MacroFab Blog
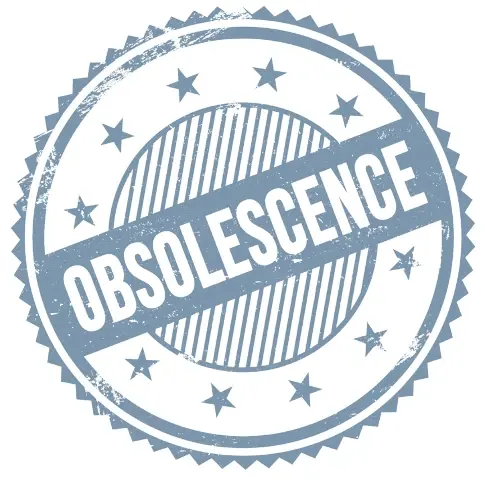
Component obsolescence is a major challenge for industries relying on electronics. Electronic parts go out of date fast - two to five years on average - and 15 percent disappear from the market annually. Outdated components harm product quality, reliability, and profitability, forcing several times more expensive due to limited supply, demand, counterfeit risks, or redesign. Thus, proactive obsolescence management, starting with product design, is crucial.
In this article, we will explore some of the reasons for component obsolescence, some of the best practices for managing it effectively, and some of the benefits of partnering with a supply chain expert who can help you mitigate obsolescence risks and maximize product value.
Reasons for Component Obsolescence
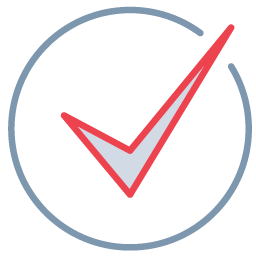
Checkpoint
Fifteen percent of electronic parts disappear from the market annually.
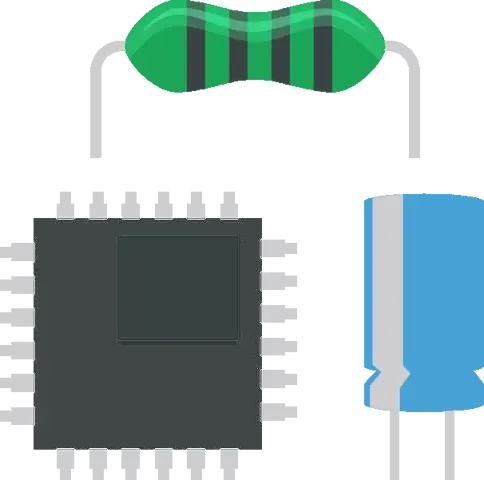
It is essential to understand the factors contributing to component obsolescence, which is a growing challenge for companies within the electronics industry.
One significant reason for component obsolescence is the rapid pace of technological innovation and development in the industry. This trend is shortening the life cycles of integrated circuits (ICs) by an average of 30 percent. A study by S&P Global Market Intelligence revealed that over 50 percent of ICs have a lifespan shorter than five years.
Another contributing factor is the increasing consolidation and competition in the upstream supply chain through mergers and acquisitions (M&A). This trend has led to more end-of-life (EOL) notifications and faster product life cycle changes. In fact, M&A activity is currently affecting over 200 billion components worldwide, according to IHS Markit.
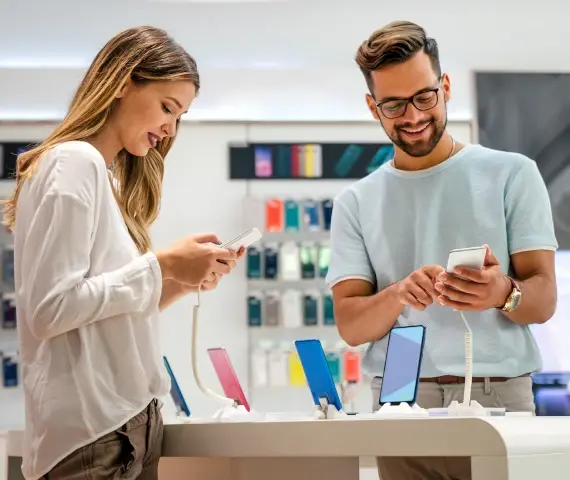
Additionally, consumer demand for newer and smarter electronic products is driving more frequent upgrades and replacements of existing devices. For example, a recent survey by Accenture found that 47 percent of consumers plan to replace their smartphones every year or sooner.
Changes in government regulations and environmental standards also have a significant impact on component availability and compatibility. The Restriction of Hazardous Substances (RoHS) directive, for instance, prohibits the use of certain substances such as lead, mercury, or cadmium in electrical and electronic equipment sold in the European Union.
These factors pose significant challenges for companies that must ensure product designs are functional, reliable, compatible, compliant, and profitable throughout their intended life span. As an industry professional, it is crucial to keep up with these trends and their implications to make informed decisions about product design and component selection.
Best Practices for Component Obsolescence Management
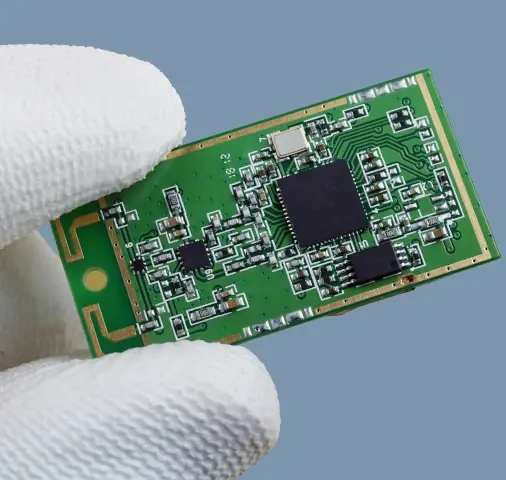
To avoid or minimize the negative impact of component obsolescence on products and systems, it’s essential to adopt an obsolescence management strategy during the product design phase. This involves incorporating best practices such as specifying components with long-term availability or multiple sources, leveraging production and order history to anticipate component turnover, communicating with end users to align design with customer expectations, maintaining regulatory compliance, and incorporating design-for-obsolescence strategies to ensure product longevity.
To reduce the risk of sourcing difficulties and price fluctuations due to limited supply or high demand, specify components that have long-term availability or have multiple sources for all necessary parts. For instance, choose to use components that are commonly found in other industries like automotive or aerospace, to ensure a stable supply chain. While this creates competition for their purchase, it also ensures they remain readily available, typically from multiple sources, as long as they remain in high demand. When you can’t use these strategies, use best practices to reduce single-source component risks.
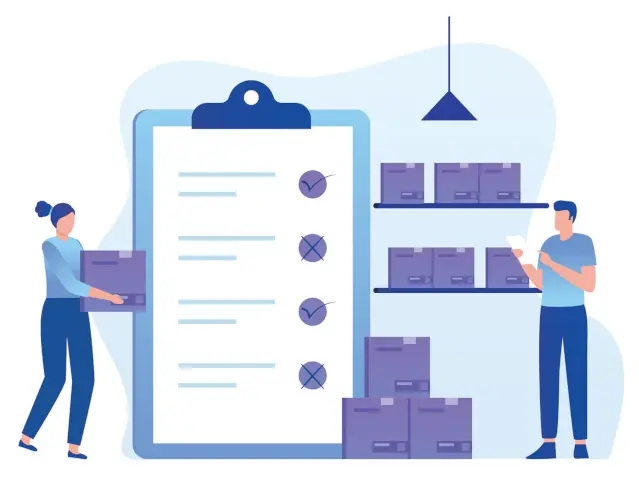
Leverage production and order history data to gain visibility into component turnover rates and identify parts that are at risk of becoming obsolete or slow-moving. Plan accordingly for inventory management or replacement strategies. Additionally, use data analytics to monitor the usage and performance of components and forecast their life expectancy to stay ahead of potential obsolescence. MacroFab’s technology platform is ideally suited to provide this sort of analytical data.
Communicating with end-users to understand their needs and expectations regarding product longevity is crucial in ensuring that product design aligns with their requirements. By preventing premature obsolescence, unnecessary costs and dissatisfaction can be avoided.
Maintaining regulatory compliance requirements and forecasting their impact on parts in stock and production is essential in ensuring regulatory adherence, avoiding penalties or fines, and anticipating potential component availability or compatibility changes.
Listen to this classic Circuit Break podcast episode when Parker and Stephen chat will Bil Herd, one of the lead hardware designers for the Commodore C128, about his experiences with through hole circuit design (among other things.)
Options to Consider at the Design Stage
Design-for-obsolescence strategies such as modularization, standardization, upgradability, and reusability can enhance product flexibility, adaptability, and maintainability, ultimately extending product life span. Below are explanations of each strategy and how to use it:
Modularization: This strategy involves designing products as a series of independent modules that can be easily replaced or upgraded. By doing so, end users can replace only the faulty or outdated module instead of buying a completely new device. This results in cost savings for the end user and reduces electronic waste. To implement modularization, design teams should identify the components that are most likely to become obsolete and design them as interchangeable modules.
Standardization: This strategy involves using standard components and interfaces that are compatible with other products. For example, using USB ports for charging and data transfer instead of proprietary connectors. Standardization allows for greater interoperability between products, making it easier for end-users to replace or upgrade components. This strategy also makes it easier for manufacturers to source components and will ultimately reduce costs.
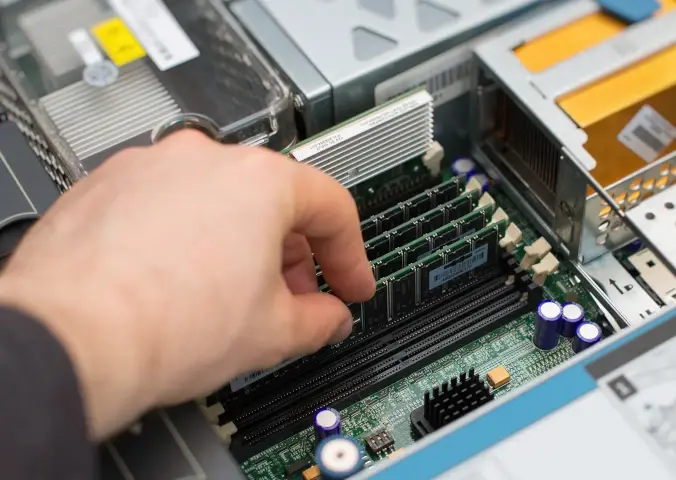
Upgradability: This strategy involves designing products with the ability to upgrade specific components, such as RAM or storage. This extends the lifespan of the product and provides cost savings for the end user. Design teams should identify the components that are most likely to need upgrading and design the product with this in mind.
Reusability: This strategy involves designing products with the ability to repurpose them after their initial use– for example, repurposing an old smartphone as a security camera. By designing products with reusability in mind, companies can reduce waste and possibly create new revenue streams by meeting two demands with one product. Design teams should identify potential secondary uses for the product and design it with these in mind.
By implementing these design-for-obsolescence strategies, electronic industry professionals can create more sustainable products that offer cost savings for end-users and reduce environmental impact. These strategies also align with ESG initiatives, making them a worthwhile investment for companies looking to improve their sustainability performance.
Benefits of Partnering with a Supply Chain Expert
Effectively managing component obsolescence requires expertise, resources, and time that many businesses may not have internally. A supply chain expert offering obsolescence management services can be beneficial. These services include optimizing inventory levels, improving quality and customer satisfaction, and providing business intelligence and decision-making support.
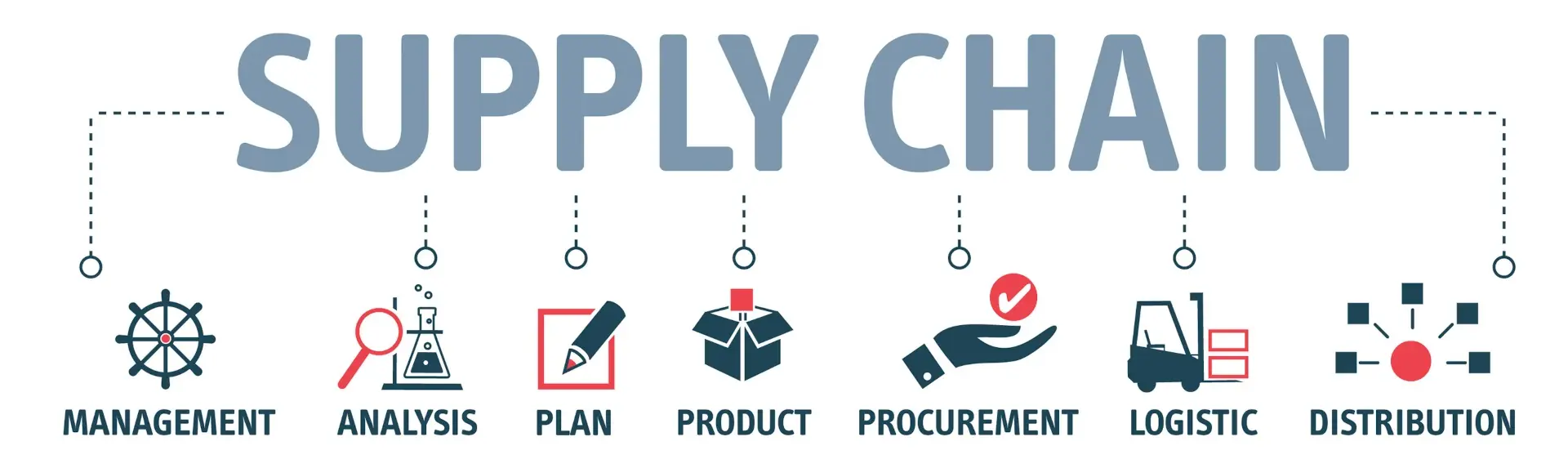
Optimizing inventory levels, reducing waste, and avoiding disruptions or delays in production or delivery can save costs and increase profits. For instance, companies can implement inventory optimization software that analyzes demand patterns and optimizes stock levels, reducing inventory carrying costs.
Ensuring product performance, reliability, and safety is critical for improving quality and customer satisfaction. Businesses can achieve this by implementing a quality management system that monitors and controls processes and activities affecting quality throughout the supply chain.
Providing business intelligence tools that track and record geographical and financial data about sales and help optimize supply chain strategy can enhance business intelligence and decision-making. The result can be an increase in sales and profitability for companies.
Getting help with obsolescence management from a supply chain expert can allow companies to focus on their core competencies, reduce costs, improve quality, enhance customer satisfaction, and grow their business. Companies can achieve their business objectives and manage component obsolescence effectively by partnering with a supply chain partner.
Conclusion
Component obsolescence is inevitable in today’s dynamic electronics industry. However, it does not have to threaten product success if companies adopt a proactive obsolescence management strategy that begins at the design stage. Your business can mitigate obsolescence risks and maximize product value throughout its life cycle by following some best practices and partnering with a supply chain expert offering comprehensive solutions.
Related Topics
Preparing for Potential Supply Chain Disruptions During Lunar New Year
This blog discusses on how to prepare for unexpected events for global supply chains such as the dockworker strike in preparation for Lunar New Year.
Mapping Out a PCBA Supply Chain Strategy in Five Moves
Companies should create unique vendor relationships with numerous international suppliers due to the necessity of having to source components globally.
MacroFab’s Modern Approach to Strategic Sourcing
Many Contract Manufacturers (CMs) and Original Equipment Manufacturers (OEMs) have some sort of procurement team. So what makes MacroFab so different?
About MacroFab
MacroFab offers comprehensive manufacturing solutions, from your smallest prototyping orders to your largest production needs. Our factory network locations are strategically located across North America, ensuring that we have the flexibility to provide capacity when and where you need it most.
Experience the future of EMS manufacturing with our state-of-the-art technology platform and cutting-edge digital supply chain solutions. At MacroFab, we ensure that your electronics are produced faster, more efficiently, and with fewer logistic problems than ever before.
Take advantage of AI-enabled sourcing opportunities and employ expert teams who are connected through a user-friendly technology platform. Discover how streamlined electronics manufacturing can benefit your business by contacting us today.