MacroFab Blog
“The PCB supply chain has come under unprecedented strain, with surging material and energy costs, bottlenecks caused by resurgent post-Covid demand, disruption in China, and geopolitical uncertainty all creating a perfect storm.” —Supply Chain Resilience For PCB, Wevolver
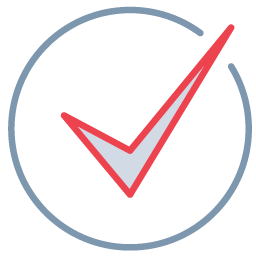
Checkpoint
Obsolescence adds complexity to the product life cycle and can be a pain point for designers and an area of risk for procurement.
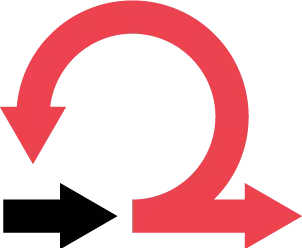
As the PCB supply chain continues to suffer unparalleled disruption, the electronics industry continues to accelerate.
Introduction, growth, maturity, decline, phase-out, and obsolescence are standard parts of the electronic product life cycle. However, with customers demanding newer, better products, the demand for new materials and components quickens, shortening the active component life cycle.
Although obsolescence can be considered a positive sign, a reflection of advancing technology, it adds complexity to the product life cycle and can be a pain point for designers and an area of risk for procurement. As the time between iterations continues to collapse, controlled obsolescence management becomes essential.
By implementing a few key rules and processes, you can safeguard against disruption and protect your costly designs.
Start Component Obsolescence Planning at Design
Component obsolescence planning can and should begin during the design process. Reviewing your Bill of Material (BOM) during the design phase gives you an opportunity to check for correct parts and incorrect values, as well as catch any outdated or aged parts.
Component obsolescence planning can and should begin during the design process. Reviewing your Bill of Material (BOM) during the design phase gives you an opportunity to check for correct parts and incorrect values, as well as catch any outdated or aged parts.
Although larger companies may have PCB librarians who would assist in monitoring, others may want to rely on a third-party library for this purpose. Whether you manage the process in-house or outsource it, auditing for obsolete parts during the design phase is critical to optimizing the life cycle of your products.
To audit for obsolete parts, you’ll want to look out for notifications the manufacturer may send out in warning that your part’s usefulness may be coming to an end.
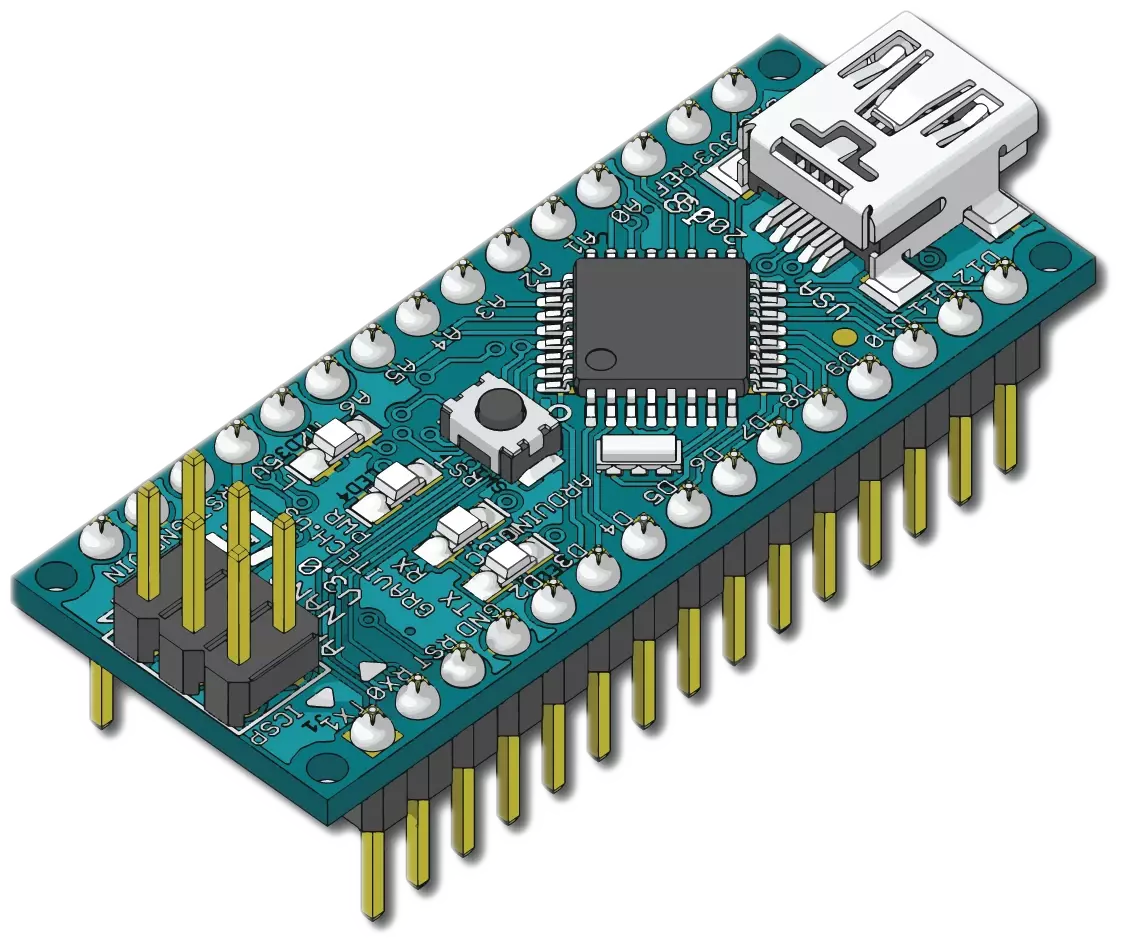
Product Discontinuance Notice (PDN), also referred to as End-of-Life, means the part will no longer be made available for sale or further supported. You likely won’t be advised of if or when you can place a final order. Product Change Notifications (PCNs) warn of changes that may impact your product, advising of updates to software or changes to function, process or quality improvements, raw material specifications, or even factory location. A PCN notification does not mean the part will be going obsolete. However, it is suggested that you obtain a sample of the replacement part and perform tests to confirm its continued suitability for your design. Last Time Buy notifications allow you the opportunity to enter final orders and advise of the date the factory must receive your order by.
BOM Review Best Practices: A Focus on Copied Circuitry
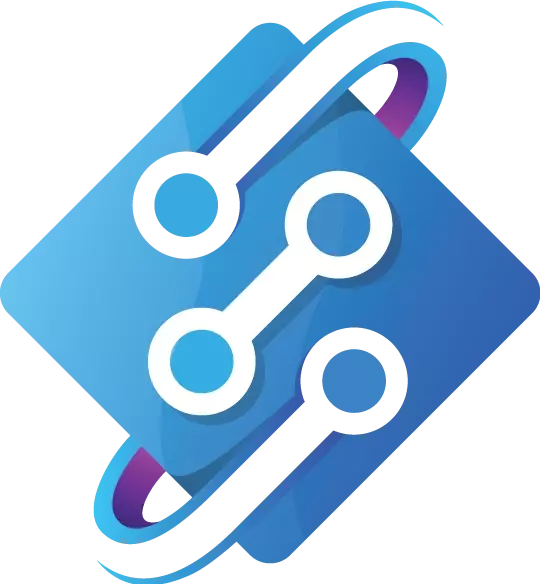
Copying circuitry can save you considerable time and comes with its benefits as you’re using proven design technology. But without a process for monitoring them, the parts you have come accustomed to relying on for a multitude of designs may suddenly become obsolete. It only takes one ‘bad’ part to quickly undo all those savings if the parts you are copying over are aged and at risk of obsolescence. So, slow down and carefully review your copied circuitry.
Review Existing BOMs for Critical Data
Your older designs may be missing critical data required for proper sourcing. So, it’s a good idea to review BOMs of older designs, making sure they’re clear, accurate, and include all essential data required to source alternatives that meet all form, fit and functional requirements.
Network with Your Supply Chain
As chip manufacturers are running on short supply due to the semiconductor shortage, regularly communicating with your distributors and component manufacturers, especially those who supply you with older, high-risk parts, is imperative. They should be able to send you alerts and provide you with projections on the specific parts you need for your circuit boards.
Keep Your Schematics Clean
PCB designs with unreadable schematics can bring a host of component management issues.
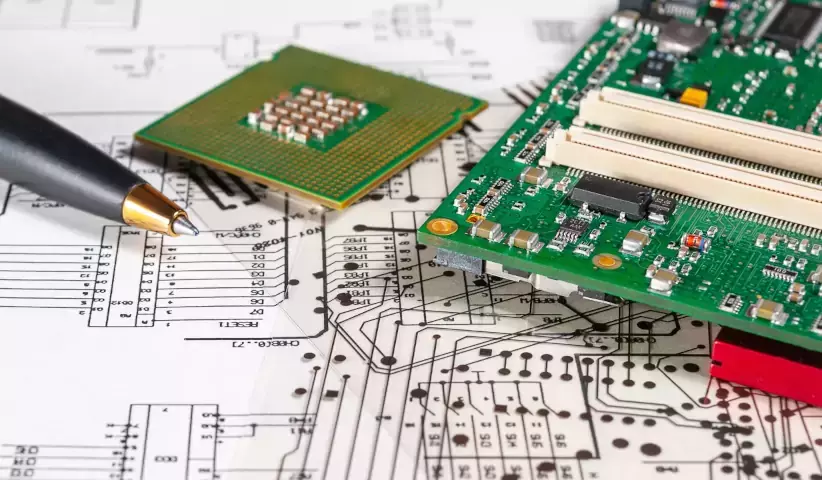
Passive parts are highly prone to issues. Due to their size, it’s easy for them to fall under the radar and be left unclearly or incorrectly marked. And as they’re often part of standard circuits and therefore copied into new designs, the issue can quickly propagate. Hence, it’s important to ensure all legacy design parts, even the small passive ones, are accurately marked and easily identifiable.
Establish Secondary Parts
Protect yourself by getting ahead of the game and ensuring timely assembly completion by establishing secondary parts for each of your BOM components. Your contract manufacturers (CMs) should be able to assist with this and more.Leverage the Power of Your CM
Conquer supply chain challenges, maintain obsolete inventory, and weather disruptions with a proactive approach that leverages our expertise.
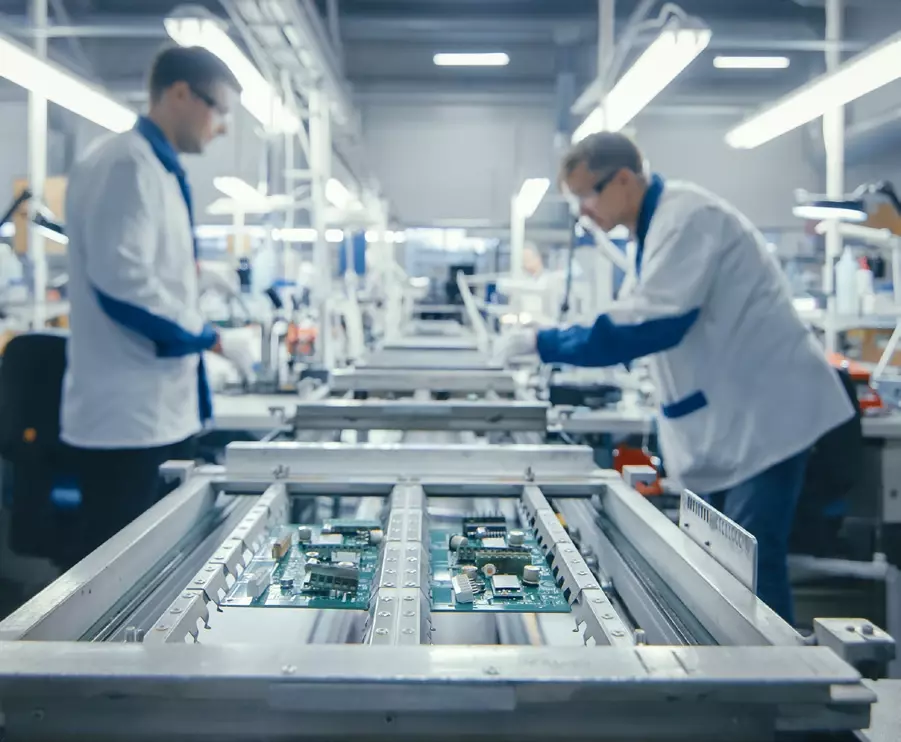
Although you may be performing some of your own due diligence, BOM complexity can make managing obsolete components a high resource activity. Your CM can offer you another layer of protection, helping relieve some of the workload of ensuring all components are available prior to build and assist you in identifying and planning for obsolescence.
While components planned for obsolescence come with clear, written warnings—including PDNs and PCNs—managing unplanned component obsolescence may sometimes require more esoteric knowledge. For example, the 5G rollout has led to issues with 3G-compatible devices as wireless carriers begin to drop 3G service.
A trustful CM partner will help you keep you up to date and better manage these harder-to-identify risks as well.
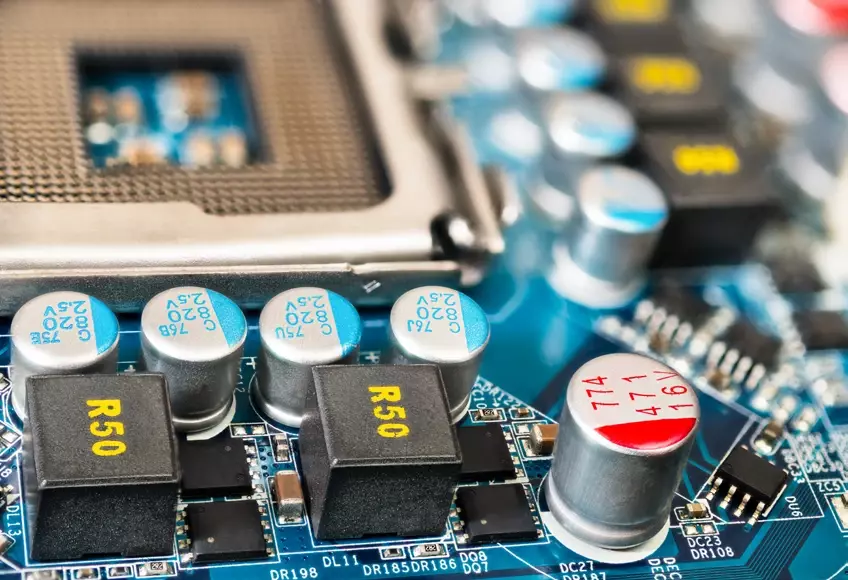
- With MacroFab’s planning tool, secondary BOM components can be identified during the design planning phase and alert of life cycle issues. By analyzing your product life cycle we can plan for obsolescence ahead of time and recommend longer-life parts.
- To further help you sidestep any surprises, MacroFab can help you build a plan to maintain continuous sourcing for all your necessary parts. Working with their extensive, trusted network of supply partners, our sourcing team can help you monitor the status and availability of your critical parts, make recommendations, and, should the need arise, source the best parts at the best possible price.
- Our PCB design engineers and Firmware development team have years of expertise. If we’re unable to find suitable fit, form, and function alternates, we can suggest available components and help you modify or redesign PCB modules using vetted, active components with firmware development if required.
Reduce risk, improve buying outcomes, and extend your product life cycles.
No matter the situation, our component engineers will work collaboratively with you to find the optimal solution to your obsolete part problem and ensure you meet your deadlines and project budget.
Related Topics
Preparing for Potential Supply Chain Disruptions During Lunar New Year
This blog discusses on how to prepare for unexpected events for global supply chains such as the dockworker strike in preparation for Lunar New Year.
Mapping Out a PCBA Supply Chain Strategy in Five Moves
Companies should create unique vendor relationships with numerous international suppliers due to the necessity of having to source components globally.
MacroFab’s Modern Approach to Strategic Sourcing
Many Contract Manufacturers (CMs) and Original Equipment Manufacturers (OEMs) have some sort of procurement team. So what makes MacroFab so different?
Ready to simplify your sourcing and better manage your obsolescence while mitigating your risks?
More On Our Strategic Sourcing SolutionsAbout MacroFab
MacroFab offers comprehensive manufacturing solutions, from your smallest prototyping orders to your largest production needs. Our factory network locations are strategically located across North America, ensuring that we have the flexibility to provide capacity when and where you need it most.
Experience the future of EMS manufacturing with our state-of-the-art technology platform and cutting-edge digital supply chain solutions. At MacroFab, we ensure that your electronics are produced faster, more efficiently, and with fewer logistic problems than ever before.
Take advantage of AI-enabled sourcing opportunities and employ expert teams who are connected through a user-friendly technology platform. Discover how streamlined electronics manufacturing can benefit your business by contacting us today.