MacroFab Blog
The development of a new electronic system goes through several project stages on the way to revenue recognition. After designing and prototyping a system for proof of operation across all variances, the last milestone is to execute a production build of the final design within a contract manufacturing (CM) environment. Fingers should not be crossed at this point. All details needed for manufacturing in volume should be completed and all issues vetted by the project team. Unfortunately, many new projects get to the first production build step and still encounter new problems that cause the build to fail any number of required metrics. Let’s review ten top reasons why first production builds could fail at the late stage of new product development. Steps for problem mitigation will be offered as potential solutions.
Incomplete Assembly Instructions
The first most common production build problem is that manufacturing documentation can be either poorly written or missing entirely. Assembly instructions need to be clear to the point that a new operator can read and understand the process without issue. Anything that is left open to interpretation has the potential to be done incorrectly or in a different way than intended. Any omission of key documentation in other areas will also require the manufacturer to interpolate the missing information based on their judgment with the potential for error.
Finding a CM that incorporates digital manufacturing will allow you to upload these instructions to the platform. This creates a single source for all design files and documentation so they are readily available anytime your product needs to be re-ordered.
Poor Acceptance Criteria
A second problem occurs when the acceptance criteria requirements of all workmanship are not precise. Both the design engineering team and the contract manufacturer should agree on what is a failure and what is a passing device. If there is ambiguity in these criteria, the product has the potential to be less than optimal.
Early prototype builds and instruction review with the CM should have already identified the areas of highest concern for potential failures. These high-risk items should be documented in the acceptance criteria with actions for risk mitigation. The criteria should include both electrical and mechanical assembly items that have the potential for the issue of the final article. Instead of subjective requirements such as “screw shall be inserted until tight”, an objective description provides a more accurate measure of acceptance described as “screw shall be inserted with no less than 19 in-lb. and no more than 20 in-lb. of torque”.
Not Planning For Alternate BOM Components
A third potential issue may arise with a bill of materials (BOM) that does not properly provide alternate choices for all components. Ideally, each electrical or mechanical component of the system should have at least one alternate, but more available alternates, in this case, would be better. If any component within the BOM becomes obsolete, the only available sourcing option is for the CM to use a pre-chosen alternate component. When the availability of any component is prohibitively long, it may not be feasible to use the primary component within the BOM. In these cases, it is imperative that component alternates are available at the time of procurement. Without having them as an option, then a production build will likely have significant delays and logistics issues, even before any assembly begins.
Some CM’s can help you source alternate parts if you run into any of the aforementioned challenges. Finding a CM that can build resiliency into your supply chain can keep your production from experiencing delays.
Planning Unique Component Availability
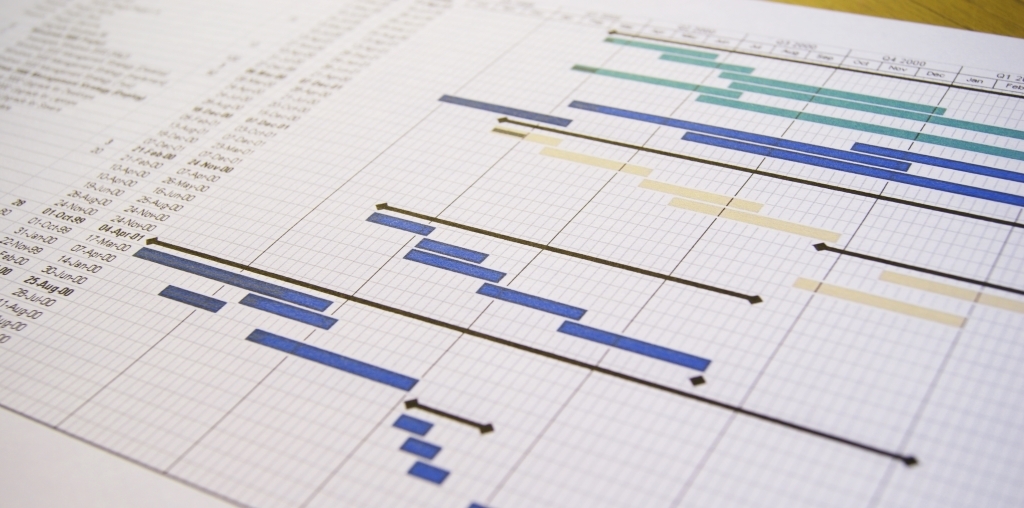
Another potential logistics challenge is to have a system that requires custom or unique components that are only sourced by one supplier. This can often be the case with advanced systems since performance components at the leading edge can typically only be supplied through a limited number of vendors. However, an assembly build may be caught short if the supplier is not able to deliver timely. If the supplier can provide a guaranteed supply or priority for your orders at the time of design, then this is ideal. If not, then you may need to consider carrying excessive inventory for these unique and custom components to bridge any potential hiccups that may occur in these supply chains.
Lead Times
Fifth, the largest cycle time of the first build will often be dictated by the aggregate lead times of all the components in the BOM. The lead times of all materials, PCB, mechanicals, components, custom, and unique parts and even software must be considered when planning cycle time. International customs must also be added as a known gate for logistics. Unplanned delays due to component lead-time availability will adversely impact the execution of a new production build. Many CM’s offer turnkey BOM kitting as a service for their assembly builds. The lead-time planning process should be thoroughly vetted and tested with prototype builds. Once volume production is achieved with recurring orders for materials, this becomes less of an issue, but the first production build is the most at risk when inventories have yet to be established.
Tolerances Stack Up
During the design phase, the system must consider both the electrical and mechanical tolerance across manufacturing variance. The stack-up of any mechanical errors in one direction can lead to interference at the time of assembly whereby a system cannot be fully assembled. Similarly, electrical tolerance across timing, supply, and temperature must all be considered within a complex design.
Consider whether the selected component tolerance can be accommodated within the system or if a higher quality component is needed with a tighter performance specification. Since one or two prototype builds may use parts from the same lots of material, these cannot be a sufficient means of testing all of the manufacturing variances that can be expected to be seen across the product life. These total variances must be known by the suppliers at the time of design in order to safeguard against corner cases where a system may fail or even be unfit for assembly.
Failure to Design Quality Specifications
A quality specification plan should be part of the development documentation set for the contract manufacturer. However, this includes not only the assembly but the quality expectations from component suppliers. The failure to design a quality specification during development can eventually be detrimental if anticipated quality issues arise during the first production build. The quality of components, materials, and assembly should not be assumed. These expectations should be explicitly set forth in formal documentation with the contract manufacturer. This includes any visual or x-ray testing that is needed on incoming materials to be used by the manufacturer before assembly.
Poor Factory Selection
During the product development cycle, the complexities of manufacturing new products should be well understood. The product should have a ‘design for manufacturing’ process that is followed during the design phase. The capabilities needed to execute a manufacturing plan should be recognized within that vetting process. By working with your contract manufacturer, a factory selected from their network should mirror those manufacturing requirements. Without having this requirements review, the potential exists for a poor factory selection. As every factory is tuned for a specific class of production, it is imperative that the factory class meets the needs of the product as each design is unique. Ideally, early prototype and pre-production builds should use the same factory or at least those with similar capabilities needed during volume production.
Over-Reliance on Human Experience
With the proper set of documentation instructions required by your manufacturer, your product should be able to be manufactured independently by any factory team. Reliance on specific human experience and tribal knowledge with key manufacturing members has the potential for future problems. If personnel is reorganized, this can derail a first manufacturing build and force development engineering to travel to fix a problem. Work with your contract manufacturer to gain agreement that your product development documentation can be internalized by a wide manufacturing pool and is not known only to one specific sub-team.
Assuming The CM Will Figure It Out
Lastly, there should not be any cases where there is the assumption that the factory will ‘figure it out’. This includes revisions to hardware, software, bill of materials, or documentation. There must be a commitment to clarity in communication with your CM on all levels. For example, many revisions of the product may have been tested during a prototyping phase that each requires something different to be done. For the first production build, the engineering team should start over from a complete baseline and not assume that the factory has any preconceived ideas as to what is needed to manufacture the final article. If anything is left open to an assumption based on prior work, there is the potential for mistake or error.
Conclusion
Success with a first production build comes down to planning and preparing for success with your contract manufacturing partner throughout the development cycle. It is a process that creates manufacturing capability for the product throughout the duration and will establish a repeatable process for easy re-orders. Without this work in advance, it is unreasonable to expect ‘everything to come together’. Taking the time to “slow down so you can speed up” will allow all pieces to fall into place for seamless manufacturing.
Finding a CM with a digital manufacturing component allows you to upload documentation in a common platform that is accessible to different departments within your organization as well as the CM and their teams. This reduces the risk of losing your documentation and makes for a more seamless transition should your manufacturing need to be moved to another factory within your CM’s network.
About MacroFab
MacroFab offers comprehensive manufacturing solutions, from your smallest prototyping orders to your largest production needs. Our factory network locations are strategically located across North America, ensuring that we have the flexibility to provide capacity when and where you need it most.
Experience the future of EMS manufacturing with our state-of-the-art technology platform and cutting-edge digital supply chain solutions. At MacroFab, we ensure that your electronics are produced faster, more efficiently, and with fewer logistic problems than ever before.
Take advantage of AI-enabled sourcing opportunities and employ expert teams who are connected through a user-friendly technology platform. Discover how streamlined electronics manufacturing can benefit your business by contacting us today.