes. Moreover, digitization eliminates the need for tribal knowledge, reducing fear of its loss. Data loss is also prevented.
Further, modern supply chain technology increases visibility across the supply chain. A good solution consolidates insights and helps uncover concerning patterns. Companies can use supply chain technology to assess their environmental impact, identify unusual activity, identify key metrics, and monitor their day-to-day operations.
Want to know more? Learn how a Digital Manufacturing Platform can benefit your business.
Automate Manual Processes
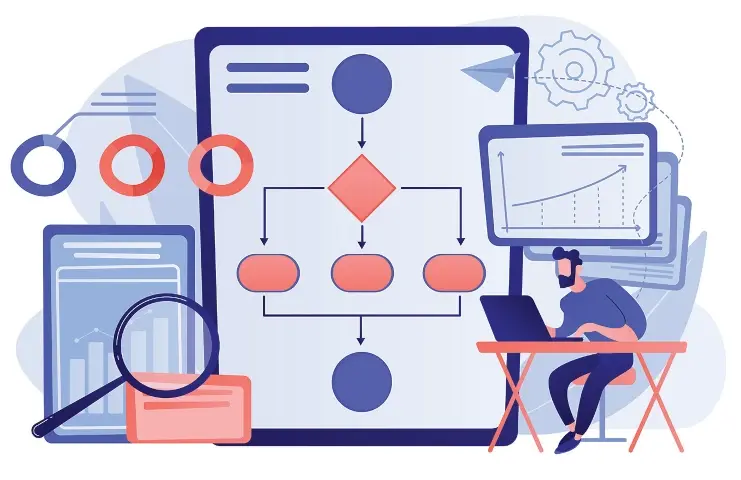
Automation maximizes supply chain efficiency. Today, companies must take swift action and make immediate decisions. As we’ve seen, supply and demand can be volatile. Component availability and manufacturing capacity can also dry up overnight. We need automation to help us keep up in such a fast-changing world.
Automation depends on digitization, which we touched on above. It’s hard to streamline analog processes. But when data and critical functionality are both available within the same digital ecosystem, it’s easier to automate.
Automation can play a role in the supply chain by generating orders and invoices based on specific triggers. Teams can also set up automated alerts around certain metrics, like component pricing or availability. And leaders can get automated updates on production progress or delays, allowing them to adapt sooner to risk.
Embrace Data-driven Analytics
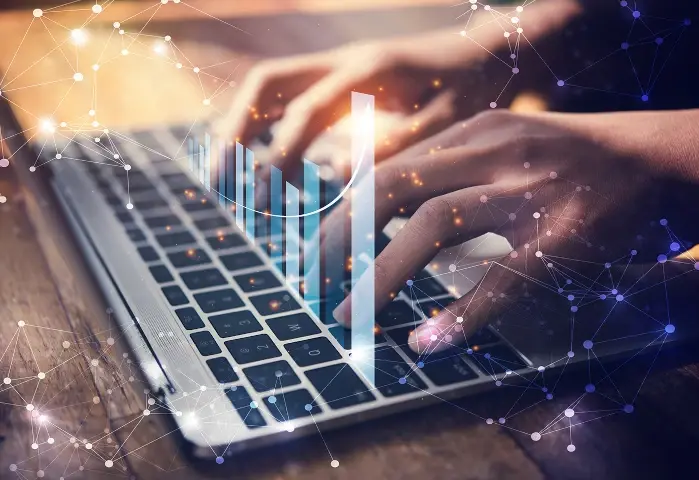
Big data has made its way into the electronics supply chain realm. Data is available to companies in greater quantities than ever before. They also have better tools for collecting, preparing, and mining this data for insights. Effective consumers of data reap four major benefits:
- The context around different interruption types is better understood. When disruption is clearly defined, recovery is easier.
- Better data provides greater insight into why certain problems occur. In this way, future disruptions can be minimized.
- Strong data capabilities open the door to predictive analytics. By understanding the past better, companies can make better predictions about the future.
- Data analytics reveal where supply chains are inefficient or ineffective today. A rich data set gives leaders the confidence to invest in their supply chains.
Create a Resilient Team
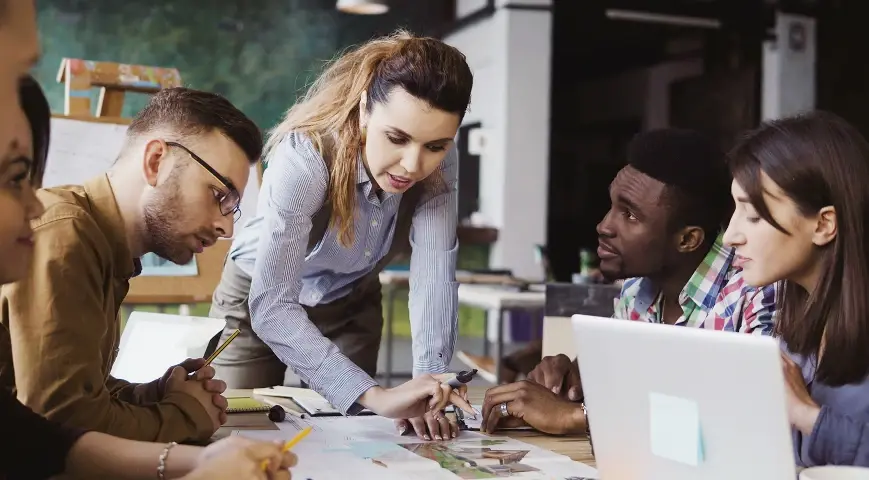
Companies can’t rely solely on new technologies to help mitigate risk. Leaders have to nurture resilient workforces to meet today’s challenges. In particular, they need to provide better opportunities for training and professional development.
Executives should also encourage more open collaboration and creative problem-solving. For many people in the industry, working in silos is a familiar habit. In order for teams to adapt to a new mindset, leaders must provide them with guidance. To solve hard problems, people must work together across functions to build a resilient supply chain and workforce.
Follow a Multi-Sourcing Approach
Diversification is another way to reduce supply chain risk. The COVID-19 pandemic revealed how dependent companies were on a single manufacturer or manufacturing region. The benefits of consolidating production may no longer outweigh the risks.
Both nearshoring and reshoring are gaining traction. Mexico and Canada have dramatically improved their production capabilities. Using modern technology platforms, companies can manufacture at several locations simultaneously, thanks to new software applications. Thus, companies can ensure production continues despite unknown risks that may affect any site, but rarely all.
Integrate and Use APIs
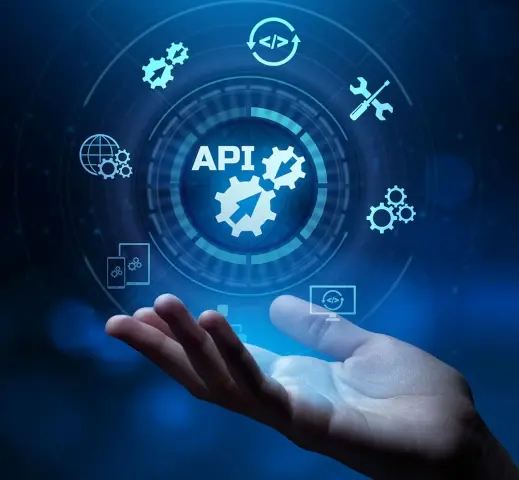
Application Programming Interfaces (APIs) are crucial for enabling software interoperability. It’s not always feasible for companies to develop all the software capabilities they need in-house. APIs enable organizations to leverage the expertise and investments of others. Additionally, they provide access to valuable information that is otherwise difficult to obtain.
Similarly, supply chain leaders should integrate functions within their supply chains (i.e., promote internal interoperability). It is essential for data and decisions to flow seamlessly between product management, engineering, procurement, and production. To accomplish this, new software applications may need to be adopted that cover the entire electronic production process.
Manage and Reduce Costs
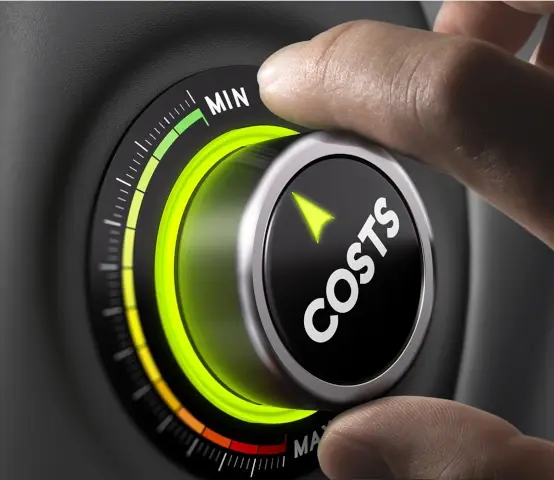
Finally, companies must manage costs wherever possible. Cash flows are vulnerable during uncertain times, like what we’re currently navigating. Implementing cost-saving measures today can protect the business over the long run.
Examples of cost-saving measures include revisiting service-level agreements, logistics contracts, and supplier relationships. Teams also need to think ahead to where they will cut costs first in the event of a downturn to conserve cash.
Comprehensive Risk Management Starts Today
Together, the eight tactics described here represent a comprehensive risk mitigation playbook. It’s not enough to pick and choose from this list. Our electronic supply chains have changed fundamentally in the last few years. Therefore, it makes sense that how we run our supply chains also has to change. Future supply chain success requires new technologies, more data, automation, and open collaboration. The good news is that there is still time to prepare for 2023 and beyond.
Related Topics
Preparing for Potential Supply Chain Disruptions During Lunar New Year
This blog discusses on how to prepare for unexpected events for global supply chains such as the dockworker strike in preparation for Lunar New Year.
Mapping Out a PCBA Supply Chain Strategy in Five Moves
Companies should create unique vendor relationships with numerous international suppliers due to the necessity of having to source components globally.
MacroFab’s Modern Approach to Strategic Sourcing
Many Contract Manufacturers (CMs) and Original Equipment Manufacturers (OEMs) have some sort of procurement team. So what makes MacroFab so different?
Want more information on this topic?
Download our White Paper on How Electronics Supply Chains Have ChangedAbout MacroFab
MacroFab offers comprehensive manufacturing solutions, from your smallest prototyping orders to your largest production needs. Our factory network locations are strategically located across North America, ensuring that we have the flexibility to provide capacity when and where you need it most.
Experience the future of EMS manufacturing with our state-of-the-art technology platform and cutting-edge digital supply chain solutions. At MacroFab, we ensure that your electronics are produced faster, more efficiently, and with fewer logistic problems than ever before.
Take advantage of AI-enabled sourcing opportunities and employ expert teams who are connected through a user-friendly technology platform. Discover how streamlined electronics manufacturing can benefit your business by contacting us today.